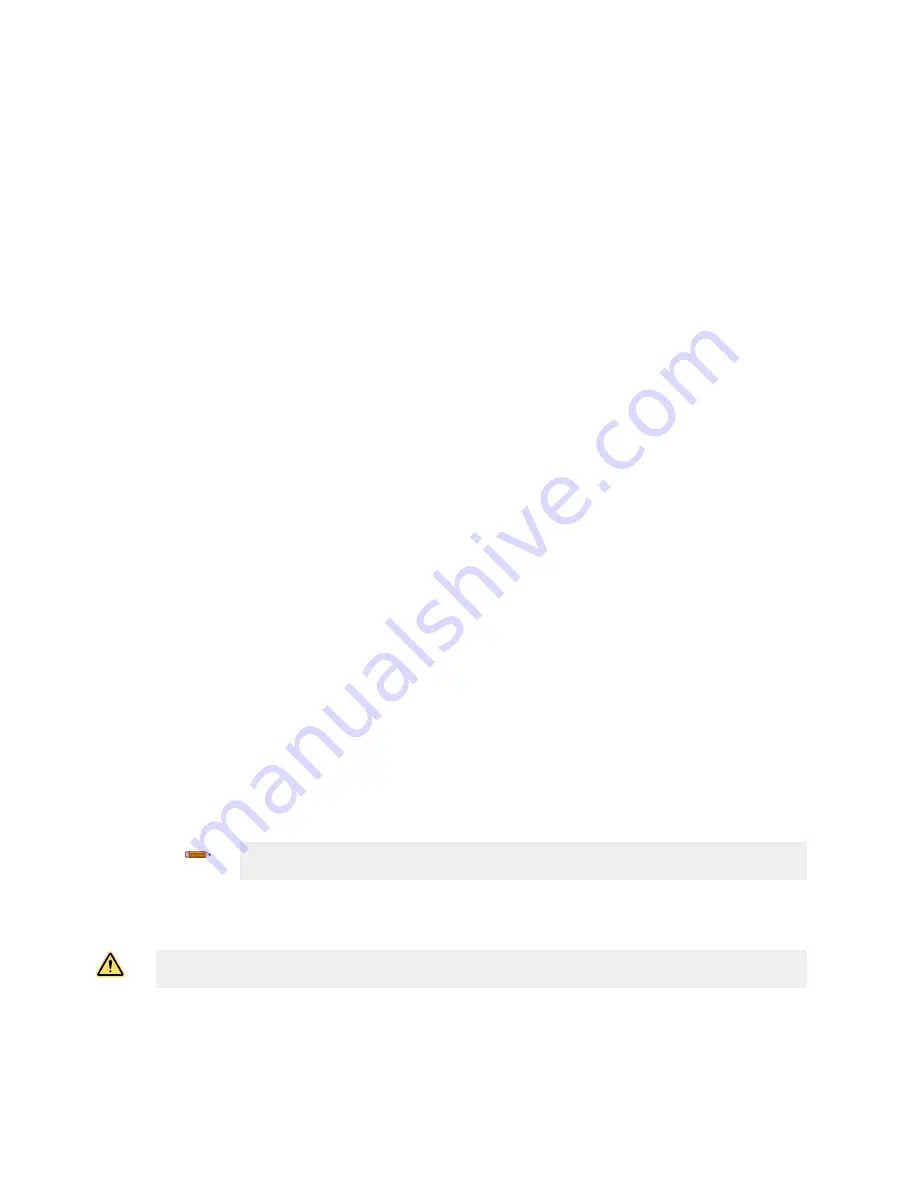
• Ensure proper System function whenever any maintenance or modification is performed on the System or on the
machinery that is guarded by the System.
6.3.1 Configuring the System for Initial Checkout
For the initial checkout, the EZ-SCREEN LS System must be checked without power available to the guarded machine.
Final interface connections to the guarded machine cannot take place until the light screen system has been checked out.
This may require lockout/tagout procedures (refer to OSHA1910.147, ANSI Z244-1, ISO 14118, or the appropriate standard
for controlling hazardous energy). The OSSD connections will be made after the initial checkout procedure has been
successfully completed.
Verify that:
• Power has been removed from (or is not available to) the guarded machine and its controls or actuators
• The machine control circuit or the Safety/Interface Module is not connected to the OSSD outputs at this time
(permanent connections will be made later)
• EDM is configured and wired per application requirements (1-channel or no monitoring, see
6.3.2 Initial Power-Up
1. Inspect the area near the light screen for reflective surfaces, including work pieces and the guarded machine.
Reflective surfaces may cause light beams to reflect around a person in the light screen, preventing the person from
being detected and not stopping the machine motion (see
2. Eliminate the reflective surfaces as much as possible by relocating, painting, masking, or roughening them.
Remaining problem reflections will become apparent during the trip test.
3. Verify that power is removed from the EZ-SCREEN LS System and from the guarded machine and that the OSSD
safety outputs are not connected.
4. Remove all obstructions from the light screen.
5. With the power to the guarded machine Off, make external device monitoring (EDM), power, and earth ground
connections on both the emitter and receiver cables (see
(brown wire) and 0 V dc (blue wire) should be connected to a SELV-rated supply and GND (green/yellow wire) to
earth ground. If the installation does not allow direct connection to earth ground via the cordset, the earth ground
must be provided via the mounting brackets.
6. Power up the EZ-SCREEN LS System only.
7. Verify that the input power is present to both the emitter and the receiver. At least one indicator on both the emitter
and the receiver should be On and the start-up sequence should cycle.
8. Watch both the emitter and the receiver Status indicators and the receiver Alignment indicators to determine the
light screen alignment status:
• An Emitter Lockout Condition—the emitter Status indicator is single-flashing red; the receiver Status
indicator is solid red, and the receiver's 7-segment display reads CH1.
• A Receiver Lockout Condition—the receiver Status indicator is single-flashing red, with Alignment and Run
mode indicators Off, and the receiver 7-segment display shows an Error Code.
• Normal Operating Mode (emitter)—the Status indicator is solid green.
• Clear (Run) Condition (receiver)—the Status indicator is solid green, and the Run mode indicator is solid
amber. All Alignment indicators are solid green.
• A Blocked Condition (receiver)—The Status indicator is solid red, Run mode indicator is solid amber, one or
more Alignment indicator(s) are solid red, identifying the location of the blocked beams, and the number of
blocked beams is displayed.
Note: If beam 1 is blocked, the Alignment indicator 1 will be red and all others Off. Beam 1
provides the synchronization signal.
9. Proceed to
on page 44.
6.3.3 Optical Alignment
CAUTION: Ensure that no individuals are exposed to any hazard if the OSSD outputs turn ON when the
emitter and receiver become aligned.
Verify the optimal alignment, adjusting the sensor rotation with the power on:
1. Verify that the emitter and the receiver are pointed squarely at each other. Use a straight edge (for example, a level)
to determine the direction the sensor is facing. The sensor face must be perpendicular to the optical axis.
EZ-SCREEN
®
LS Safety Light Screen
44
www.bannerengineering.com - Tel: +1.763.544.3164