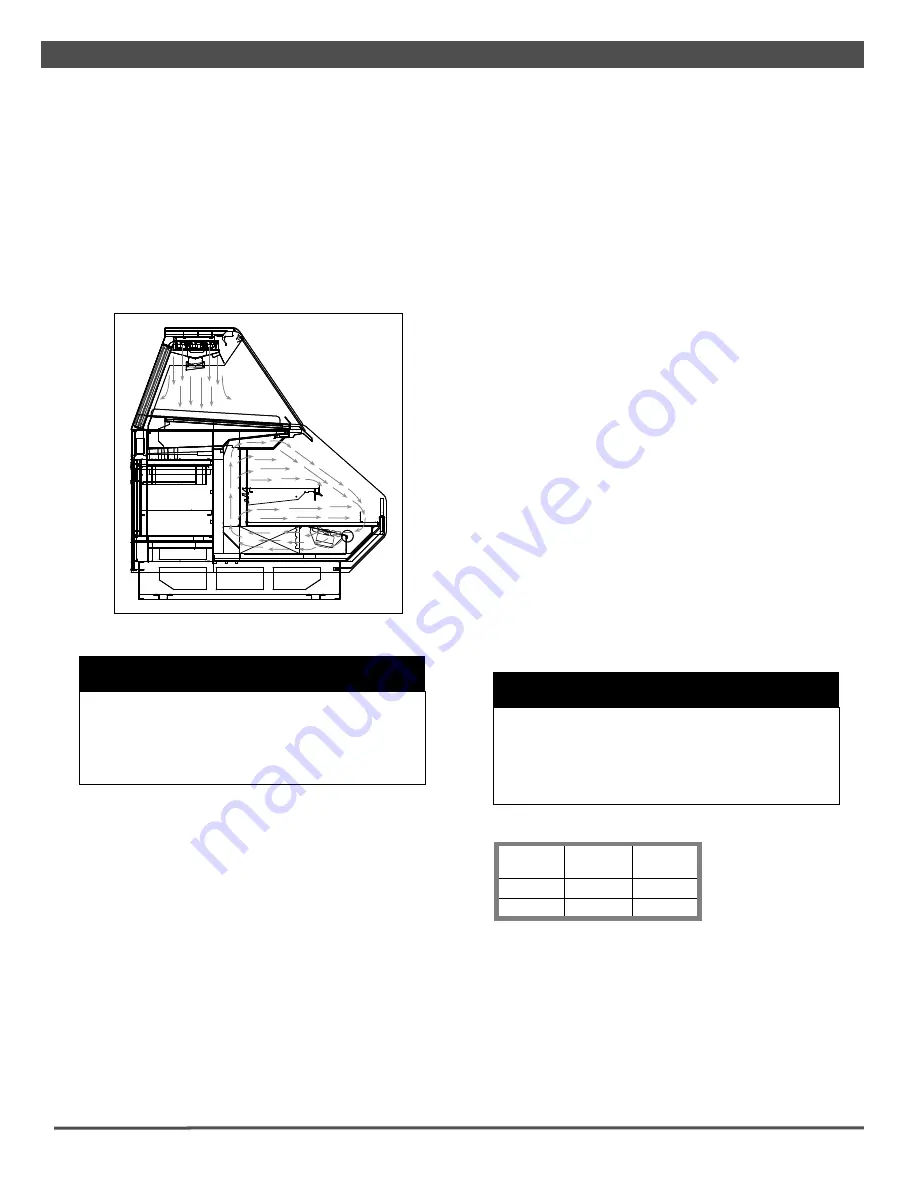
AIRFLOW & DEFROST
Cut-In/Cut-Out
Cut-In
Temp (
o
F)
Cut-Out
Temp (
o
F)
Pans
33
29
Top Coil
36
31
AIRFLOW & PRODUCT LOAD
Hillphoenix cases provide maximum product capacity within the
refrigerated air envelope. Please keep products within the ap-
propriate load limit.
It is important that you do not overload the food product display
so that it
impinges on the airfl ow pattern (Fig. 11). Overload-
ing will cause malfunction and the loss of proper temperature
levels, particularly when discharge and return air sections are
covered.
W A R N I N G
Always keep product within the designated air
curtain. Failure to do so may result in case
malfunction and product losing proper tempera-
ture, resulting in sub-standard operation and
increased chances of food contamination.
▲
PTD-RGC cases are available with the defrost and temperature
controls mounted at the case or initiated by the rack controller.
When the controls are mounted at the case, the single time-off
defrost is initiated by the Dixell XR70CX controller mounted in
the slide out control box. During defrost, all valves close and
the pump cycles OFF. When in refrigeration mode, the glycol
fl ow to the top coil, shelves and the Coolgenix pans is inde-
pendently controlled by the Dixell controller. If none of these
components requires fl ow, all solenoids close (including DX
liquid-line valve) and the pump is cycled OFF.
When defrost and temperature are controlled from the rack,
the time-off defrost is controlled by a set of normally open con-
tacts at the rack controller. When in refrigeration mode, the
top coils, shelf and the Coolgenix pans are controlled as three
independent, temperature-controlled cases. Again, if none of
C A U T I O N
If the shelves are removed from the case or other-
wise not utilized, the shelf setpoint (SAA) must be
raised to 90
o
F to prevent the pump from running
when only the shelves are calling for refrigeration.
Failure to do so could result in early pump failure.
▲
these components requires fl ow, all valves close and the pump
cycles OFF.
Whether the controls are managed at the case or by the rack
controller, the case and product temperatures are maintained
by having the top coils, shelves and the Coolgenix deck pans
cycle through their individual DIFFERENTIAL range. If the
Dixell XR70CX Controller is used, the fl ow of the chilled fl uid to
the Coolgenix pans, shelves and top coil circuit is controlled by
comparing the temperature readings of the appropriate tem-
perature sensor against either the CUT-IN or CUT-OUT setpoint
to the DIFFERENTIAL control settings. To determine CUT-OUT
temperature, calculate the CUT-IN minus the DIFFERENTIAL.
To determine CUT-IN temperature, calculate the CUT-OUT plus
the DIFFERENTIAL. For example, the factory setting for pan
CUT-OUT is 29°F with a 4°F DIFFERENTIAL which yields a CUT-
IN setting of 33°F.
The factory settings should be considered a guide and may
need to be adjusted based on store conditions. Because
these cases are often installed in stores near a meat prepara-
tion area where standard ASHRAE conditions may not apply,
different settings may be required for optimal operation.
It is important to consult the guidelines and control setting
shown on page 2 before setting defrost times. Further adjust-
ment may be required depending on store conditions.
If your case is equipped with a Dixell temperature and humidity
controller, see Appendices B1-B4 for operating instructions.
If you need to convert pressure to temperature see Appendix
C1 for the Sporlan Temperature-Pressure Chart.
DEFROST & TEMPERATURE CONTROLS
Cases are equipped with either Hot Gas or Timed-Off defrost at
the owner's option.
The hot gas defrost termination sensor bulb and probe are
attached to the dump line which is in the front, left-hand side
of the case.
Fig. 11 Airflow pattern
16
Summary of Contents for PTD-RGC
Page 2: ...ii ...