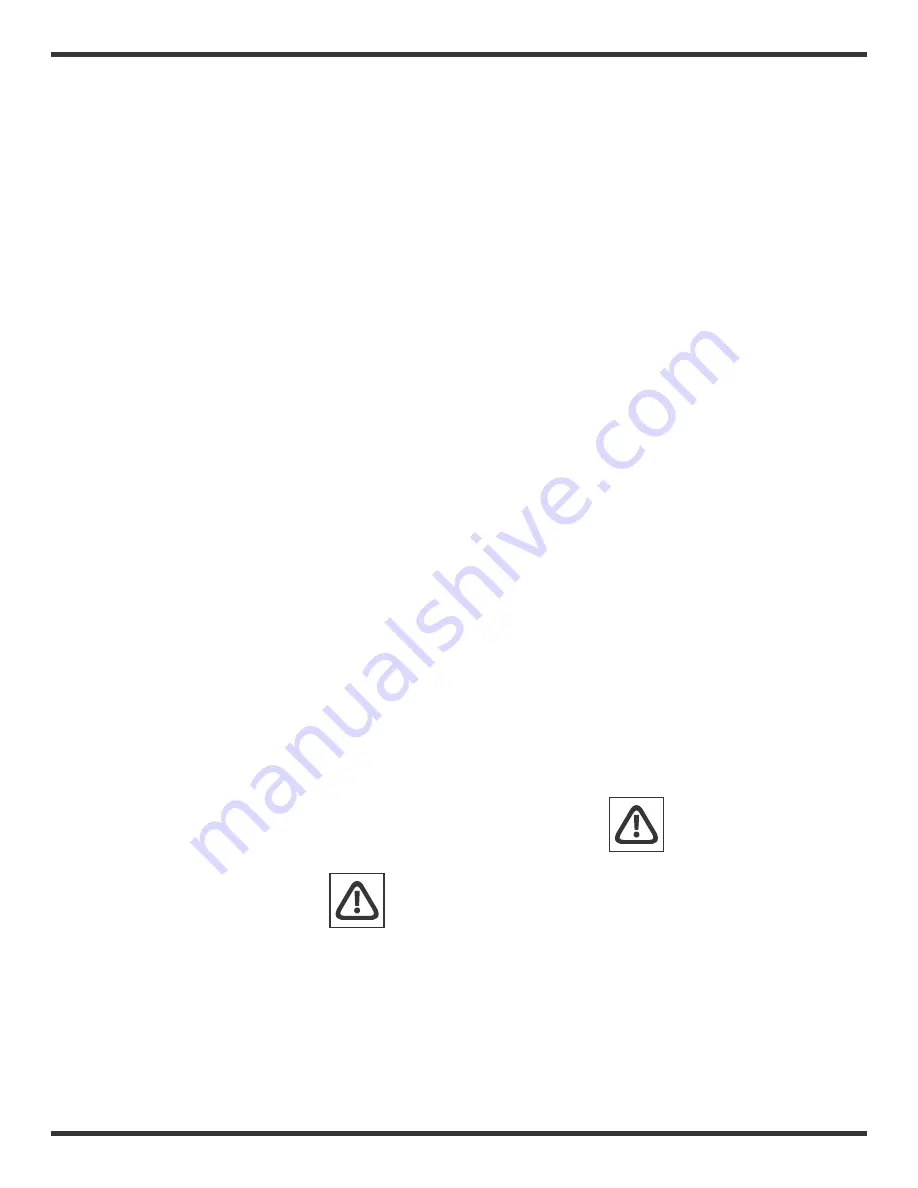
7
4
Disassembly
Impeller and Volute -
Disconnect
power. Remove hex nuts ( ) and
16
vertically lift motor housing and seal
plate assembly from volute (3 ).
7
Clean out volute (3 ) if necessary.
7
Inspect gasket (3 ) and replace if cut
6
or damaged. Clean and examine
impeller ( ), for pitting or wear and
32
replace if required. To remove
impeller ( ), remove cap screw ( )
32
35
a
34
nd washer ( ). With a wheel puller,
pull impeller straight of
shaft and
remove
. To remove wear
square key
ring (33), split it and remove, being
carefull not to damage volute.
Moisture Probes -
Drain oil from seal
chamber, if not already done.
Remove cap screws (9) and lifting
handle (8). Set unit upside down on
blocks to avoid damaging cables.
Remove socket head cap screws (27)
and lift seal plate (26), with seal’s (19)
stationary, vertically from bearing
housing (15),
do not
damage seal.
Check moisture sensor probes (41)
for damage, replace by removing
screws (42) and disconnecting wires
(40). Then remove probes (41) from
bearing housing (15).
Diaphragm -
6
with seal plate (2 )
removed, examine diaphragm (2 )
3
for ruptures or crackes. Replace
diaphragm by removing capscrews
( ) and plate ( ). Clean vent holes
25
24
in seal plate (2 ).
6
Shaft Seal -
Remove outboard
rotating member of seal (19), spring
and inboard rotating member from
shaft. Examine all seal parts.
Inspect seal for signs of uneven wear
pattern on stationary members, chips
and scratches on either seal face.
DO
NOT interchange seal components,
replace the entire shaft seal (19)
. If
replacing seal, remove stationary by
prying out with flat screwdriver.
Motor and Bearings -
Remove
volute, impeller, seal plate and seal as
previously stated and drain oil from
motor housing (3). Position unit
upright, using blocks to avoid resting
unit on shaft. Remove cap screws (6)
o-ring (5) and conduit box assembly
(4) from motor housing (3). Note
connections and then remove cable
lead wires from motor lead wires and
moisture
temperature sensor
and
wires from control cable by removing
connectors. Remove cap screws (12)
and vertically lift the motor housing
(3) from bearing housing (1 ).
5
Replace square ring (1 if damaged
4)
or cut. Remove the upper motor bolts
and lift upper end bell from motor
(1). Remove wave washer. Remove
upper bearing (2) with a wheel puller
if damaged or worn.
Vertically lift stator (1) from
rotor/shaft. Inspect windings for
shorts and resistance. Test the
temperature sensors by checking for
continuity between the black and
white wires. If defective contact
f
actory or motor service station. Pull
motor rotor/shaft with bearing (1 )
3
from bearing housing (1 ). Remove
5
bearing (1 ) with a wheel puller if
3
worn or damaged. If rotor or stator
windings are defective, replace the
complete motor.
4
Reassembly
Bearings -
Replace bearings, being
careful not to damage the rotor or
shaft. If equipped, i
fill notch should
face the rotor core for both upper
and lower bearings.
Apply adhesive compound to the
shaft and press bearing (1 ) onto
3
shaft, position squarely onto the
shaft applying force to the inner race
of bearing only, until bearing seats on
shoulder of the shaft. In the same
manner, assemble upper bearing (2)
to shaft.
Motor -
Slide rotor with bearing (13)
into bearing housing
5
(1 ) until
bearing seats on the bottom. Position
motor housing and stator into pilot,
install wav
upper end
e washers in
bell.
IMPORTANT! Special wave washers
in upper motor housing are required
to compensate for shaft expansion.
These washers must be properly
reinstalled to give the required
constant down force on the motor
shaft.
Position upper motor end bell
aligning holes and thread cap screws
into bearing housing (1 ) and torque
5
to 16 ft/lbs. Place all motor leads
above the motor. Position square ring
(1 ) on bearing housing (1 ) and
4
5
lower housing (3) over motor and
into pilot, aligning handle so that it is
parallel to motor end bell reliefs.
Apply thread locking compound to
threads on cap screws (12) and install
with nuts (16) and torque to 24 ft/lbs.
Seal/Diaphragm -
(See Figure 3)
Clean and oil seal cavities in bearing
housing (1 ) and seal late (2 ).
5
p
6
Lightly oil
outer
(Do not use grease)
surface of inboard and outboard
stationary members of seal (19). Press
inboard stationary member if rmly
into bearing housing (15) and
outboard stationary into seal plate
( ), using a seal pusher tool.
24
Nothing but the seal pusher tool is to
come in contact with seal face.
IMPORTANT! - All parts
must be clean before
reassembly.
Handle seal parts with
extreme care. DO NOT
damage lapped surfaces.
Service
barmesa.com
Summary of Contents for 6BSE-LDS Series
Page 18: ...17 barmesa com...