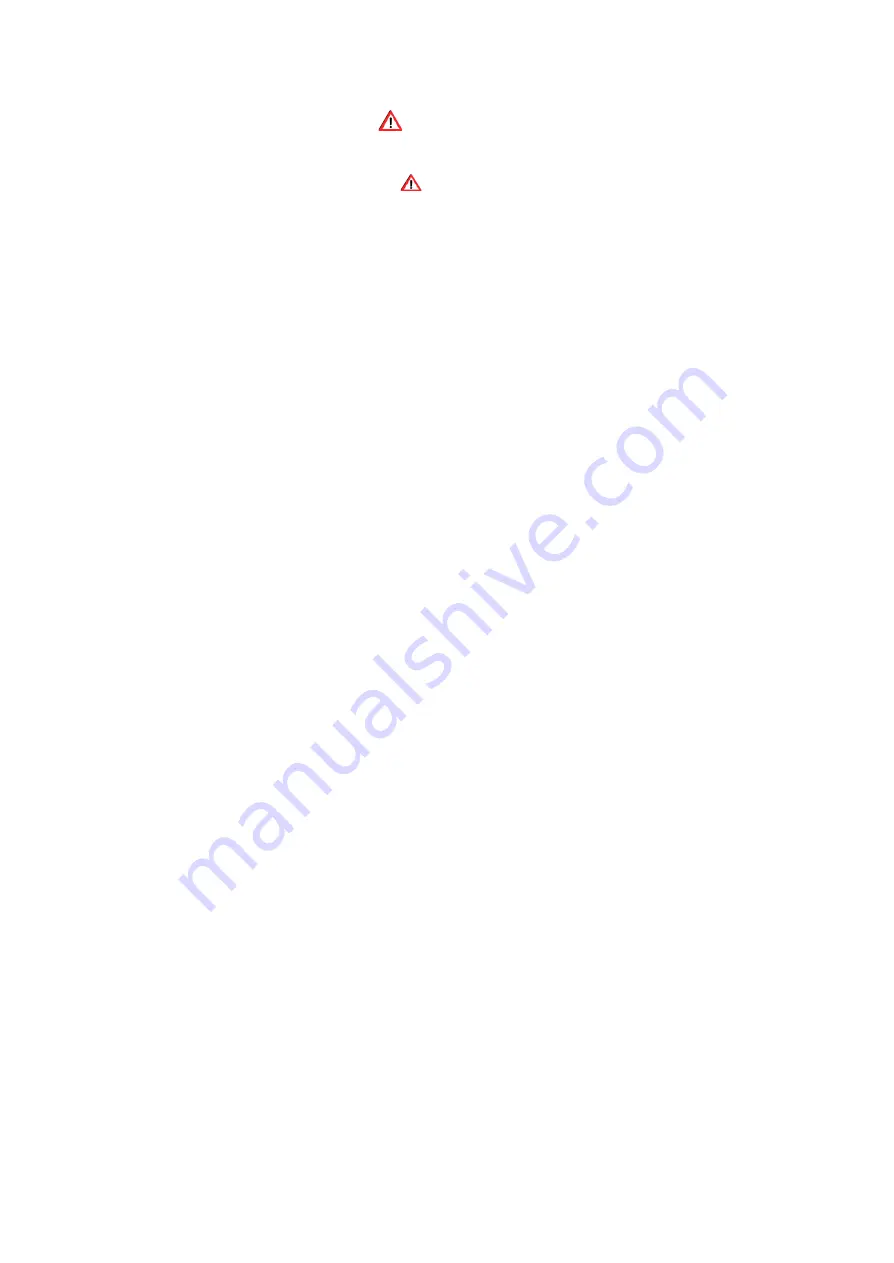
Safety Instruction
1.
Users are required to read the operation manual completely and carefully before installation
or operation.
2.
All the instruction marked with sign
must be observed or executed; otherwise, bodily
injuries might occur.
3.
The product should be installed and pre-operated by well-trained persons.
4.
For perfect operation and safety, it is prohibited that using extension cable with multi-outlet
for power connection.
5.
When connecting power supply cords to power sources, it is necessary to make sure that the
power voltage matches the rated voltage ±20% indicated on the motor’s name plate.
6.
Don
'
t operate in direct sun light
,
outdoors area and where the room temperature is over
45°C or below 5°C.
7.
Please avoid operating near the heater at dew area or at the humidity below 30% or above
95%.
8.
Don
'
t operate in area with heavy dust, corrosive substance or volatile gas.
9.
Avoid power cord being applied by heavy objects or excessive force, or over bend.
10. The earth wire of power cord must be connected to the system ground of the production plant
by proper size of conductions and terminals. This connection should be fixed permanently.
11. All the moving portions must be prevented to be exposed by the parts provided.
12. Turing on the machine in the first time, operate the sewing machine at low speed and check
the correct rotation direction.
13. Turn off the power before the following operation
:
a) Connecting or disconnecting any connectors on the control box or motor.
b) Threading needle.
c) Raising the machine head.
d) Repairing or doing any mechanical adjustment.
e) Machines idling.
14. Repairs and high level maintenance work should only be carried out by electronic technicians
with appropriate training.
15. All the spare parts for repair must be provided or approved by the manufacturer.
16. Don’t use any objects or force to hit or ram the product.
Guarantee Time
Warranty period of this product is 1 year dated from purchasing, or within 2 years from
ex-factory date.
Warranty Detail:
Any trouble found within warranty period under normal operation, it will be repaired free of
charge. However, maintenance cost will be charged in the following cases even if within
warranty period:
1. Inappropriate use, including: wrong connecting high voltage, wrong application, disassemble,
repair, modification by incompetent personnel, or operation without the precaution, or
operation out of its specification range, or inserting other objects or liquids into the product.
2. Damage by fire, Earth quake, lighting, wind, flood, salt corrosive, moisture, abnormal power
voltage and any other damage cause by the natural disaster or by the inappropriate
environments.
3. Dropping after purchasing or damage in transportation by customer himself or by customer’s
shipping agency
Note: We make our best effort to test and manufacture the product for assuring the quality.
However, it is possible that this product can be damaged due to external magnetic
interference and electronic static or noise or unstable power source more than expected;
therefore the grounding system of operate area must guarantee the good earth and it’s also
recommended to install a failsafe device. (Such as residual current breaker)
1