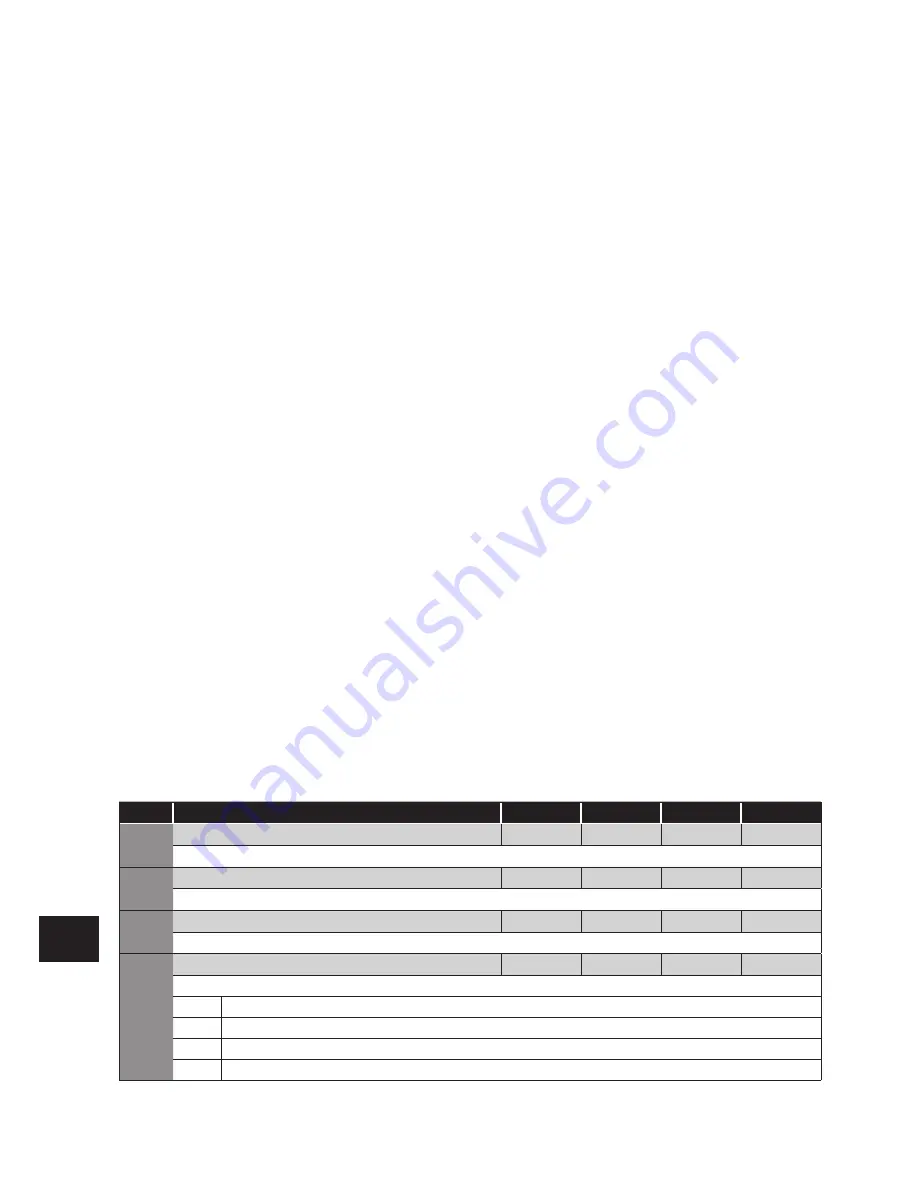
P2 Series User Guide |
Version 3.01
www.bardac.com
8.3.1. Overview
The P2 provides many methods to allow the user to connect to a variety of fieldbus networks. In addition, connection to options such
as external keypads, drive.web programmable conrollers, PC and Optistick are possible. Parameter Group 5 provides the parameters
required to configure the various fieldbus interfaces and connection points.
8.3.2. Connecting Bardac
drive.web
Options
All Bardac
drive.web
options which require communication with the drive, connect to the P2 using the built in RJ45 connection point.
The pin connections on these options are already matched, such that a simple pin to pin plug in cable can be used to connect these
options without any special requirements.
For further information on connecting and using these optional items, refer to the specific option User guide.
8.3.3. Connecting to a PC or Mac via Ethernet or USB
A low cost, plug-in
drive.web speedy
interface controller can be used to connect a drive or drive system to a PC running the
savvy
tools on currently supported versions of either Microsoft Windows or Mac OSX operating systems with Java. The
savvy
tools can be used to configure connect and control a drive or complete drive control system.
Get savvy
Download – get the free basic
savvy
tools from https://driveweb.com/get-savvy/ for easy programming & networking via a
speedy (model dw224) interface to your computer USB or Ethernet port.
• Import/export configurations – edit programs – monitor – control – create trend charts – export operational data to a .csv file
• create
savvyPanel
operator stations for touch screens for PCs, Macs, iPad, iPhone
• network drives peer to peer over Ethernet – build complete integrated drive systems without using a PLC or SCADA
• Add smarty automation controllers for full featured featured programmable control and remote i/o
• Upgrade savvy to the savvy-SFD, Signal Flow Diagram version for easy systems design with drag and drop connections
• Add smart function blocks for advanced control, winders, encoder position, motion, indexing, registration, solar tracking & more
Get Training
Get free online training for drive configuration and drive system design – contact [email protected]
8.3.4. Modbus RTU Connection
The P2 supports Modbus RTU communication. Connection is made through the RJ45 connector. For further information refer to section
9.2. Modbus RTU Communications on page 61.
8.3.5. CAN Open Connection
The P2 supports CAN Open communication. Connection is made through the RJ45 connector. For further information refer to section
9.3. CAN Open Communication on page 63.
8.3.6. Other Fieldbus Networks
Additional fieldbus network protocols are supported using optional interfaces. Call Bardac (USA 410-604-3400) or refer to the
Bardac.com website for a list of supported protocols and the required interface option modules.
8.3.7. Communication Parameters
Par
Name
Minimum
Maximum
Default
Units
P5-01
Drive Fieldbus Address
0
63
1
-
Sets the Fieldbus address for the drive.
P5-02 CAN Baud Rate
125
1000
500
kbps
Sets the baud rate when CAN Open communications are used.
P5-03 Modbus RTU Baud rate
9.6
115.2
115.2
kbps
Sets the baud rate when Modbus RTU communications are used.
P5-04 Modbus RTU
-
-
-
-
Sets the expected Modbus telegram data format as follows:
No Parity, 1 stop bit
No parity, 2 stop bits
Odd parity, 1 stop bit
Even parity, 1 stop bit
8
Extended P
arameters