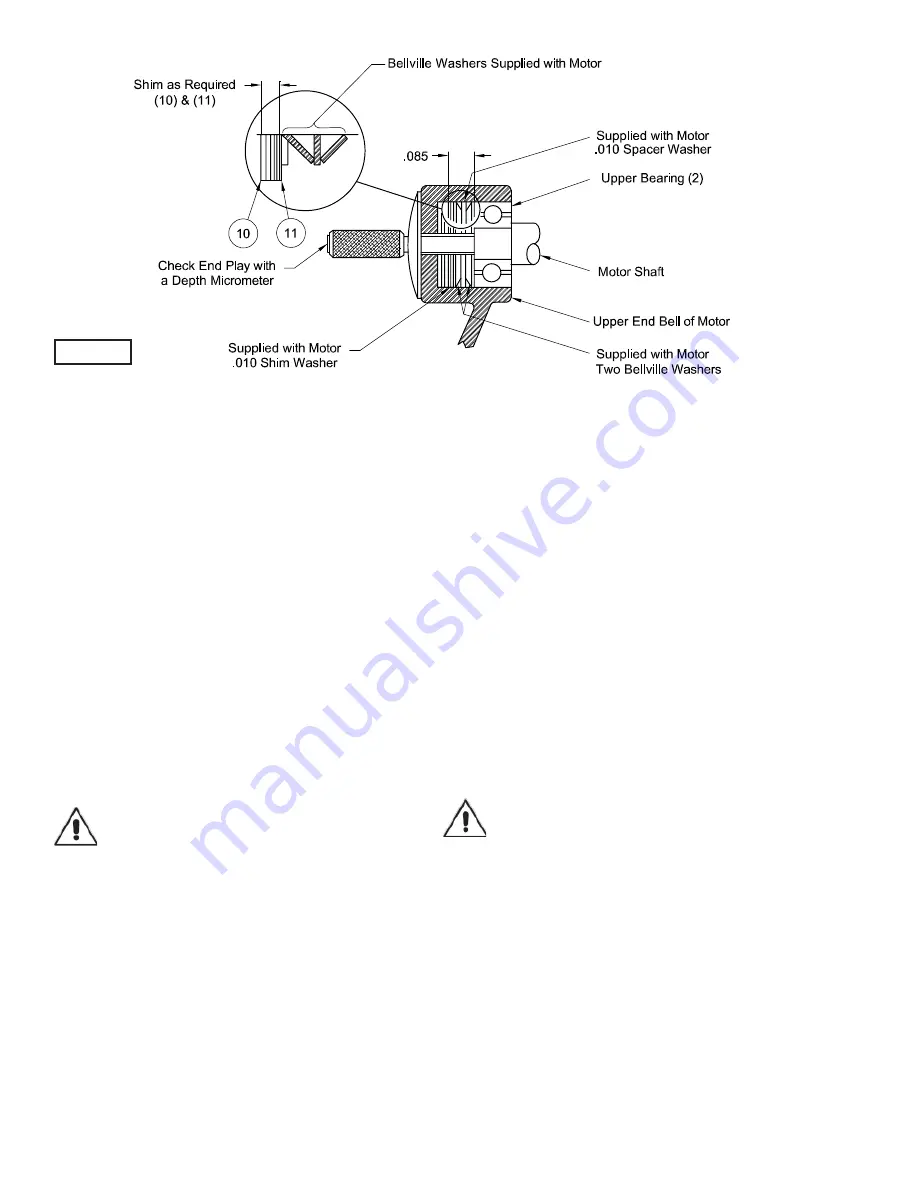
10
FIGURE 3
Vertically lift the outside motor housing (1) from bearing
bracket (4) with lifting strap (24). Inspect square ring (3) for
damage or cuts. Remove the upper motor bolts and lift upper
end bell from motor (47). Examine upper bearing (2) and
replace if required. If replacement is required, remove bearing
(2) from motor shaft using a wheel puller.
NOTE SPECIAL BELLVILLE WASHERS
in upper motor
housing required to compensate for shaft expansion. These
Bellville washers and spacer shims (10) and (11) must be
properly reinstalled to give the required constant down force
on the motor shaft. See Section F-3.3.
Vertically lift stator. Inspect winding for shorts and resistance.
To test the temperature sensor (if equipped), check for continu-
ity between the black and white wires. If found to be defective
contact a motor service station or Crane Pumps & Systems
service department. Pull motor rotor and lower bearing (5)
vertically from bearing bracket (4). Examine bearing (5) and
replace if required. If replacement is required, remove bear-
ing (5) from motor shaft using a wheel puller. Check rotor for
wear. If rotor or the stator windings are defective, the complete
motor must be replaced. While disassembled, check moisture
sensor wires (31), that they are secured to electrodes (29) with
lockwashers (34) and screws (33).
Important !
All parts must be clean before reassembly
.
F-3.2) Reassembly:
Bearings -
When replacing bearings, be careful not to
damage the rotor or shaft threads. (If so equipped, fi ll notch
should face the rotor core for both upper and lower bearings).
Clean the shaft thoroughly. Apply adhesive compound (42) to
the shaft and press bearing (5) on the motor shaft, position
squarely onto the shaft applying force to the inner race of the
bearing only, until bearing seats against shoulder of the shaft.
Reassemble top bearing (2) in the same manner.
Motor -
Slide lower bearing (5) and motor rotor squarely into
the bearing bracket (4) until bearing seats on the bottom.
Position motor housing and stator into pilot, install bellville
washers and shims (10) and (11) in upper end bell.
Position upper motor end bell aligning holes and thread cap
screws into bearing bracket (4). Torque to 16 ft. lb.. Place all
motor leads above the motor. Position square ring (3) over
bearing bracket (4) and lower housing (1) over motor and into
pilot, being sure to orient motor housing handle parallel to mo-
tor end bell reliefs. Apply thread locking compound (38) to cap
screws (6) threads and install with nut (7).Torque to 24 ft. lb.
F-3.3) Checking Of End-Play:
Measure distance with micrometer from the top surface of the
motor cover to the end of the shaft. See Figure 3. Temporar-
ily set the partially assembled unit on the lower end of the
shaft, causing the bearings to slide up in the bearing retainer.
When the bearings bottom securely, again measure the
distance from the top surface of the motor cover to the end
of the shaft. This difference should be between .015 to .030
inches. If the end-play is within these tolerances, proceed
with reassembly. If the end-play is not within the above listed
tolerances, the motor upper end bell must be disassembled
and suffi cient .010 shims (10) must be added or removed as
required. Reassemble and recheck again for the required
listed end-play tolerance.
F-4) Shaft Seal and Diaphragm Service:
Important! - Handle seal parts with extreme care.
do not scratch or mar lapped surfaces.
F-4.1) Disassembly and Inspection:
Diaphragm -
To examine or replace the diaphragm (14) or
shaft seal (12), remove impeller (48) as outlined in paragraph
F-2.1. Drain oil from seal chamber as outlined in paragraph
F-1.3. Remove cap screws (25) and lifting strap (24). Set unit
upside down on blocks to avoid damaging cords. Remove
socket head cap screws (17) and lift seal plate (13) vertically,
being cautious to avoid seal damage, together with diaphragm
(14), clamp (15) and outboard stationary member (12A) of
shaft seal (12), from bearing bracket (4). Examine diaphragm
(14), if it is ruptured, cracked or damaged, replace by removing
screws (16) and diaphragm clamp (15), Also, clean out vent
holes in seal plate (13). Check moisture sensor probes (29)
for damage. Replace by disconnecting wires (31) by removing
screws (33) and lockwashers (34). Then remove probe (29)
from bearing bracket (4).
Summary of Contents for BARNES 4DSE-L Series
Page 15: ...15 FIGURE 10 4DSE L Pump Series...
Page 16: ...16 FIGURE 11 4DSE L Pump Series...
Page 17: ...17 4DSE L Pump Series FIGURE 12...
Page 21: ...21 4DSE HL High Ef ciency Pump Series FIGURE 13...
Page 22: ...22 4DSE HL High Ef ciency Pump Series FIGURE 14...
Page 23: ...23 4DSE HL High Ef ciency Pump Series FIGURE 15...
Page 27: ...27 NOTE...