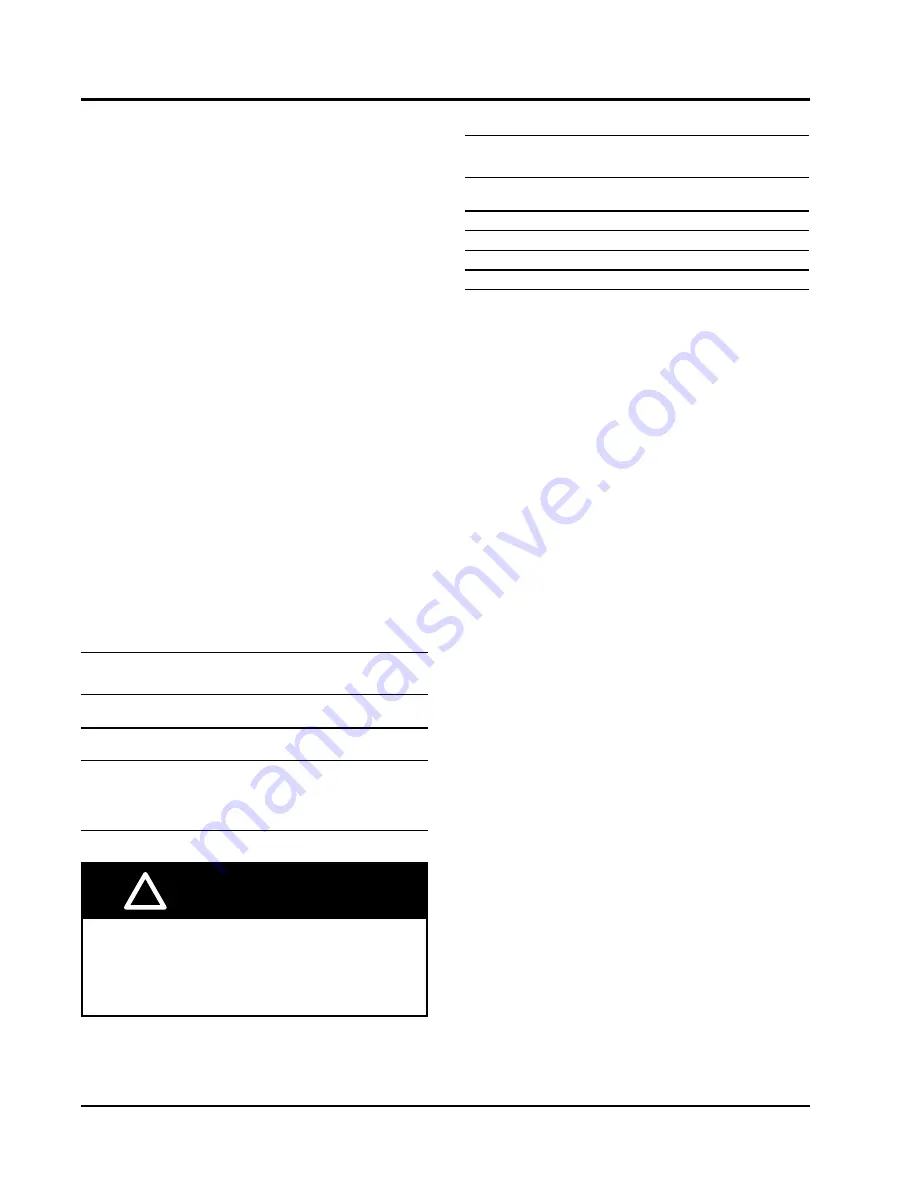
Manual 2100-647D
Page
6 of 36
Failure to provide the 1/4" clearance
between the supply duct and a combustible
surface for the first 3' of duct can result in
fire causing damage, injury or death.
!
WARNING
INSTALLATION
WALL MOUNTING INFORMATION
1. Two holes for the supply and return air openings
must be cut through the wall as shown in Figures
3A-D on pages 9-12.
2. On wood frame walls, the wall construction must
be strong and rigid enough to carry the weight of
the unit without transmitting any unit vibration.
3. Concrete block walls must be thoroughly inspected
to insure that they are capable of carrying the
weight of the installed unit.
MOUNTING THE UNIT
1. These units are secured by wall mounting brackets
which secure the unit to the outside wall surface at
both sides. A bottom mounting bracket, attached
to skid for shipping, is provided for ease of
installation, but is not required.
2. The unit itself is suitable for 0 clearance, but the
supply air duct flange and the first 3' of supply
air duct require a minimum of 1/4" clearance to
combustible material for Model Series H36, H42,
H48, H60 and H72. However, it is generally
recommended that a 1" clearance is used for
ease of installation and maintaining the required
clearance to combustible material. See Figures
3A-D for details on opening sizes.
3. Locate and mark lag bolt locations and bottom
mounting bracket location (see Figures 3A-D).
4. Mount bottom mounting bracket.
5. Hook top rain flashing, attached to front-right
corner of supply flange for shipping, under back
bend of top.
6. Position unit in opening and secure with fasteners
sufficient for the application such as 5/16 lag bolts;
use 7/8" diameter flat washers on the lag bolts.
7. Secure rain flashing to wall and caulk across entire
length of top (see Figures 3A-D).
8. For additional mounting rigidity, the return air
and supply air frames or collars can be drilled
and screwed or welded to the structural wall itself
(depending upon wall construction). Be sure to
observe required clearance if combustible wall.
9. On side-by-side installations, maintain a minimum
of 20" clearance on right side to allow access to
control panel and heat strips, and to allow proper
airflow to the outdoor coil. Additional clearance
may be required to meet local or national codes.
10. Care should be taken to ensure that the
recirculation and obstruction of condenser
discharge air does not occur. Recirculation of
condenser discharge air can be from either a
single unit or multiple units. Any object such as
shrubbery, a building or other large object can
cause obstructions to the condenser discharge
air. Recirculation or reduced airflow caused by
obstructions will result in reduced capacity,
possible unit pressure safety lockouts and reduced
unit service life.
For units with blow through condensers, it is
recommended there be a minimum distance of 10'
between the front of the unit and any barrier or 20'
between the fronts of two opposing (facing) units.
NOTE:
For side-by-side installation of two H**A models there
must be 20" between units. This can be reduced to 15"
by using a H**L model (left side compressor and controls)
for the left unit and H**A (right side compressor and
controls) for right unit.
Clearances Required for Service Access and
Adequate Condenser Airflow
MODELS
LEFT
SIDE
RIGHT
SIDE
DISCHARGE
SIDE
H12A, H24A, H36A
15"
20"
10'
H24L, H36L
20"
15"
10'
H42A, H48A, H60A, H72A
20"
20"
10'
H42L, H48L, H60L, H72L
20"
20"
10'
Minimum Clearances Required to
Combustible Materials
MODELS
SUPPLY AIR DUCT
FIRST 3'
CABINET
H12A
H24A, H24L
0"
0"
H36A, H36L
H42A, H42L
H48A, H48L
H60A, H60L
H72A, H72L
1/4"
0"