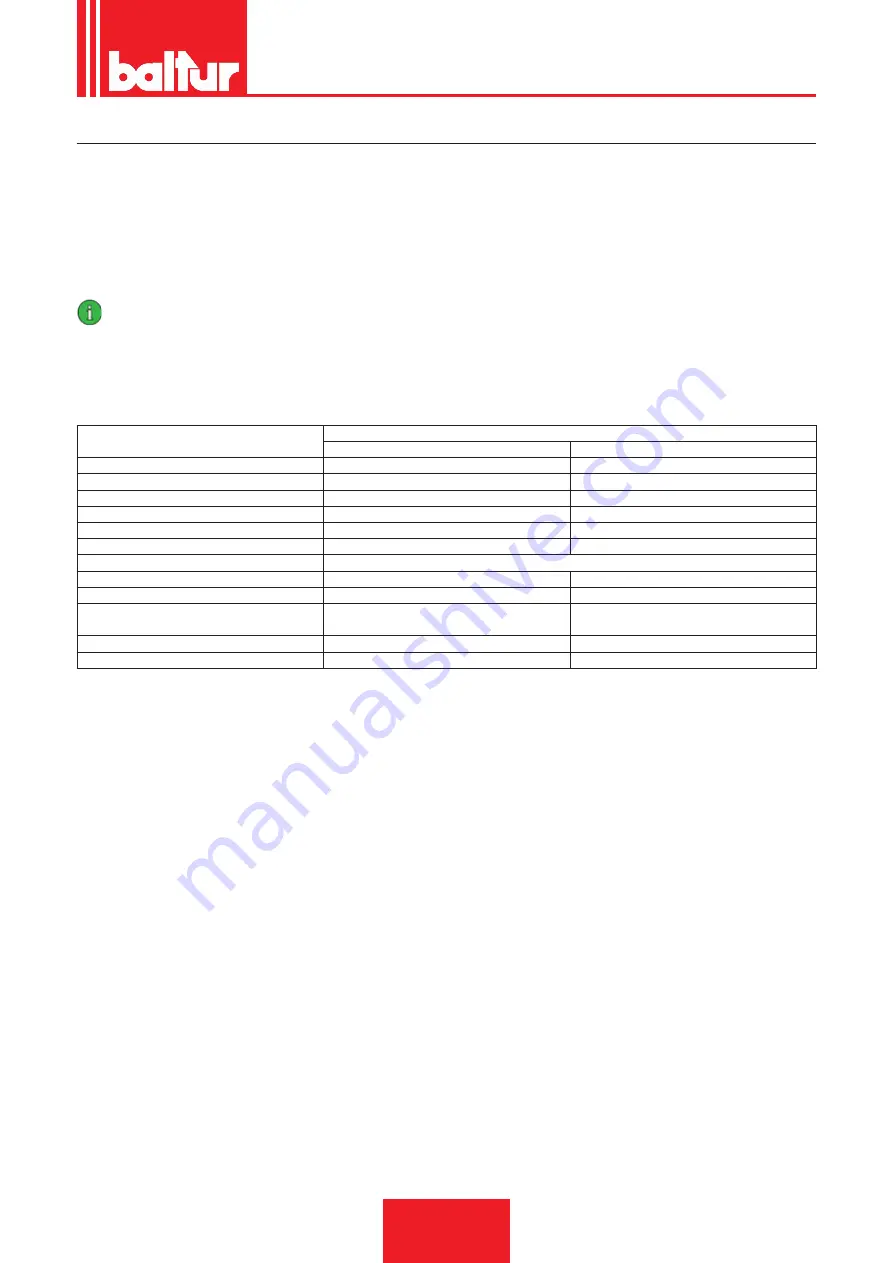
ENGLISH
21 / 28
0006081514_201711
EXPECTED LIFESPAN
The expected lifespan of burners and relevant components depends very much from the type of application on which the burner is installed, from
cycles of delivered power, from the conditions of the environment in which it is located, from maintenance frequency and mode, etc.
Standards about safety components provide for a project expected lifespan expressed in cycles and/or years of operation.
Such components ensure the correct operation in standard (*) operating conditions, with periodic maintenance according to the instructions
contained in the manual.
The table below shows the project expected lifespan of the main safety components; approximately, operating cycles correspond to the burner
activations.
When this expected lifespan limit has almost been reached the component must be replaced with an original spare part
.
IMPORTANT
warranty conditions (laid down in contracts and/or delivery or payment notes, if necessary) are independent and do not refer to the
expected lifespan stated below.
(*) “Normal” operating conditions means applications on water boilers and steam generators or industrial applications compliant with the standard
EN 746, in environments with temperatures within the limits provided for in this manual and with pollution degree 2 in compliance with annex M
of the standard EN 60335-1.
Safety component
Project expected lifespan
Operating cycles
Years of operation
Control box
250 000
10
Flame sensor (1)
N.A.
10,000 operating hours
Seal control
250 000
10
Gas pressure switch
50 000
10
Air pressure switch
250 000
10
Gas pressure regulator (1)
N.A.
15
Gas valves (with seal check)
Until the first seal fault signal
Gas valves (without seal check) ( 2)
250 000
10
Servomotors
250 000
10
Liquid fuel hoses
N.A.
5 (every year for fuel oil burners or in the presence
of biodiesel in diesel/kerosene)
Liquid fuel valves
250 000
10
Air fan impeller
50,000 activations
10
(1) The characteristics can degrade over time; during the annual maintenance the sensor must be checked and in case of flame signal degradation
must be replaced.
(2) Using normal mains gas.
Summary of Contents for TBG 600 ME
Page 2: ......
Page 25: ...ITALIANO 23 28 0006081514_201711 SCHEMI ELETTRICI TBG 480 2000 ME...
Page 26: ...ITALIANO 24 28 0006081514_201711 TBG 480 2000 ME...
Page 27: ...ITALIANO 25 28 0006081514_201711 TBG 480 2000 ME...
Page 28: ...ITALIANO 26 28 0006081514_201711 TBG 480 2000 ME...
Page 30: ......
Page 53: ...ENGLISH 23 28 0006081514_201711 WIRING DIAGRAMS TBG 480 2000 ME...
Page 54: ...ENGLISH 24 28 0006081514_201711 TBG 480 2000 ME...
Page 55: ...ENGLISH 25 28 0006081514_201711 TBG 480 2000 ME...
Page 56: ...ENGLISH 26 28 0006081514_201711 TBG 480 2000 ME...
Page 58: ......
Page 59: ......