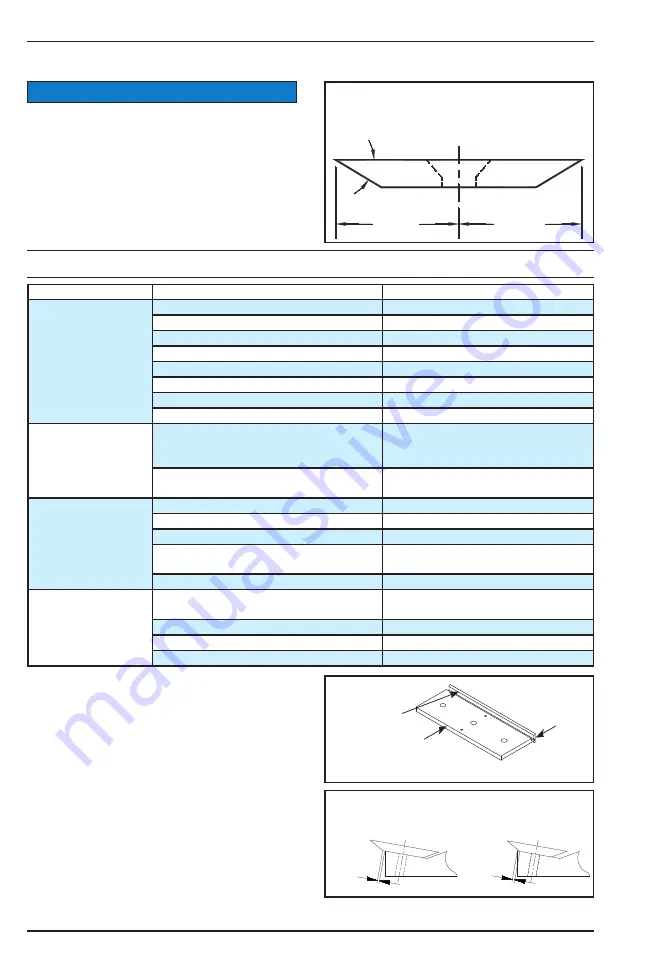
32
1/21
MODEL 200 UC
MAINTENANCE
1/2” x 4” x 7 1/4” Chipper Knives (Start 9/12)
(12.7 mm x 101.6 mm x 184.2 mm) &
3/8” x 4” x 7 1/4” Chipper Knives (Pre 5/12)
(9.5 mm x 101.6 mm x 184.2 mm)
1 13/16”
(46 mm)
Min.
1 13/16”
(46 mm)
Min.
31
°
TROUBLE SHOOTING CHIPPER PROBLEMS
Knives must be replaced in sets. These sets are
determined by the amount of resharpening done
to the knives. It must be reinstalled with another
knife of comparable usage. It helps to keep the disc
balanced, and it helps maintain chip quality.
Never allow these knives to wear or be
sharpened beyond absolute specified minimum
distance from the center line of bolt.
CHIPPER DISC
KNIFE SAVER KIT
Through various tests, Bandit has found that using
the Knife Saver will increase the life span of chipper
knives if used during the recommended times.
Each knife installed in every new machine at Bandit
has the Knife Saver used on it before leaving the
factory. The Knife Saver can be purchased from
your local Bandit dealer.
NOTICE
PROBLEM
POSSIBLE CAUSE
SOLUTION
Chipper makes
poor quality chips
or does not feed
properly.
Dull knives.
Sharpen or replace knives
Anvil worn or needs adjustment
Rotate, repair or replace
Feedwheels not operating correctly
See Hydraulic Troubleshooting
Throat/base wear
Repair with weld to original integrity.
Knives sharpened at wrong angle
Must be sharpened to 30° to 31° angle.
Feedwheel springs too loose
Adjust
Clutch / belts out of adjustment
Adjust
Engine not running at full RPMs
Adjust
Chipper knife hits
anvil.
Anvil clearance.
Adjust the anvil clearance to approx.
.045” to .065” (1.1 mm to 1.6 mm) from
the closest knife.
Chipper bearing bolts
Torque according to the torque chart
(see page 26)
Discharge Plugs
or Does Not Throw
Chips Properly.
Lugging engine on large material
Keep engine RPM up.
Dull knives or worn to minimum size.
Sharpen or replace.
Obstruction in discharge chute
Clear the obstruction.
Chipping rotting material with little
substance can plug the discharge chute. Feed alongside with good solid wood.
Worn fan blades.
Replace
Chipper Bearings
Running Too Hot
Improper lubrication
Purge chipper bearings once a day with
an EP-2 Type Lithium grease
Chipper disc operating at too high RPMs Do not exceed recommended RPMs
Bearings worn out
Replace.
Bearing locknut is loose.
Tighten.
• Use the Knife Saver on brand new knives.
• Use the Knife Saver on freshly resharpened
knives.
• Use the Knife Saver every day during the Daily
Maintenance while the knives are checked.
• Use the Knife Saver when the machine is shut
down for a break during the day.
See page 82 for knife saver part numbers
Fill working edge
with hard surface
weld as flat to
anvil surface as
possible. Use a
non-weldable bar
stock (Brass)
BRASS
BAR
ANVIL
Remove brass bar after building up area with hard surface weld
and square working corner with grinder.
Figure 1
UNDER NO SITUATION IS HEAL OF KNIFE
TO BE INSIDE EDGE OF MILLED POCKET!
YES
NO