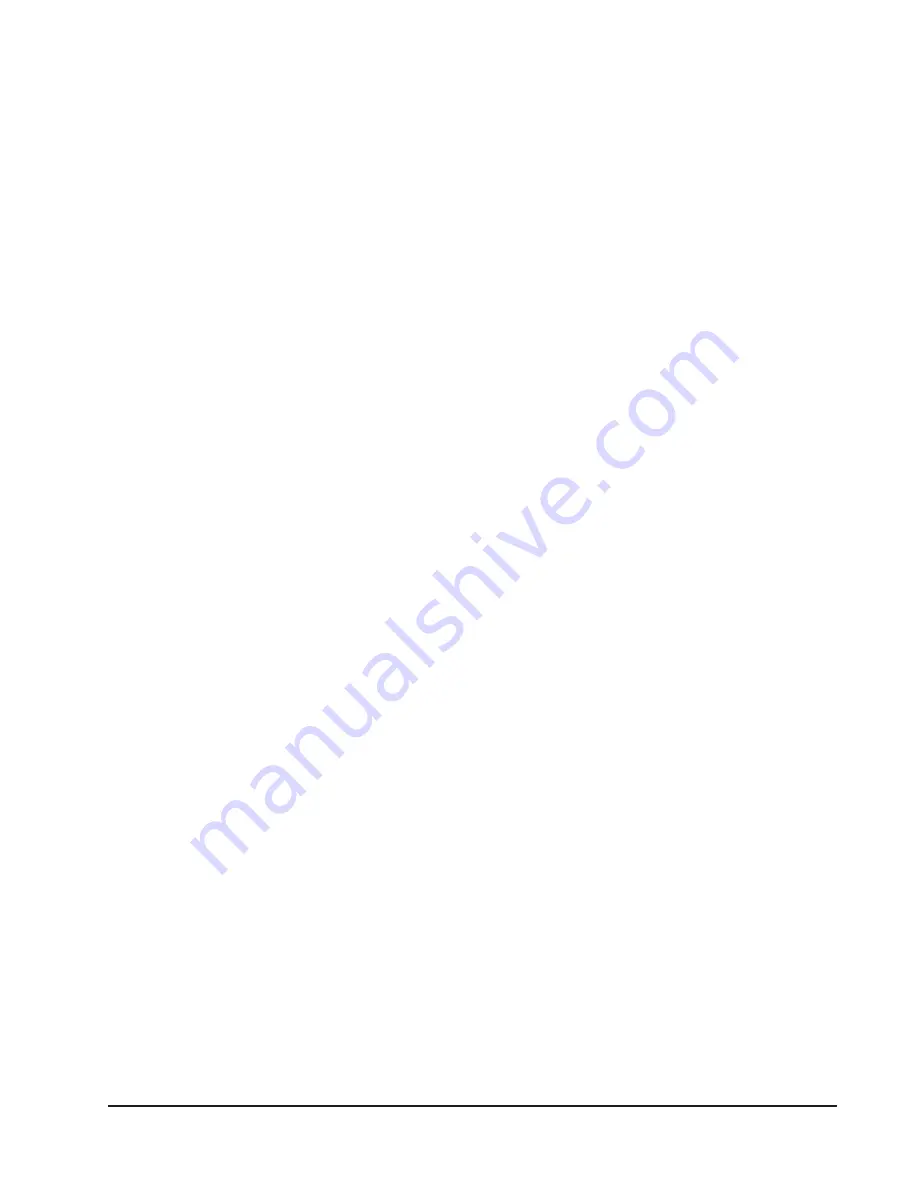
Manual 2100-692E
Page
25 of 42
statics)
. Consult Bard Application Engineering for
details prior to implementation.
CAUTION:
Balanced Climate is not a replacement for
a dehumidification (hot gas reheat) unit for extreme
applications, but rather an enhancement feature for
limited climates and applications.
Vent Connection Plug
All units are equipped with a vent connection plug in
the side of the control panel for the different ventilation
packages to plug in to. If the compressor will not start
and there is no "Y1" at the compressor control module,
first check to make sure that either the optional vent is
plugged into the vent connection plug or the supplied
jumper plug is in place.
The unit will not operate
without anything plugged in.
This plug is located on
the side of the control panel behind the front vent door
(behind the filter access door). If the unit is supplied
with a factory-installed vent package, it will be plugged
in but the jumper plug will also be tethered next to the
connection for troubleshooting purposes, if necessary.
Compressor Control Module
The compressor control module (CCM) is standard on
all models covered by this manual.
Features
Delay-on-Make Timer
Short Cycle Protection/Delay-on-Break
Low Pressure Detection
High Pressure Detection
LPC and HPC Status LEDs
Test Mode
Brownout Protection with Adjustment
Delay-on-Make Timer
A delay-on-make timer is included to be able to delay
startup of the compressor. This is desired when more
than one unit is on a structure so that all of the units
do not start at the same time which could happen
after a power loss or building shutdown. The delay-
on-make time period is 2 minutes plus 10% of the
delay-on-break time period. To ensure that all of the
units do not start at the same time, adjust the delay-
on-break timer on each unit to a slightly different
delay time.
Short Cycle Protection/Delay-on-Break
An anti-short cycle timer is included to prevent short
cycling the compressor. This is adjustable from 30
seconds to 5 minutes via the adjustment knob (see
Figure 22 on page 26). Once a compressor call is
lost, the time period must expire before a new call
will be initiated.
Low Pressure Detection
Low pressure switch monitoring allows for a lockout
condition in a situation where the switch is open. If
the low pressure switch remains open for more than
2 minutes. the CCM will de-energize the compressor
for the delay-on-break time. If the switch closes again,
it will then restart the compressor. If the switch trips
again during the same Y call, the compressor will be
de-energized and the alarm terminal will be energized
indicating an alarm. The blue LED will light and stay on
until power is cycled to the control or a loss of voltage is
present at Y terminal for more than ½ second.
High Pressure Detection
High pressure switch monitoring allows for a lockout
condition in a situation where the switch is open. If
the high pressure switch opens, the CCM will de-
energize the compressor. If the switch closes again,
it will then restart the compressor after the delay-
on-break setting has expired on the device. If the
switch trips again during the same thermostat call,
the compressor will be de-energized and the alarm
terminal will be energized indicating an alarm. The
red LED will light and stay on until power is cycled
to the control or a loss of voltage is present at Y
terminal for more than ½ second.
Test Mode
By rapidly rotating the potentiometer (POT) clockwise
(see Figure 22 on page 26), all timing functions will
be removed for testing.
The conditions needed for the unit to enter test mode
are as follows: POT must start at a time less than or
equal to the 40 second mark. The POT must then be
rapidly rotated to a position greater than or equal to
the 280 second mark in less than ¼ second. Normal
operation will resume after power is reset or after the
unit has been in test mode for at least 5 minutes.
Brownout Protection with Adjustment
Brownout protection may be necessary if the utility
power or generator power has inadequate power to
prevent the voltage from dropping when the compressor
starts. This is rare but can happen if the generator
is undersized at the site or if the site is in a remote
location far from the main power grid. Under normal
circumstances, allowing the brownout to be ignored for
a time period should not be needed. The 8201-169 is
shipped with all the DIP switches in the 'off' or 'do not
ignore' position (see Figure 22 on page 26).
If ignoring the brownout is needed because of the
above conditions, three preset timers can be set by DIP
switches in order to delay signaling a power brownout
for a specific length of time after compressor contactor
is energized. This allows the compressor a time period
to start even if the voltage has dropped and allows
the voltage to recover. This delay only happens when
the CC terminal energizes. The delay can be set to 1
second (A DIP switch), 5 seconds (B DIP switch) or 10
seconds (C DIP switch); time is not cumulative—only
the longest setting will apply. If the voltage recovers