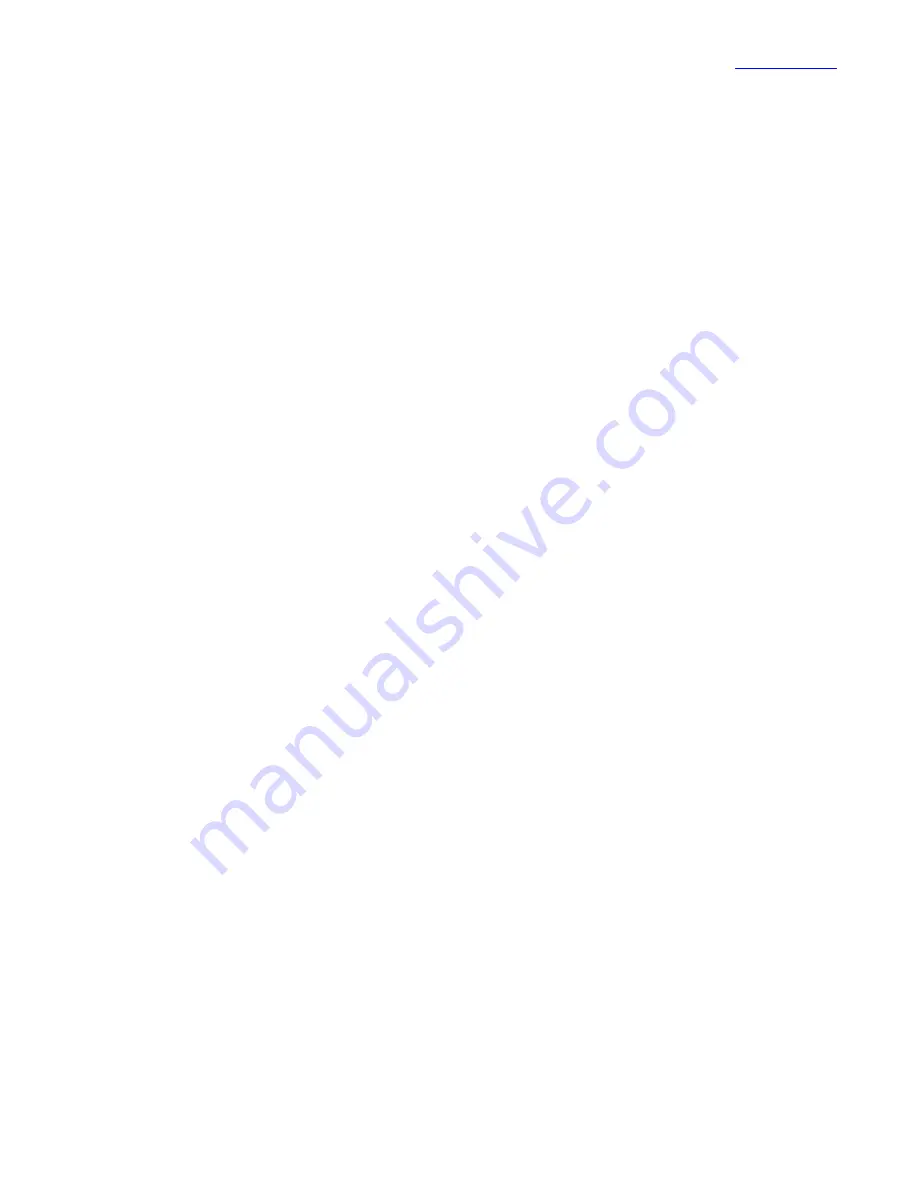
Wraptor™ User Manual
www.barrett.com
© 2007 Barrett Technology®, Inc.
Document: D2000, Version: AB.00
Page 6 of 15
2 Safety and Cautions
PLEASE READ THIS SECTION IN ITS ENTIRETY BEFORE USING YOUR WRAPTOR™.
Following these safety instructions will help prevent user injury and equipment damage.
2.1 Human Safety
•
The Wraptor™ has been designed to apply human-scale maximum active forces of several kilograms even though the
Wraptor™ is designed to lift 50 kg once the fingers have secured their grasp. HOWEVER, the safety of the Wraptor™
is limited by the system safety, including the arm, which may be capable of tons of force. If the arm that transports the
Wraptor™ is able to move, then the end user must be aware that the Wraptor™ is capable of (and will) transmit the
arm’s end forces directly to people and delicate equipment. If an articulated robotic arm is rated for 50 kg, for example,
it is likely to be able to produce many tons of force in many leveraged configurations or when it is moving fast upon an
impact.
•
Beware of situations when the Wraptor™ is stationary and secured on the end of a high-payload robot, but there is other
active moving equipment nearby. The Wraptor™ generally will not accommodate and reduce the force of any collision,
if it occurs.
•
Do not place any part of your body or delicate objects within the grasp of the Wraptor™ without first verifying control
of the unit and confirming appropriate force levels.
•
Beware that the sharp finger-nail like claws attached nominally to the outer links can cause pain and possibly cut bare
human skin depending on details of the grasp.
2.2 Wraptor Safety
•
Do not connect or disconnect any electrical cables while the Power Supply is turned on. Failure to follow this instruction
could impart irreparable damage to the onboard electronics.
•
Ensure that input power to the Positive- and Negative-voltage terminals are never reversed.
•
Never allow power to be connected to the communication pins at the input connector of the Wraptor
•
Do not exceed the load limit of the fingers, 50kg per finger. Consider all loading situations including accelerated loads,
cantilever loads from long objects, robot collisions, active loads, etc. (See also, next paragraph.)
•
Similar to the concerns about Human safety when the Wraptor™ is mounted on a robotic arm, one must recognize that,
for example, a 50-kg lift robotic arm is easily capable of producing several tons (!!!) of force even when moving slowly
(in many configurations with high mechanical leverage) or when moving quickly just before a collision (regardless of
configuration). Since forces cannot be seen by eye, any contact with rigid surfaces or even with the base or other links of
the robotic arm can easily exceed tons of force without operator awareness. It is advisable to be very cautious when
running the full system to minimize these collisions or to ensure that a force/torque sensor or collision-break-away
mechanism is installed between the tool-plate of the robot and the base of the Wraptor™.
•
Do not allow the Wraptor™ to be exposed to corrosive liquids that may cause damage to the body or cable of the unit.
•
The operating temperature of the Wraptor™ is monitored continuously and automatically so that no Puck can approach
OTEMP, which is set nominally to 82 C. If the temperature reaches within 16C of OTEMP, then the max command
torque (motor current) will be temporarily limited to prevent damage. Under normal conditions, the Wraptor™ operates
between 35 and 60C. The Wraptor™ was designed with non-backdrivable finger joints to take advantage of the motors’
peak operating performance in short bursts. The spread, however, is backdrivable to aid in target-independent grasping
and requires constant motor current to actively hold position. Idling the spread motor (thus activating the spread brake),
when possible, will help keep the temperature lower.
•
Do not immerse the Wraptor™ in liquid.
•
Do not expose the Wraptor™ to corrosive liquids.
•
Do not expose the Wraptor™ to mud or slurries.
•
Ensure that the electrical Wraptor™ cable and connector cannot be damaged by collision, cutting, pulling, or twisting.