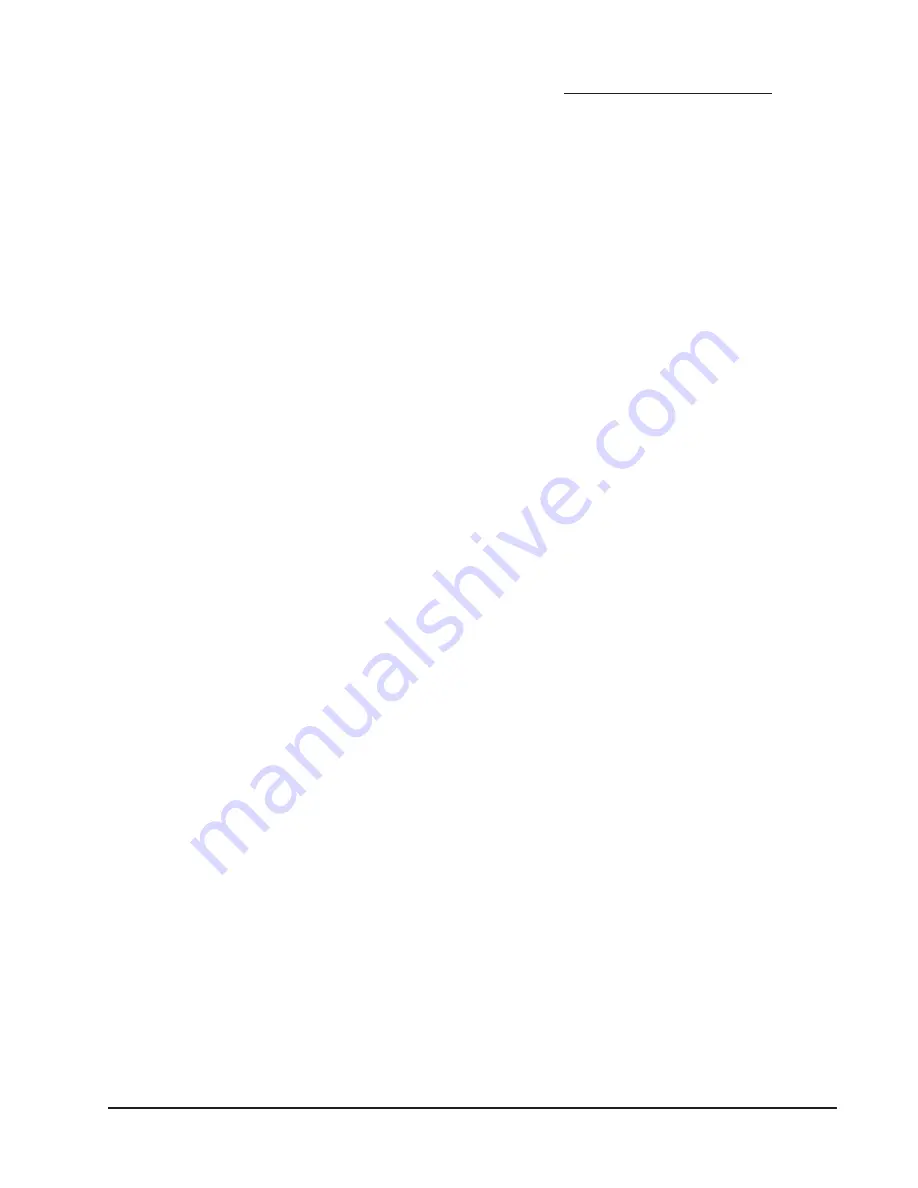
Manual 2100-718A
Page
15 of 26
SEQUENCE OF OPERATION
Cooling Stage 1
Circuit R-Y makes at thermostat pulling in compressor
contactor, starting the compressor and outdoor motor.
The G (indoor motor) circuit is automatically completed
on any call for cooling operation or can be energized
by manual fan switch on subbase for constant air
circulation.
Cooling Stage
2
Circuit R-Y1 makes at the thermostat energizing the
2nd stage solenoid in the compressor. Default position
is not energized. Compressor will run at low capacity
until this solenoid is energized.
Heating
Stage 1
A 24V solenoid coil on reversing valve controls heating
cycle operation. Two thermostat options, one allowing
“Auto” changeover from cycle to cycle and the other
constantly energizing solenoid coil during heating season
and thus eliminating pressure equalization noise except
during defrost, are to be used. On “Auto” option a
circuit is completed from R-B and R-Y on each heating
“on” cycle, energizing reversing valve solenoid and
pulling in compressor contactor starting compressor and
outdoor motor. R-G also make starting indoor blower
motor. Heat pump heating cycle now in operation. The
second option has no “Auto” changeover position, but
instead energizes the reversing valve solenoid constantly
whenever the system switch on subbase is placed in
“Heat” position, the “B” terminal being constantly
energized from R. A thermostat demand for Stage
1 heat completes R-Y circuit, pulling in compressor
contactor starting compressor and outdoor motor. R-G
also make starting indoor blower motor.
Heating
Stage
2
Circuit R-Y2 makes at the thermostat energizing the
2nd stage solenoid in the compressor.
PRESSURE SERVICE PORTS
High and low pressure service ports are installed on
all units so that the system operating pressures can
be observed. Pressure Tables 5A and 5B covering all
models can be found on page 21. It is imperative to
match the correct pressure table to the unit by model
number.
This unit employs high-flow Coremax valves instead of
the typical Shrader type valves.
WARNING! Do NOT use a Schrader valve core removal
tool with these valves. Use of such a tool could result in
eye injuries or refrigerant burns!
To change a Coremax valve without first removing the
refrigerant, a special tool is required which can be
obtained at www.fastestinc.com/en/SCCA07H. See the
replacement parts manual for replacement core part
numbers.
DEFROST CYCLE
The defrost cycle is controlled by temperature and time
on the solid state heat pump control.
When the outdoor temperature is in the lower
40°F temperature range or colder, the outdoor coil
temperature is 32°F or below. This coil temperature
is sensed by the coil temperature sensor mounted near
the bottom of the outdoor coil. Once coil temperature
reaches 30°F or below, the coil temperature sensor
sends a signal to the control logic of the heat pump
control and the defrost timer will start accumulating
run time.
After 30, 60 or 90 minutes of heat pump operation at
30°F or below, the heat pump control will place the
system in the defrost mode.
During the defrost mode, the refrigerant cycle switches
back to the cooling cycle, the outdoor motor stops,
electric heaters are energized and hot gas passing
through the outdoor coil melts any accumulated frost.
When the temperature rises to approximately 57°F, the
coil temperature sensor will send a signal to the heat
pump control which will return the system to heating
operations automatically.
If some abnormal or temporary condition such as a high
wind causes the heat pump to have a prolonged defrost
cycle, the heat pump control will restore the system to
heating operation automatically after 8 minutes.
The heat pump defrost control board has an option of
30, 60 or 90-minute setting. By default, this unit is
shipped from the factory with the defrost time on the
60-minute pin. If circumstances require a change
to another time, remove the wire from the 60-minute
terminal and reconnect to the desired terminal. Refer
to Figure 8.
There is a cycle speed up jumper on the control. This
can be used for testing purposes to reduce the time
between defrost cycle operation without waiting for
time to elapse.
Use a small screwdriver or other metallic object, or
another ¼" QC, to short between the
SPEEDUP
terminals
to accelerate the HPC timer and initiate defrost.
Be careful not to touch any other terminals with the
instrument used to short the
SPEEDUP
terminals.
It may take up to 10 seconds with the
SPEEDUP
terminals shorted for the speedup to be completed and
the defrost cycle to start.
As soon as the defrost cycle kicks in, remove the
shorting instrument from the SPEEDUP terminals.
Otherwise the timing will remain accelerated and