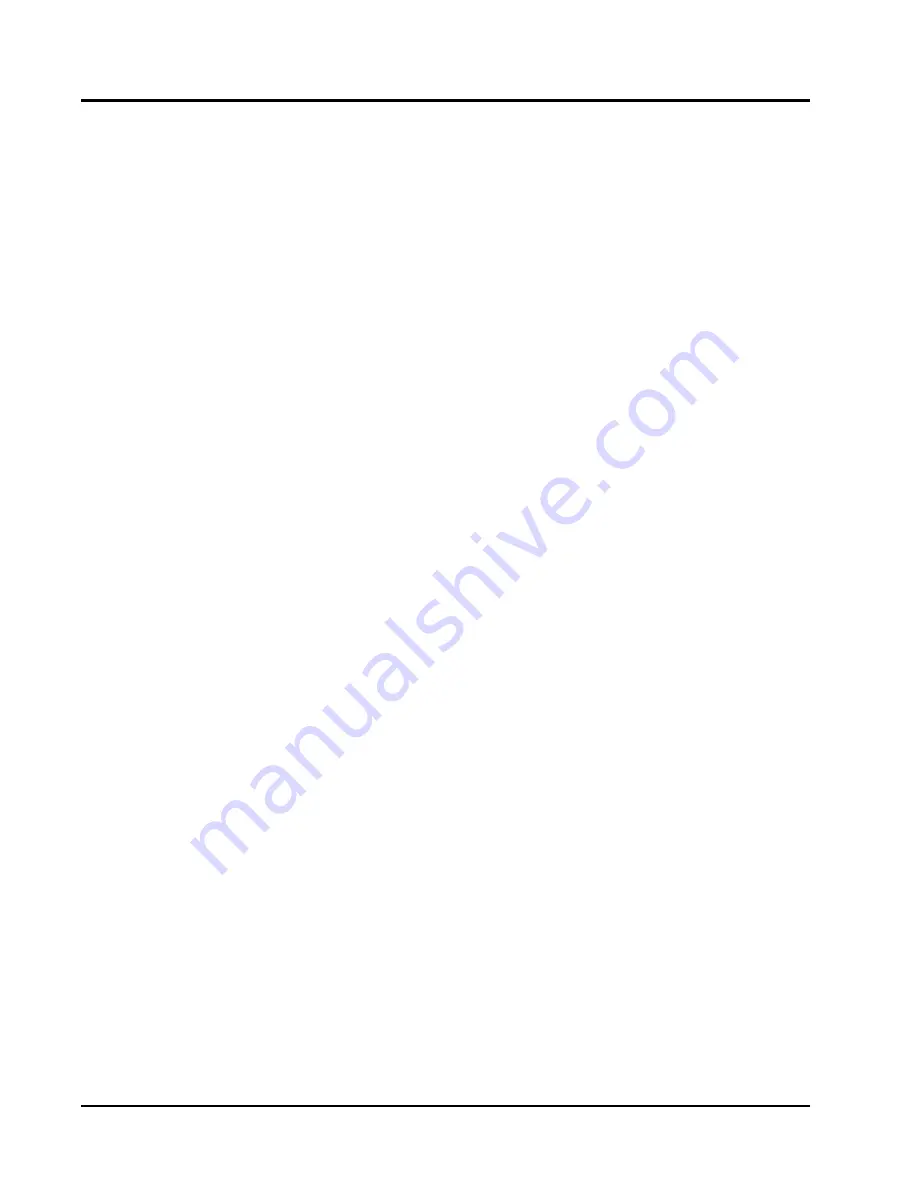
Manual 2100-711C
Page
8 of 45
INSTALLATION
Basic Installation Design and
Application Planning
Successful unit installations require proper planning
and site inspection before installation begins. Before
installing the wall mount unit, make sure that all
service and airflow clearances are met and that the
unit can meet all applicable code and regulation
requirements. Provide an inspection of both the inside
and outside of the structure by reviewing floorplans
and/or visiting the installation site.
Wall Construction
The wall must be inspected to ensure that the weight
of the unit can be supported. Be sure to review all
applicable construction codes and regulations including
seismic requirements. When inspecting wood frame
walls, the wall construction must be strong and
rigid enough to carry the weight of the unit without
transmitting any unit vibration. It is important that
the side unit wall mounting lags and optional bottom
bracket are supported by structural members inside
the wall cavity. Concrete block and brick walls must be
thoroughly inspected to ensure that they are capable
of carrying the weight of the installed unit. Metal
buildings must contain structural components to
support the unit weight. If heavily corrugated siding
is present, it may need to be trimmed and flashed to
provide a flat, even surface to attach and seal the unit
to the wall.
Outdoor Area Inspection
Inspect the outdoor area of the jobsite or review
construction plans and locate the area where the wall
mount is to be installed. The outdoor area must be
free from obstructions including fences, bushes and
walls that will hinder unit operation regarding outdoor
condenser airflow and unit serviceability. Do not
install units in enclosed areas that limit the amount
of ambient temperature airflow. Warm air will exit
the front condenser section of the unit, and outdoor
ambient temperature air must be able to enter side
intake condenser openings of the unit. Portable or
modular building placement must be in a way that the
wall mount units have a constant supply of outdoor air
for proper unit operation. Make sure that the service
panels of the unit are accessible. Inspect wall surfaces
for obstructions that could hinder unit installation
and servicing including outdoor electrical conduits,
junction boxes, wall drains, vent hoods, windows, doors,
overhangs and posts.
Condensate Water Drainage
Review all codes and requirements for unit condensate
drainage. A clear, flexible PVC drain hose (3/4" ID, 1"
OD) extends from the drain pan in the upper section of
the unit and extends down to the unit base. An opening
is supplied towards the back of the unit base for the
drain hose to pass through, and the hose extends 1"
to 2" below the unit base. Water removed from the
indoor air (condensate) will be expelled from the unit
in large amounts during cooling operation through the
hose. Units running in cooling operation in cold outdoor
below freezing conditions can cause the condensate
to freeze after leaving the drain hose. In the event the
drain hose is connected to a drain system of some type,
it must be an open or vented type system to ensure
proper drainage throughout seasonal use.
Indoor Ducted and Non-Ducted
Applications
Air distribution inside the structure being conditioned
plays an important role in making sure the area is
a consistent temperature. Improper air distribution
can result in areas being cooler or warmer, electrical
equipment not receiving sufficient airflow or occupancy
discomfort felt inside an area. Thermostat or indoor
temperature sensor placement inside the area being
conditioned also plays an important role in indoor
climate control.
Indoor Supply Airflow
Indoor installation areas must provide a non-restrictive
path for the conditioned supply air to leave supply
grilles and registers. Inspect the area to ensure that all
indoor portions of the room or rooms will have access
to supply air. Ductwork may be used to ensure proper
air circulation and all provided ductwork guidelines and
clearances must be followed. Non-ducted applications
must use a supply louver grille installed over the supply
opening inside the room. Be sure to adjust supply
deflectors to properly disperse the conditioned supply
air to all parts of the room. Avoid closing sections of
the supply grilles which would cause unneeded supply
duct pressurization.
Indoor Return Airflow
A non-restrictive path for room air returning to the
center section of the unit must be provided inside
the room. Avoid placing objects including furniture,
electronics equipment, equipment racks and cabinets
directly in front of the unit return grilles and registers.
Bard recommends at least 2' between solid objects
and return grilles or registers. Ductwork may be used to
ensure proper air circulation and all provided ductwork
guidelines and clearances must be followed. Non-
ducted applications must use a return louver grille
installed over the return opening inside the room.
Ducted Applications
Field fabricated supply and return duct work may be
installed inside the structure being conditioned. A short