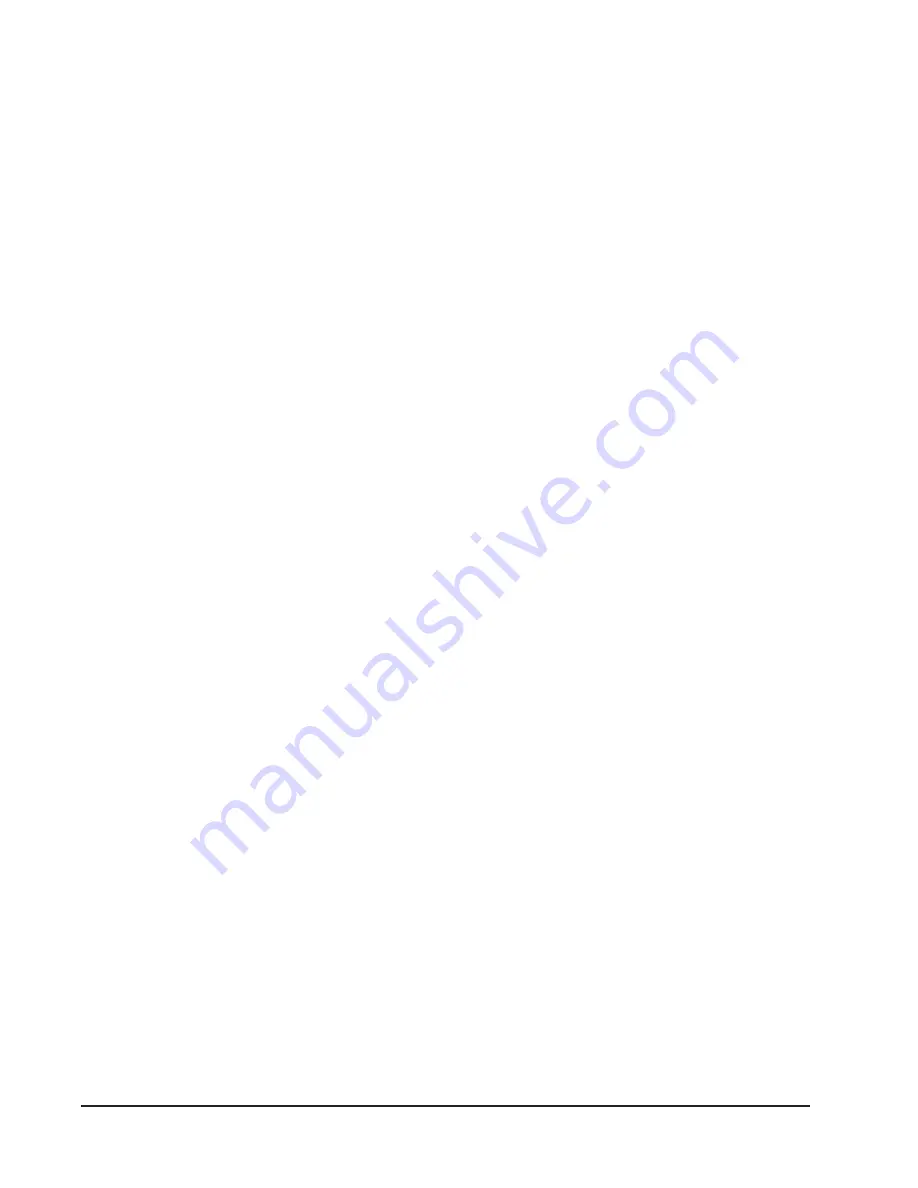
Manual 2100-511
Page
14 of 27
WIRING – MAIN POWER
Refer to the unit rating plate for wire sizing information
and maximum fuse or “HACR” type circuit breaker
size. Each outdoor unit is marked with a “Minimum
Circuit Ampacity”. This means that the field wiring
used must be sized to carry that amount of current.
Depending on the installed KW of electric heat, there
may be two field power circuits required. If this is the
case, the unit serial plate will so indicate. All models
are suitable only for connection with copper wire. Each
unit and/or wiring diagram will be marked “Use Copper
Conductors Only”. These instructions
must be
adhered
to. Refer to the National Electrical Code (NEC) for
complete current carrying capacity data on the various
insulation grades of wiring material. All wiring must
conform to NEC and all local codes.
The electrical data lists fuse and wire sizes (75° C
copper) for all models including the most commonly
used heater sizes. Also shown are the number of field
power circuits required for the various models with
heaters.
The unit rating plate lists a “Maximum Time Delay
Relay Fuse” or “HACR” type circuit breaker that is to
be used with the equipment. The correct size must be
used for proper circuit protection and also to assure that
there will be no nuisance tripping due to the momentary
high starting current of the compressor motor.
The disconnect access door on this unit may be locked
to prevent unauthorized access to the disconnect. To
convert for the locking capability, bend the tab located
in the bottom left-hand corner of the disconnect opening
under the disconnect access panel straight out. This tab
will now line up with the slot in the door. When shut, a
padlock may be placed through the hole in the tab
preventing entry.
See “Start Up” section for important information on
three phase scroll compressor start ups.
See Table 5 for Electrical Specifications.
WIRING – LOW VOLTAGE WIRING
230/208V, 1 phase and 3 phase equipment dual primary
voltage transformers. All equipment leaves the factory
wired on 240V tap. For 208V operation, reconnect from
240V to 208V tap. The acceptable operating voltage
range for the 240 and 208V taps are:
TAP
RANGE
240
253 – 216
208
220 – 187
NOTE: The voltage should be measured at the field power
connection point in the unit and while the unit is
operating at full load (maximum amperage
operating condition).
For wiring size and connections, refer to Wiring Manual
2100-507.
Summary of Contents for W18H1
Page 8: ...Manual 2100 511 Page 8 of 27 FIGURE 3A W18H1 W24H1 MOUNTING INSTRUCTIONS...
Page 9: ...Manual 2100 511 Page 9 of 27 FIGURE 3B W30H1 W36H1 MOUNTING INSTRUCTIONS...
Page 10: ...Manual 2100 511 Page 10 of 27 FIGURE 3C W42H1 W48H1 W60H1 MOUNTING INSTRUCTIONS...
Page 13: ...Manual 2100 511 Page 13 of 27 FIGURE 7 COMMON WALL MOUNTING INSTALLATIONS...
Page 18: ...Manual 2100 511 Page 18 of 27 FIGURE 8 DEFROST CONTROL BOARD...