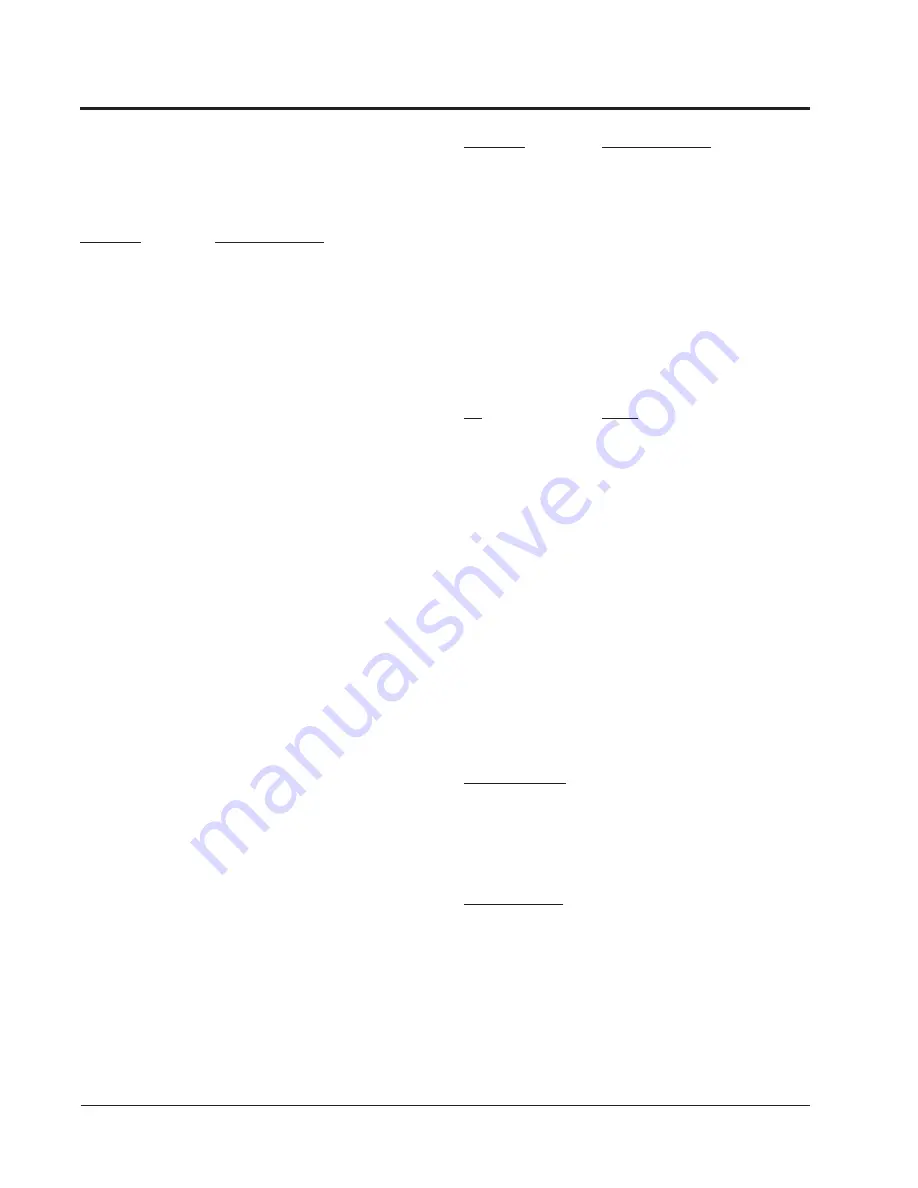
Manual
2100-467D
Page
22 of 25
NOTE: Affects Models PA13241, PA13301, PA13361
TROUBLESHOOTING GE ECM 2.3
™
MOTORS
CAUTION:
Disconnect power from unit before removing or replacing
connectors, or servicing motor. To avoid electric shock from
the motor’s capacitors, disconnect power and wait at least 5
minutes before opening motor.
Symptom
Cause/Procedure
Motor rocks slightly
•
This is normal start-up for ECM
when starting
Motor won’t start
•
Check blower turns by hand
• No movement
• Check power at motor
• Check low voltage (24 Vac R to C) at motor
• Check low voltage connections
(G, Y, W, R, C) at motor
• Check for unseated pins in connectors on
motor harness
• Test with a temporary jumper between R - G
• Check motor for tight shaft
• Perform motor/control replacement check
•
Perform Moisture Check
• Motor rocks,
• Check for loose or compliant motor mount
but won’t start
• Make sure blower wheel is tight on shaft
• Perform motor/control replacement check
Motor oscillates up
• It is normal for motor to oscillate with no
load
& down while being
on shaft
tested off of blower
Motor starts, but
runs erratically
• Varies up and down
• Check line voltage for variation or “sag”
or intermittent
• Check low voltage connections
(G, Y, W, R, C) at motor, unseated pins in
motor harness connectors
• Check “Bk” for erratic CFM command (in
variable-speed applications)
• Check out system controls, Thermostat
•
Perform Moisture Check
• “Hunts” or “puffs” at
• Does removing panel or filter reduce
high CFM (speed)
“puffing”?
- Reduce restriction
- Reduce max airflow
• Stays at low CFM
• Check low voltage (Thermostat) wires and
despite system call
connections
for cool or heat CFM
• Verify fan is not in delay mode; wait until
delay complete
• “R” missing/not connected at motor
• Perform motor/control replacement check
• Stays at high CFM
• “R” missing/not connected at motor
• Is fan in delay mode? - wait until delay time
complete
• Perform motor/control replacement check
• Blower won’t shut off
• Current leakage from controls into G, Y or W?
Check for Triac switched thermostat or solid-
state relay
Excessive noise
• Determine if it’s air noise, cabinet, duct or
motor noise; interview customer, if necessary
• Air noise
• High static creating high blower speed?
- Is airflow set properly?
- Does removing filter cause blower to slow
down? Check filter
- Use low-pressure drop filter
- Check/correct duct restrictions
Symptom
Cause/Procedure
• Noisy blower or cabinet
•
Check for loose blower housing, panels, etc.
• High static creating high blower speed?
- Check for air whistling through seams in
ducts, cabinets or panels
- Check for cabinet/duct deformation
• “Hunts” or “puffs” at
•
Does removing panel or filter reduce
high CFM (speed)
“puffing”?
- Reduce restriction
- Reduce max. airflow
Evidence of Moisture
• Motor failure or
• Replace motor and
Perform Moisture
Check
malfunction has occurred
and moisture is present
• Evidence of moisture
•
Perform Moisture Check
present inside air mover
Do
Don’t
• Check out motor, controls,
•
Automatically assume the motor is bad.
wiring and connections
thoroughly before replacing
motor
• Orient connectors down so • Locate connectors above 7 and 4 o’clock
water can’t get in
positions
- Install “drip loops”
• Use authorized motor and
• Replace one motor or control model # with
model #’s for replacement another (unless an authorized replacement)
• Keep static pressure to a
• Use high pressure drop filters some have
½"
minimum:
H
2
0 drop!
- Recommend high
• Use restricted returns
efficiency, low static filters
- Recommend keeping filters
clean.
- Design ductwork for min.
static, max. comfort
- Look for and recommend
ductwork improvement,
where necessary
• Size the equipment wisely
• Oversize system, then compensate with low
airflow
• Check orientation before
• Plug in power connector backwards
inserting motor connectors
• Force plugs
Moisture Check
• Connectors are oriented “down” (or as recommended by equipment
manufacturer)
• Arrange harness with “drip loop” under motor
• Is condensate drain plugged?
• Check for low airflow (too much latent capacity)
• Check for undercharged condition
• Check and plug leaks in return ducts, cabinet
Comfort Check
• Check proper airflow settings
• Low static pressure for lowest noise
• Set low continuous-fan CFM
• Use humidistat and 2-speed cooling units
• Use zoning controls designed for ECM that regulate CFM
• Thermostat in bad location?