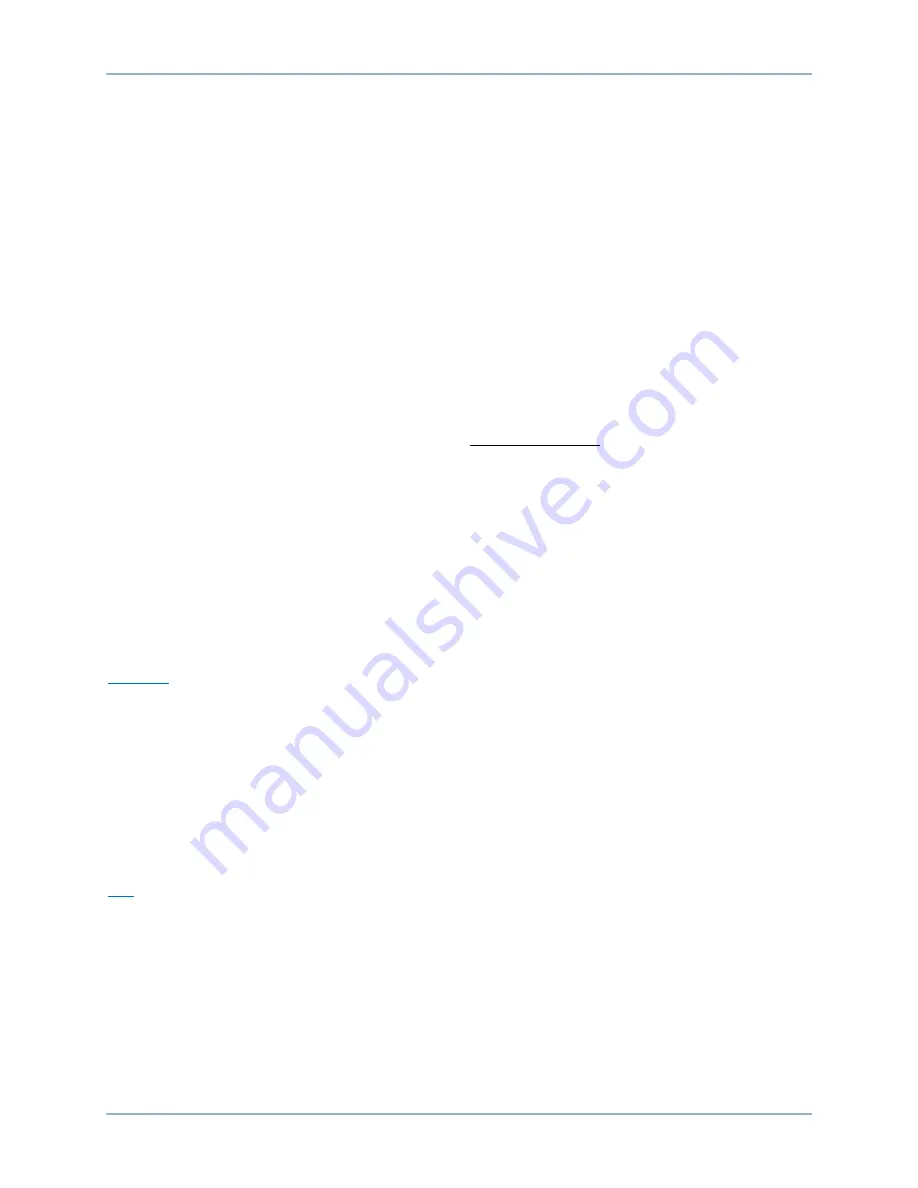
9424200996
20-5
BE1-11
m
Thermal Curve (49TC) Protection
TCU = Present Thermal Capacity
TCU
end
= Thermal Capacity that the motor will eventually reach if current is maintained at present
magnitude.
TCU
start
= Thermal Capacity
T
= Time since last calculation
τ
= Cooling time constant (either running or stopped)
RTD Biasing and Hot/Cold Safe Stall Ratio
The thermal overload curves are based on the assumption of a normal 40
°
C ambient and normal motor
cooling. In the case of unusual ambient temperature or blocked or reduced motor cooling, the optional
installed RTDs can be used to improve the estimation of thermal capacity.
The user provides a curve showing RTD thermal capacity used. The curve includes a minimum of three
points and a maximum of 40 points. Three typical points are Ambient RTD Temperature (40
°
C) and 0%
TC, Full Load Amps running RTD temperature and thermal capacity, and Maximum Safe Stator RTD
temperature (typically 155
°
C).
Equation 20-7 is used to calculate the Full Load Amp thermal Capacity.
RTD Bias TCU =
�
1
−
hot safe stall time
cold safe stall time
�
Equation 20-7. RTD Bias TCU
RTD Bias TCU is linearly interpolated when RTD temperature is between defined temperatures.
When the 49TC is in overload and the RTD Bias TCU is higher than the current-based TCU, RTD Bias
TCU is used to update the 49TC thermal capacity. The current based model continues to calculate
thermal capacity from this new bias level. RTD Bias TCU alone will not result in a thermal model trip.
Current must be above the thermal model current pickup.
Overload and Trip
The Overload output occurs first, followed by the Trip output.
Overload
The 49TC pickup level is determined by the Overload setting along with the Service Factor and Full Load
Amps settings located on the System Parameters, Motor Configuration screen in BESTCOMS
Plus
. The
Overload output becomes true when the equivalent thermal current increases above the pickup current.
In BESTlogic
Plus
, the Overload output can be connected to other logic elements to annunciate the
condition, control other elements in logic, and start the fault recorder (logic element FAULTTRIG).
Assertion of the Overload output initiates a timer that begins timing to a thermal trip. The duration of the
timer is established by the thermal curve.
If the pickup condition subsides before the element delay expires, the timer and Overload output are
reset, no corrective action is taken, and the element is rearmed for any other overload conditions.
Trip
The Trip output becomes true if an overload condition exists for the duration of the element timer. In
BESTlogic
Plus
, the Trip output can be connected to other logic elements and to a physical relay output to
annunciate the condition and to initiate corrective action. If a target is enabled for the element, the BE1-
11
m
will record a target when the Trip output becomes true. See the
Fault Reporting
chapter for more
information about target reporting.
Emergency Start
When performing an emergency start, the Max Emergency Thermal Capacity setting determines the
maximum thermal capacity allowed. An emergency start is requested when the Emergency input of the
Motor Status logic block is true. The emergency start condition remains until the thermal capacity drops
Summary of Contents for BE1-11m
Page 8: ...vi 9424200996 Revision History BE1 11m...
Page 12: ...x 9424200996 Contents BE1 11m...
Page 21: ...9424200996 1 9 BE1 11m Introduction Figure 1 1 Style Chart...
Page 22: ...1 10 9424200996 Introduction BE1 11m...
Page 40: ...3 6 9424200996 Controls and Indicators BE1 11m Figure 3 3 Front Panel Display Setup Screen...
Page 54: ...5 6 9424200996 Phase Undervoltage 27P Protection BE1 11m...
Page 56: ...6 2 9424200996 Negative Sequence Voltage 47 Protection BE1 11m...
Page 61: ...9424200996 7 5 BE1 11m Phase Overvoltage 59P Protection Figure 7 3 Overvoltage Settings Screen...
Page 62: ...7 6 9424200996 Phase Overvoltage 59P Protection BE1 11m...
Page 68: ...8 6 9424200996 Auxiliary Overvoltage 59X Protection BE1 11m...
Page 80: ...12 4 9424200996 Instantaneous Overcurrent 50 Protection BE1 11m...
Page 84: ...13 4 9424200996 Breaker Failure 50BF Protection BE1 11m...
Page 92: ...14 8 9424200996 Inverse Overcurrent 51 Protection BE1 11m...
Page 105: ...9424200996 18 3 BE1 11m Power Factor 55 Protection Figure 18 2 Power Factor Settings Screen...
Page 106: ...18 4 9424200996 Power Factor 55 Protection BE1 11m...
Page 110: ...19 4 9424200996 Resistance Temperature Detector 49RTD Protection BE1 11m...
Page 118: ...20 8 9424200996 Thermal Curve 49TC Protection BE1 11m...
Page 122: ...22 2 9424200996 Starts per Time Interval 66 Protection BE1 11m...
Page 124: ...23 2 9424200996 Restart Inhibit Protection BE1 11m...
Page 140: ...28 4 9424200996 Breaker Control Switch 101 BE1 11m...
Page 148: ...29 8 9424200996 Setting Groups BE1 11m...
Page 156: ...30 8 9424200996 Metering BE1 11m Figure 30 11 RTD Meter Screen...
Page 158: ...31 2 9424200996 Digital Points BE1 11m Figure 31 2 Digital Points Monitor Screen...
Page 177: ...9424200996 34 5 BE1 11m Motor Reporting Figure 34 9 Learned Motor Data Screen...
Page 178: ...34 6 9424200996 Motor Reporting BE1 11m...
Page 184: ...35 6 9424200996 Alarms BE1 11m...
Page 186: ...36 2 9424200996 Differential Reporting BE1 11m...
Page 196: ...38 4 9424200996 Demands BE1 11m...
Page 198: ...39 2 9424200996 Load Profile BE1 11m...
Page 208: ...41 6 9424200996 Trip Circuit Monitor 52TCM BE1 11m...
Page 212: ...42 4 9424200996 Fuse Loss 60FL BE1 11m...
Page 218: ...43 6 9424200996 BESTnet Plus BE1 11m Figure 43 8 Power Quality Page...
Page 221: ...9424200996 44 3 BE1 11m Mounting Figure 44 3 Case Side Dimensions...
Page 235: ...9424200996 45 5 BE1 11m Terminals and Connectors Figure 45 7 Example of Reversed CT Polarity...
Page 236: ...45 6 9424200996 Terminals and Connectors BE1 11m...
Page 269: ...9424200996 48 15 BE1 11m BESTlogic Plus Figure 48 4 Logic Page 1 for Default Logic...
Page 288: ...49 10 9424200996 Communication BE1 11m Figure 49 14 Modbus Mapping Screen...
Page 306: ...52 4 9424200996 Device Information BE1 11m...
Page 314: ...53 8 9424200996 Configuration BE1 11m Figure 53 3 Display Units Screen...
Page 318: ...54 4 9424200996 Introduction to Testing BE1 11m...
Page 330: ...56 6 9424200996 Commissioning Testing BE1 11m...
Page 336: ...58 4 9424200996 Phase Undervoltage 27P Test BE1 11m...
Page 340: ...59 4 9424200996 Phase Overvoltage 59P Test BE1 11m...
Page 352: ...60 12 9424200996 Auxiliary Overvoltage 59X Test BE1 11m...
Page 360: ...61 8 9424200996 Frequency 81 Test BE1 11m...
Page 364: ...62 4 9424200996 Instantaneous Undercurrent 37 Test BE1 11m...
Page 376: ...63 12 9424200996 Instantaneous Overcurrent 50 Test BE1 11m...
Page 396: ...65 16 9424200996 Inverse Overcurrent 51 Test BE1 11m...
Page 408: ...67 6 9424200996 Power 32 Test BE1 11m...
Page 412: ...68 4 9424200996 Loss of Excitation Reverse Var Based 40Q Test BE1 11m...
Page 426: ...70 10 9424200996 Thermal Curve 49TC Test BE1 11m...
Page 432: ...72 4 9424200996 Starts per Time Interval 66 Test BE1 11m...
Page 436: ...73 4 9424200996 Restart Inhibit Test BE1 11m...
Page 440: ...74 4 9424200996 Virtual Control Switches 43 Test BE1 11m...
Page 450: ...75 10 9424200996 Logic Timers 62 Test BE1 11m...
Page 464: ...79 8 9424200996 Troubleshooting BE1 11m...
Page 480: ...80 16 9424200996 Specifications BE1 11m...
Page 600: ...84 56 9424200996 Settings Calculation Examples BE1 11m Figure 84 70 Logic Page 4 Part 1...
Page 602: ...84 58 9424200996 Settings Calculation Examples BE1 11m...
Page 608: ...85 6 9424200996 BESTCOMSPlus Settings Loader Tool BE1 11m...
Page 609: ......