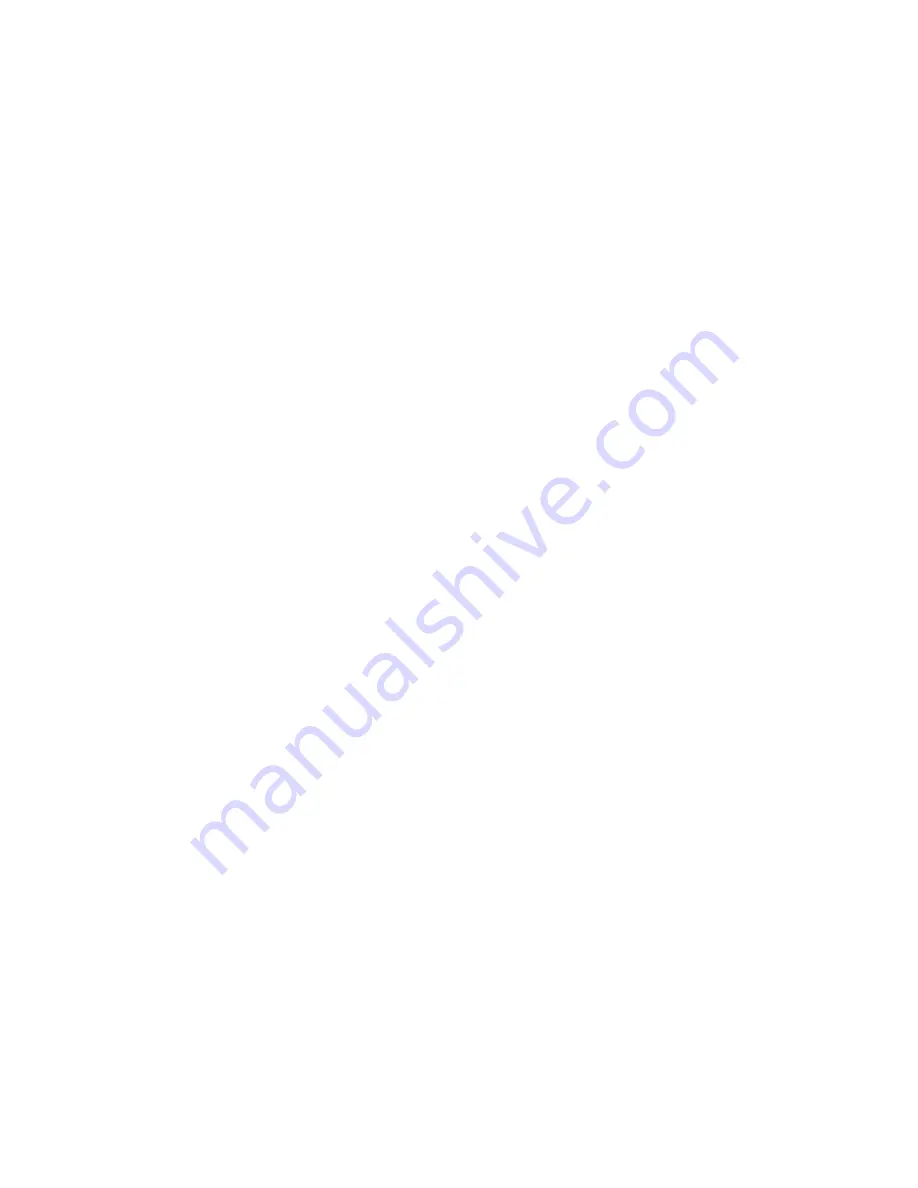
86
8.2 Inner & outer mast
The mast assembly is of the free lift range-contained two stage telescopic type
consisting of the inner and outer mast, and is sustained by mast supports. The mast
supports are welded to the bottom of the outer mast, being extended from the axle
housing. The outer masts are provided with brackets for lock pins of tilt cylinder
connecting hardware. The mast is tilted by operation of the tilt cylinders.
The inner mast is composed of right and left mast frames which are connected with
each other by upper and lower connecting members. At the upper inside of each outer
mast frame an end roller is installed on the end roller shaft welded to the frame, with a
snap ring. In addition, the outer mast frames are fitted with side rollers to sustain the
inner mast frames. At the lower outside of each inner mast frame an end roller is
installed on the end roller shaft with snap ring, which is welded to the inner mast. Under
the end rollers other side rollers are located to sustain transverse load. With the aid of
these rollers, the inner mast can smoothly operate.
Notice:
Please pay more regard to safety when maintaining the main rollers and
side rollers on the upper of outer mast.
8.3 Lift bracket
At the lift brackets, end rollers that roll along the inside of the inner mast frames are
installed on the end roller shafts with snap rings. The end roller shafts are welded to the
lift brackets. The side rollers that roll along on the inside of the inner mast frames are
bolt fitted, being shim adjusted. To prevent the rolling of the finger bar, two retaining
rollers are used, which roll along on the outside of inner mast frames. The longitudinal
load is sustained by the end rollers of which the upper ones emerge from the top mast
when the forks reach the maximum lift height.
The transverse load is sustained by upper retaining rollers and lower side rollers. As we
mentioned above, the mast assembly and lift brackets are designed with rigidity, stability
and smooth operation in mind.
Furthermore, the finger bar and lift brackets are made into one body construction
using high tension steel to improve the durability. This meets the ISO Standards.
The two forks installed on the finger bar are made of special alloy steel which has
been subjected to heat treatment.
The fork pin fastens the fork on the definite position. When adjusting the clearance
Summary of Contents for CPCD 80
Page 1: ...Original instructions...
Page 25: ...19 4 Lubrication system 5 Capacity chart 6 Inspections before starting...
Page 32: ...26 Lubrication diagram...
Page 50: ...44 Fig 2 4 Forward shift clutch Fig 2 5 Reverse shift clutch Fig 2 6 Control valve...
Page 61: ...55 Fig 4 2 Position of brake pedal...
Page 99: ...93 Fig 9 1 Principle diagram of electric system domestic CPCD80 100CY...
Page 100: ...94 Fig 9 2 Principle diagram of electric system imported CPCD80 100W...
Page 104: ...98 Fig9 5 1 Diagram of meter harness domestic CPCD80 100CY...
Page 105: ...99 Fig9 5 2 Diagram of meter harness imported CPCD80 100W...
Page 106: ...100 Fig9 5 3 Diagram of main harness domestic CPCD80 100CY...
Page 107: ...101 Fig9 5 4 Diagram of main harness imported CPCD80 100W...
Page 109: ...103 NOTE...
Page 110: ...104...
Page 112: ...106 incurring any obligation...