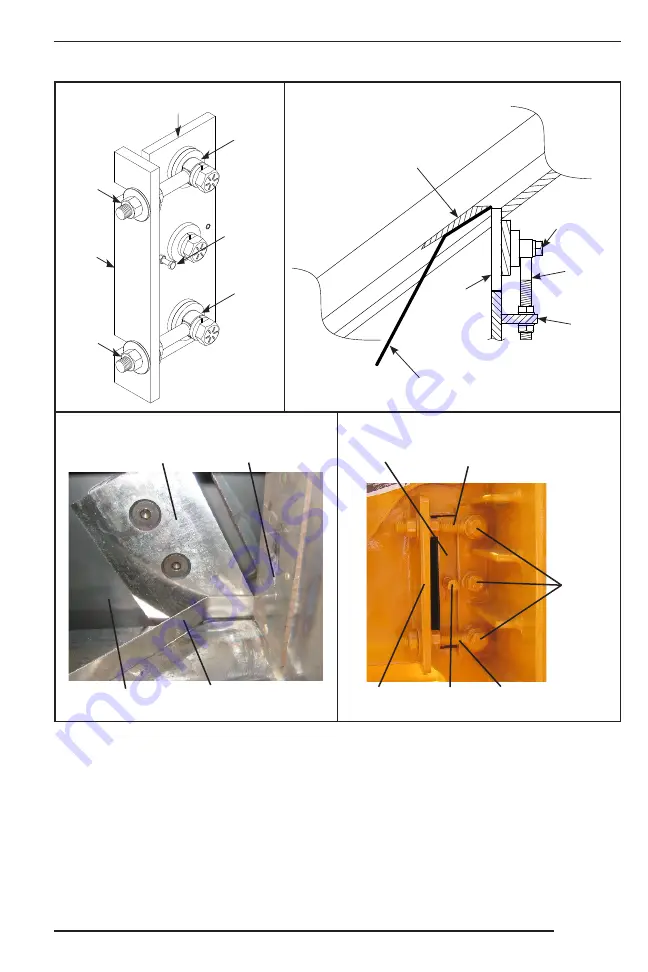
Bandit
35
MODEL 75
MAINTENANCE
ANVIL ADJUSTMENT
Anvil Bolts
Torque To
Specs
Knife
Disc
Anvil
Adjuster
Bolts
Anvil
Puller
Block
Anvil To
Knife Gauge
Anvil
Anvil
Anvil
Handle
Anvil
Adjuster
Bolt
Anvil
Puller
Block
Hex
Nut
Hex
Nut
Anvil
Adjuster
Bolt
View looking through the feedwheels at the
throat area
Anvil
Knife
Disc
Anvil To
Knife Gauge
View looking from the curb side of the
machine at the anvil area
Anvil Adjuster
Bolt
Anvil Puller
Block
Anvil Bolts
Torque To
Specs
Anvil Adjuster
Bolt
Anvil
Handle
Anvil
Summary of Contents for 75
Page 18: ......
Page 94: ...80 1 21 Model 75 Replacement Parts HYDRAULIC GASOLINE TANK ASSEMBLY 1 4 3 2 7 6 5 8 9 7...
Page 96: ...82 1 21 Model 75 Replacement Parts HYDRAULIC DIESEL FUEL TANK ASSEMBLY 2 7 6 3 2 1 4 8 4 9 5...
Page 102: ...88 1 21 Model 75 Service Record Service Record SERVICE RECORD DATE DESCRIPTION AMOUNT...