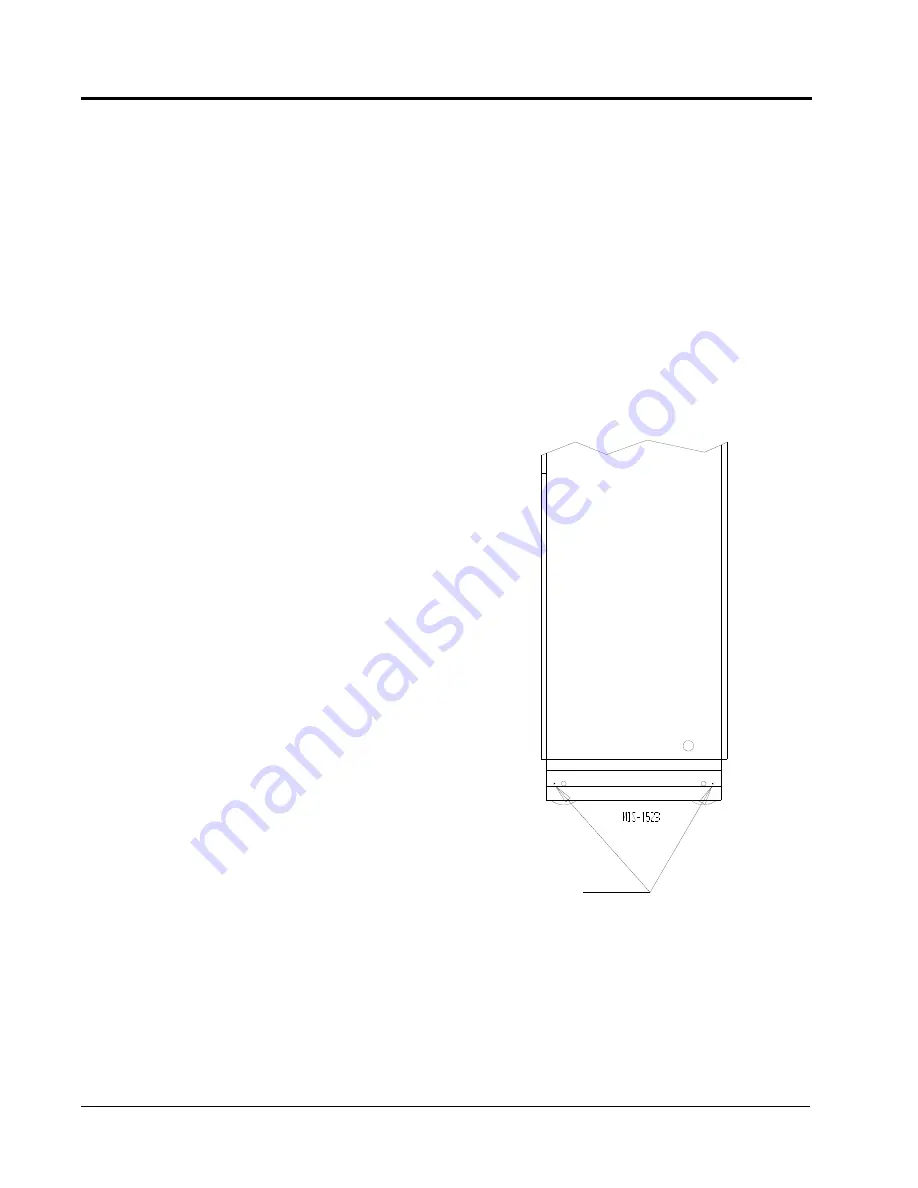
Manual 2100-416J
Page
16 of 27
INSTALLATION INSTRUCTIONS
MOUNTING THE UNIT
When installing a QC
unit near an interior wall on the
left side, a minimum of 8" is required; 12" is preferred.
When installing a QC
unit near an interior wall on the
right side, a minimum of 12" is required as additional
space is required to connect the drain.
This clearance is required to allow for the attachment
of the unit to the wall mounting brackets and the side
trim pieces to the wall.
This unit is to be secured to the wall with the wall
mounting brackets provided. The unit itself, the supply
duct, and the free blow plenum are suitable for “0”
clearance to combustible material.
NOTE:
When a wall sleeve is to be used discard the
brackets shipped with the heat pump and
attache the unit to the sleeve with bracket
supplied with the wall sleeve.
Following are the steps for mounting the QC units; for
reference see Figure 13.
1. Attach wall mounting bracket to the structure wall
with field-supplied lag bolts. The fluid piping
connections are to be within the confines of this
bracket. See Figure 1 for cabinet openings and
location of fluid coil connection points.
2. Position the unit in front of the wall mounting
bracket.
3. Remove the locking screws from the wheels. Refer
to Figure 12.
4. Roll the unit up to the wall mounting bracket.
The unit must be level from side to side. If any
adjustments are necessary, shim up under the
rollers with sheets of steel or any substance that is
not affected by moisture.
5. Secure the unit to the wall bracket with provided
#10 hex head sheet metal screws. There are
prepunched holes in the cabinet sides, and
the bracket has slotted holes to allow for some
misalignment.
6. Position the bottom trim piece to the unit and
attach with provided screws (dark colored).
7. Position side trim pieces to the wall and attach
with field-supplied screws. There are two long and
two short pieces supplied. The long pieces are to
enclose the gap behind the unit. The short pieces
are to fill the gap behind the cabinet extension or
the free blow plenum box. They may be cut to suit
the ceiling height or overlap the unit side trim.
There is sufficient length to trim up to a 10'-2"
ceiling.
FIGURE 12
Removing Locking Screws from Wheels
REMOVE SCREWS
FROM WHEELS BEFORE
ROLLING INTO PLACE
Summary of Contents for QC501
Page 6: ...Manual 2100 416J Page 6 of 27 FIGURE 1 Unit Dimensions...
Page 9: ...Manual 2100 416J Page 9 of 27 FIGURE 4 Installation of Unit through Wall with Wall Sleeve...
Page 14: ...Manual 2100 416J Page 14 of 27 FIGURE 10 Fresh Air Damper Removal MOUNTING SCREW...
Page 21: ...Manual 2100 416J Page 21 of 27 FIGURE 16 Remote Thermostat Wiring Diagram X Option...
Page 22: ...Manual 2100 416J Page 22 of 27 FIGURE 17 Remote Thermostat Wiring Diagram D Thermostat Option...