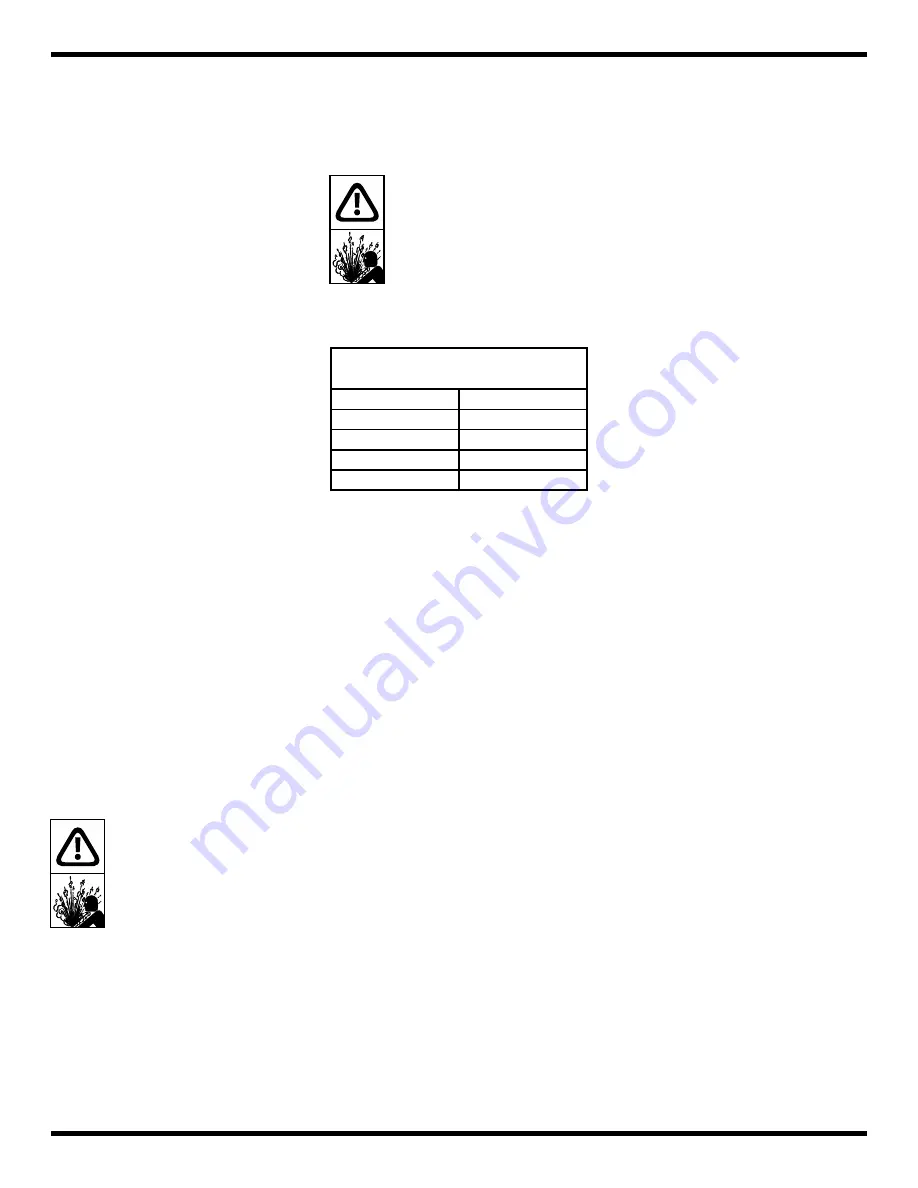
5
Oil Replacement
- Set unit upright
and refill with new cooling oil as per
table below. Fill to just above motor,
but below capacitor as an air space
must remain in the top of the
housing to compensate for oil
expansion.
Cooling Oil
Recommended Supplier/Grade
BP
Enerpar SE100
Conoco
Pale Parafin 22
Mobile
D.T.E. Oil Light
Shell Canada
Transformer-10
Texaco
Diala-Oil-AX
4
Disassembly
Impeller and Volute:
1. Disconnect power.
Service
Pressure builds up extremely
fast, increase pressure by
"TAPPING" air nozzle. Too
much pressure will damage
seal.
DO NOT exceed 10 PSI.
DO
NOT
overfill
oil.
Overfilling of housing with oil
can create excessive and
dangerous hydraulic pressure
which can destroy the pump
and create a hazard.
Overfilling oil voids warranty.
2. Remove cap screws, volute and
gasket.
12. Remove seal’s rotating member,
spring and retaining ring from seal
plate. Examine all seal parts, if seal
faces show signs of wear, uneven
wear pattern, chips or scratches
replace
entire
seal.
DO
NOT
interchange
seal
components,
replace the entire shaft seal
. If
replacing seal, remove stationary by
prying out with flat screwdrive.
Shaft Seal:
11. Remove snap ring from seal plate.
Remove shaft and motor rotor from
seal plate.
Oil Testing
Ÿ
Drain oil into a clean, dry
container by placing pump on
it’s side, remove pipe plug, from
housing.
Ÿ
Check oil for contamination
using an oil tester with a range
to 30 kilovolts breakdown.
Ÿ
If oil is found to be clean and
uncontaminated
(measuring
above 15 kV breakdown), refill
the housing.
Ÿ
If oil is found to be dirty or
contaminated
(or
measures
below 15 kV breakdown), the
pump
must
be
carefully
inspected for leaks at the shaft
seal, cable assembly, square ring
and pipe plug, before refilling
with oil. To locate the leak,
perform a pressure test.
After leak is repaired, dispose of old
oil properly, and refill with new oil.
3. Clean and examine impeller, for
cracks or breakage and replace if
required. To remove impeller, place a
flat screwdriver in the slot of the end
of the shaft to hold the shaft
stationary while unscrewing.
4. Check v-ring and remove if
damaged.
Power Cord and Motor:
5. Remove pipe plug and drain oil
from housing.
6. Remove gland nut, washer and
nylon housing from motor housing.
Pull cord through and disconnect the
wires from the terminals on power
cord.
7. Remove screws and washers and
lift motor housing and stator from
seal plate.
8. Remove o-ring, replace if damaged.
9. Check motor capacitor with an
Ohm meter by first grounding the
capacitor by placing a screwdriver
across both terminals and then
removing screwdriver. Connect Ohm
meter (set on high scale) to terminals.
If needle moves to infinity (∞) then
drifts back, the capacitor is good. If
needle does not move or moves to
infinity (∞) and does not drift back,
replace capacitor.
10. Inspect motor winding for shorts
and check resistance values. Check
rotor for wear. If rotor or the stator
windings are defective, the complete
motor must be replaced.
Bearings:
13. Examine lower bearing, and
upper bearing, if replacement is
required, remove by using a wheel
puller.
With a flashlight, visually inspect the
oil in the housing to make sure it is
clean and clear, light amber in color
and free from suspended particles.
Milky white oil indicates the presence
of water. Oil level should be just
above the motor when pump is in
vertical position.
Apply pipe thread compound to
threads of pipe plug then assemble
to housing.
barmesa.com
Summary of Contents for BPEV512 Series
Page 11: ...10 barmesa com...