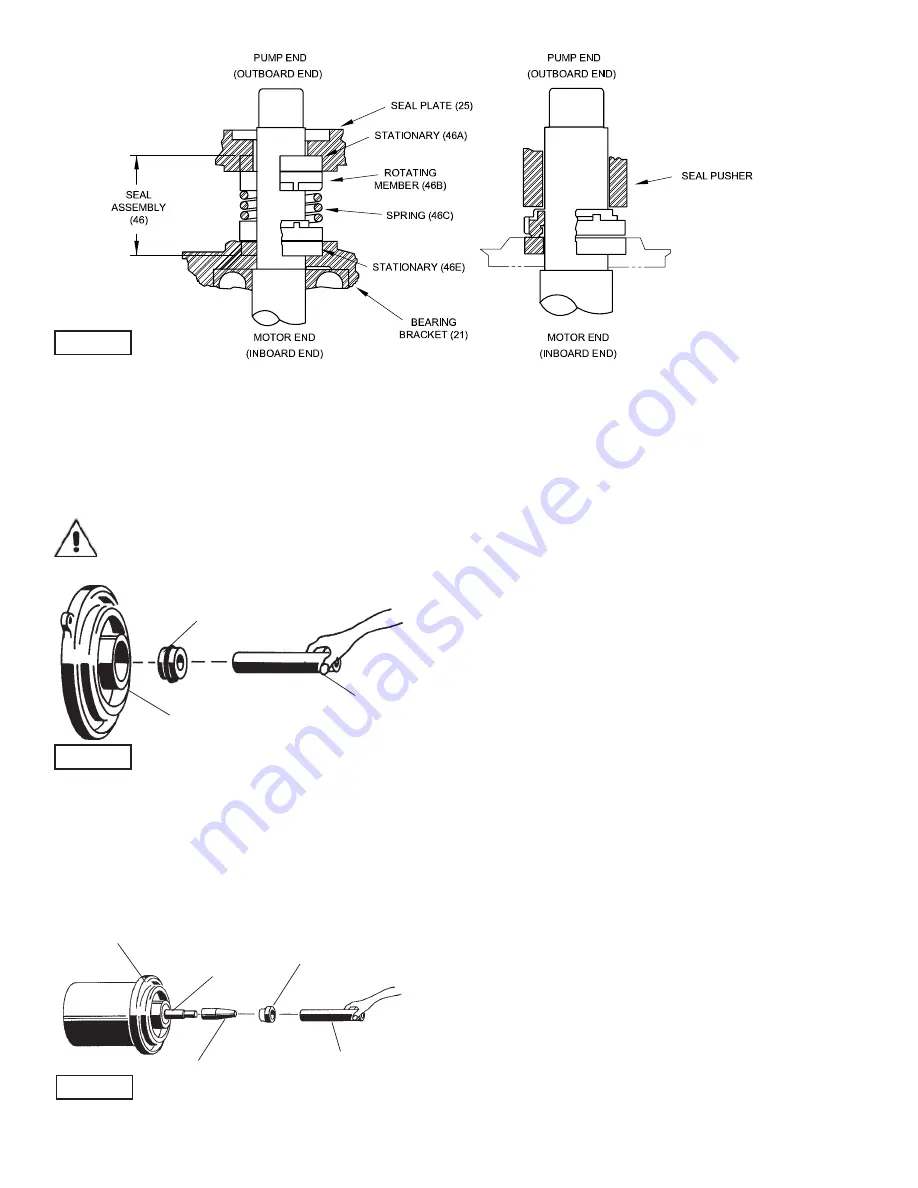
10
Seal -
Clean and oil seal cavities in bearing bracket (21)
and seal plate (25). Lightly oil
(DO NOT use grease)
outer
surface of inboard stationary member (46E) and outboard
stationary member (46A). Press inboard stationary member
(46E) fi rmly into bearing bracket (21) and outboard stationary
(46A) into seal plate (25), using a seal pusher (see parts list-
seal tool kit), nothing but the seal pusher is to come in contact
with seal face (See Figures 2 & 3).
Important ! - DO NOT hammer on the seal pusher-
it will damage the seal face.
Make sure the stationary members are in straight and that
the rubber ring is not out of it’s groove. Lightly oil
(DO NOT
use grease)
shaft and inner surface of bellows on rotating
member (46D) See Figure 4. With lapped surface facing
bearing bracket (21), slide rotating member (46D) onto shaft,
using seal pusher, until lapped faces of (46D) and (46E) are
together (See Figure 2). It is extremely important to keep seal
faces clean during assembly. Dirt particles lodged between
these faces will cause the seal to leak.
Make sure driving lugs in retainer are matched in rotating
member. Place spring (46C) over shaft and in place on rotat-
ing member (4E), making sure it is seated in retainer and not
cocked or resting on bellows tail. Re-oil shaft and lightly oil
inner surface of outboard rotating member (46B). With tail
section toward bearing bracket (21), slide rotating member
(46B) onto shaft with seal pusher until retainer engages spring
(46C) and spring is compressed slightly. Make sure spring
(46C) is properly engaged in both retainers. Insert o-ring (42)
onto bearing braket (21). Slide seal plate (25) over shaft onto
bearing bracket (21), being careful not to damage outboard
stationary member (46A) and align holes for socket head cap
screws (39). Thread socket head cap screws (39) into bearing
bracket (21) and tighten. Fill seal chamber with oil as outlined
in paragraph F-1.3. Reassemble impeller and volute per para-
graph F-2.2.
F-4.3) Wiring Connections:
Check power cable (10A) and control cable (10D), on conduit
box (10), for cracks or damage and replace complete conduit
box assembly (10) if required (See Fig. 5). Bring motor wires
through wire opening in top of housing (2),check sleeving (53)
and replace if required, position square ring (11) in conduit
housing (10) and reconnect motor leads to power cable and
moisture and temperature sensor leads to control cable using
connectors (12), (17) and insulators (54) as show in Figure 6.
F-4.4) Conduit Box and Cable Assembly:
Refi ll with cooling oil as outlined in paragraph F-1.3. Position
conduit box (10) and square ring (11) over opening, apply
thread locking compound to cap screws (6) threads and torque
to 16 ft. lb. Remove gland nuts (10B) and (10F), friction rings
(10C) and (10G), and grommets (10D) and (10H) from conduit
box (10) inspect and replace if required (See Figure 5). Insert
one friction ring (10C), grommet (10D), one friction ring (10C)
and gland nut (10B) into conduit box for power cable (10A). For
control cable (10E), insert grommet (10H), friction ring (10G)
and gland nut (10F). Torque gland nuts (10B) and (10F) to 15
ft. lb. to prevent water leakage.
F-5) Base & Elbow Service:
To clean out base elbow (68) remove cap screws, clean-out
plates (64) and o-ring (67) from elbow (68). Inspect o-ring
and replace if damaged. If gasket (58) is damaged or leaking,
remove hex nuts (61) and lockwashers (60) and remove hard-
ware from piping to drop elbow down. To remove pump from
base (59) remove hex nuts (70) and lockwashers (66) and lift
pump from base.
FIGURE 2
FIGURE 4
Stationary Member (46E)
Polished Face Out
Seal Plate (25)
Seal Pusher
FIGURE 3
Rotating Member (46D)
Bullet
Motor & Bearing Bracket
Seal Pusher
Stationary
Summary of Contents for 6DSE-L Series
Page 5: ...5 inches mm...
Page 14: ...14 FIGURE 7 6DSE L Pump Series...
Page 15: ...15 FIGURE 8 6DSE L Pump Series...
Page 22: ...Notes...