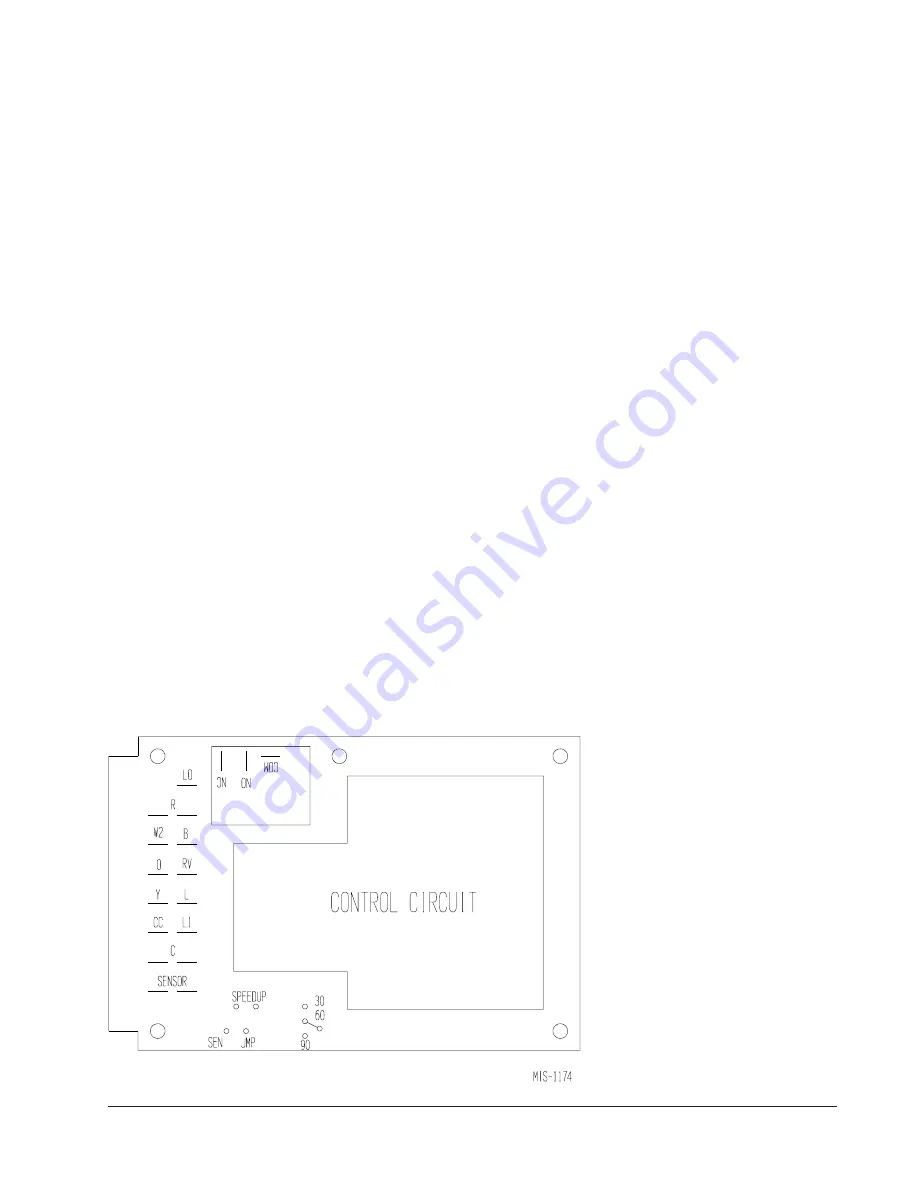
Manual 2100-413G
Page
21 of 28
DEFROST CYCLE
The defrost cycle is controlled by temperature and time
on the solid state heat pump control. See Figure 12.
When the outdoor temperature is in the lower 40°F
temperature range or colder, the outdoor coil
temperature is 32°F or below. This coil temperature is
sensed by the coil temperature sensor mounted near the
bottom of the outdoor coil. Once coil temperature
reaches 30°F or below, the coil temperature sensor
sends a signal to the control logic of the heat pump
control and the defrost timer will start.
After 60 minutes at 30°F or below, the heat pump
control will place the system in the defrost mode.
During the defrost mode, the refrigerant cycle switches
back to the cooling cycle, the outdoor motor stops,
electric heaters are energized, and hot gas passing
through the outdoor coil melts any accumulated frost.
When the temperature rises to approximately 57°F, the
coil temperature sensor will send a signal to the heat
pump control which will return the system to heating
operations automatically.
If some abnormal or temporary condition such as a high
wind causes the heat pump to have a prolonged defrost
cycle, the heat pump control will restore the system to
heating operation automatically after 10 minutes.
The heat pump defrost control board has an option of
30, 60 or 90-minute setting. All models are shipped
from the factory on the 60-minute pin. If special
circumstances require a change to another time, remove
the wire from the 60-minute terminal and reconnect to
the desired terminal. The manufacturer's
recommendation is for 60-minute defrost cycles. Refer
to Figure 12.
There is a cycle speed up jumper on the control. This
can be used to reduce the time between defrost cycle
operation without waiting for time to elapse.
Use a small screwdriver or other metallic object, or
another 1/4 inch QC, to short between the
SPEEDUP
terminals to accelerate the HPC timer and initiate
defrost.
Be careful not to touch any other terminals with the
instrument used to short the
SPEEDUP
terminals. It
may take up to 10 seconds with the
SPEEDUP
terminals
shorted for the speedup to be completed and the defrost
cycle to start.
As soon as the defrost cycle kicks in remove the
shorting instrument from the SPEEDUP terminals.
Otherwise the timing will remain accelerated and run
through the 1-minute minimum defrost length sequence
in a matter of seconds and will automatically terminate
the defrost sequence.
There is an initiate defrost jumper (sen jump) on the
control that can be used at any outdoor ambient during
the heating cycle to simulate a 0° coil temperature. This
can be used to check defrost operation of the unit
without waiting for the outdoor ambient to fall into the
defrost region.
By placing a jumper across the
SEN JMP
terminals (a
1/4 inch QC terminal works best) the defrost sensor
mounted on the outdoor coil is shunted out and will
activate the timing circuit. This permits the defrost
cycle to be checked out in warmer weather conditions
without the outdoor temperature having to fall into the
defrost region.
In order to terminate the defrost test the
SEN JMP
jumper must be removed. If left in place too long the
compressor could stop due to the high pressure control
opening because of high pressure condition created by
operating in the cooling mode with outdoor fan off.
Pressure will rise fairly fast as there is
likely no actual frost on the outdoor
coil in this artificial test condition.
There is also a 5-minute compressor
time delay function built into the HPC.
This is to protect the compressor from
short cycling conditions. In some
instances it is helpful to the service
technician to override or speed up this
timing period, and shorting out the
SPEEDUP
terminals for a few seconds
can do this.
FIGURE 12
DEFROST CONTROL BOARD