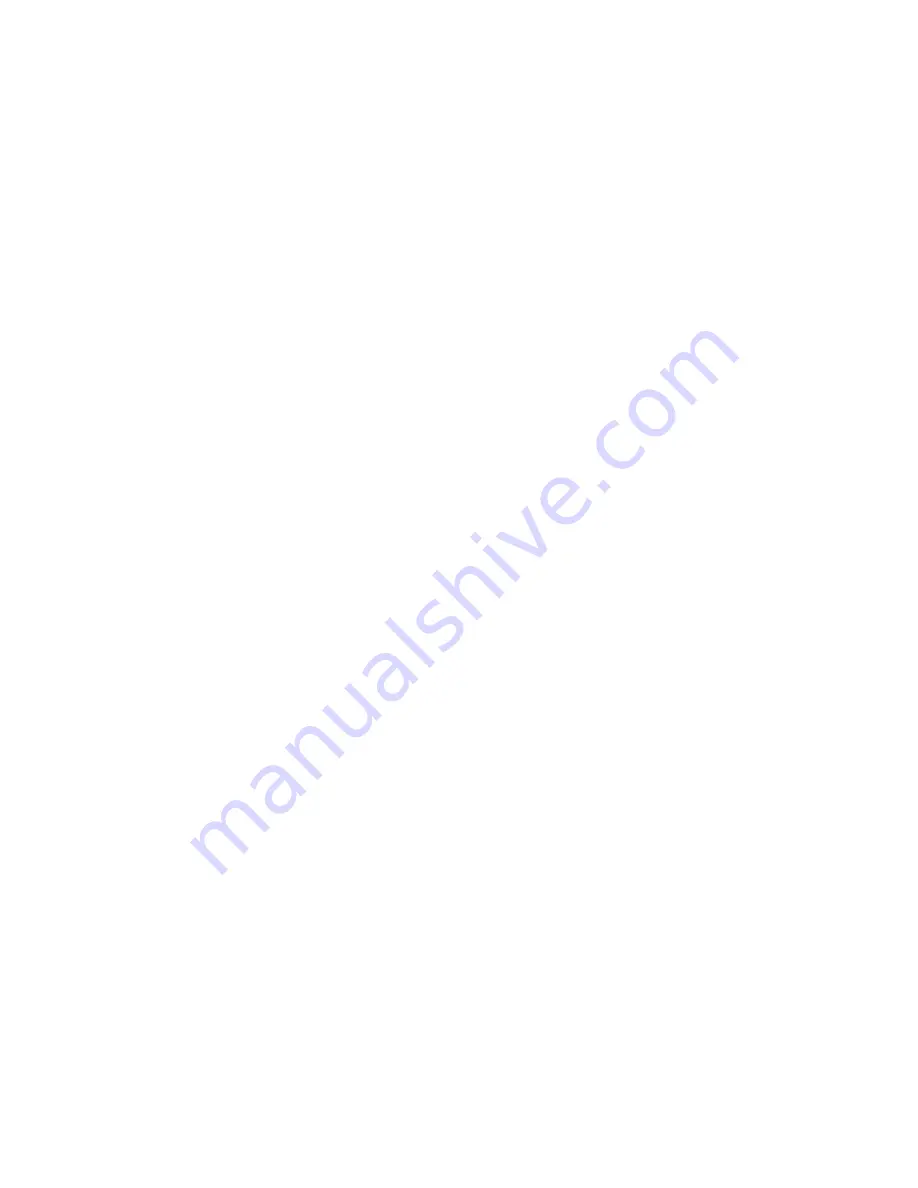
61780 0221
BARBER SURF RAKE
®
MAINTENANCE ADJUSTMENTS
DAILY ADJUSTMENT CHECK
There are four basic component checks for proper adjustment to ensure that
your Surf Rake
®
is operating to the efficiency for which it was designed. The four adjustments work together
and should be checked each time the machine is used.
1. TIRE PRESSURE
It is important for the proper operation of the Surf Rake
®
to have the two rear tires
inflated to the same pressure.
TO ADJUST TIRE PRESSURE:
Inflate tires to 18 PSI.
When the tires are not inflated the same, the tire with the lower pressure will in turn lower that side of the
Surf Rake
®
and cause the tines on that side to be lower. The result is the conveyor belt will clean
unevenly, possibly picking up sand on the lower side or not cleaning deep enough on the higher side.
2. BUCKET / LIFT ARM CHAIN ASSEMBLIES
It is important for the proper operation of the Surf Rake
®
to
have the bucket/lift arm chains on each side of the Surf Rake
®
under the same tension, and not left loose,
so they will share the load when lifting and tripping the hopper.
TO ADJUST BUCKET CHAINS:
When the bucket is sitting on the frame, the chain/turnbuckle assemblies
should be tight. Tighten up loose chain/turnbuckle assemblies so that both sides have the same tension
and the bucket support blocks are just off or barely touching the frame.
When one chain assembly is loose while raising the bucket, all the weight and pressure of lifting the
bucket is shifted to the tighter chain assembly. This causes the tighter chain assembly to stretch
more than it would if both chain assemblies were the same tension. This causes premature wear to
the links and the chains and can cause sudden failure to one or both of the chain assemblies. If
both chains become loose, the bucket will not fully return to the forward/bottom position and will
bottom out farther back on the frame than it should. This will allow a gap between the bucket and
the path of the debris being thrown by the conveyor that allows the debris to drop down in front of
the bucket.
3. CONVEYOR BELT TENSION
It is important for the proper operation of the Surf Rake
®
to have both sides
of the conveyor belt with the same tension.
TO ADJUST THE CONVEYOR BELT:
Open the side guard doors on both sides of the Surf Rake
®
. Pull
the conveyor belt back and forth midway between the upper 8” idler roller wheel and lower 8” idler roller
wheel to check for amount of play. If there is more than 1 ½” of play, tighten the adjusting bolt. This will
raise the upper shaft and tighten the conveyor assembly. Repeat this procedure on the other side of the
conveyor assembly. Take some time and go back and forth to each side of the machine, checking that
both sides are the same tension. Once both sides are the same tension, retighten the jam nuts on the take
up bolts and refasten the doors/guards.
When the conveyor belt assembly is loose on one side, the belt will naturally sag on that side and cause
the tines to drag on that side. The result is premature wear to the tines, an uneven cleaning and possibly
picking up sand.
4. MOLDBOARD HEIGHT
It is important for the proper operation of the Surf Rake
®
to have both sides of the
moldboard adjusted identically to the same height. The moldboard is initially set evenly. For most
applications, this factory setting works well. If the factory setting is changed, be advised that a small amount
of adjustment has dramatic results. Do not move more than ¼” at a time without testing the new setting in
the sand for a period of time. Use the guides at the sides of the moldboard to align both sides identically.
TO ADJUST:
Loosen the turnbuckle locking arms on the sides to be moved. Use the guides at each side
of the moldboard to level the moldboard to the desired height. Be sure that the guides are set at the same
mark or location on each side. Retighten the turnbuckle locking arm/s.
4-2