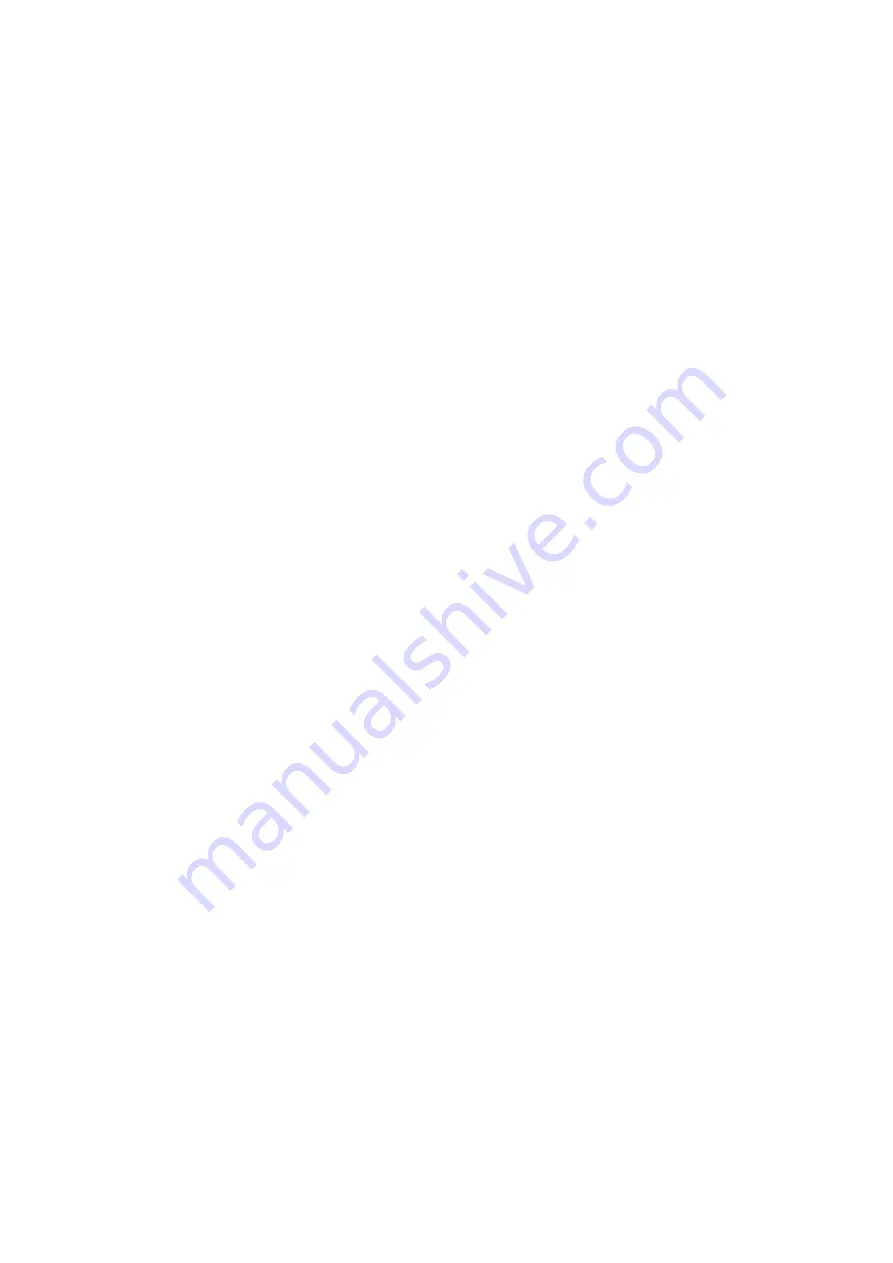
ACOPOSinverter X64
ACOPOSinverter P64new
Migration manual
Version:
1.20 (December 2019)
Order no.:
MAACPIX64-ENG
Translation of the original documentation
All values in this manual are current as of its creation. We reserve the right to change the contents of this manual
without notice. B&R Industrial Automation GmbH is not liable for technical or editorial errors and defects in this
manual. In addition, B&R Industrial Automation GmbH assumes no liability for damages that are directly or indirectly
attributable to the delivery, performance or use of this material. We point out that the software and hardware
designations and brand names of the respective companies used in this document are subject to general trademark,
brand or patent protection.
Summary of Contents for ACOPOSinverter X64
Page 2: ......
Page 21: ...Implementation V 1 20 21...
Page 24: ...Implementation 24 V 1 20...
Page 27: ...Implementation V 1 20 27...
Page 30: ...Implementation 30 V 1 20...