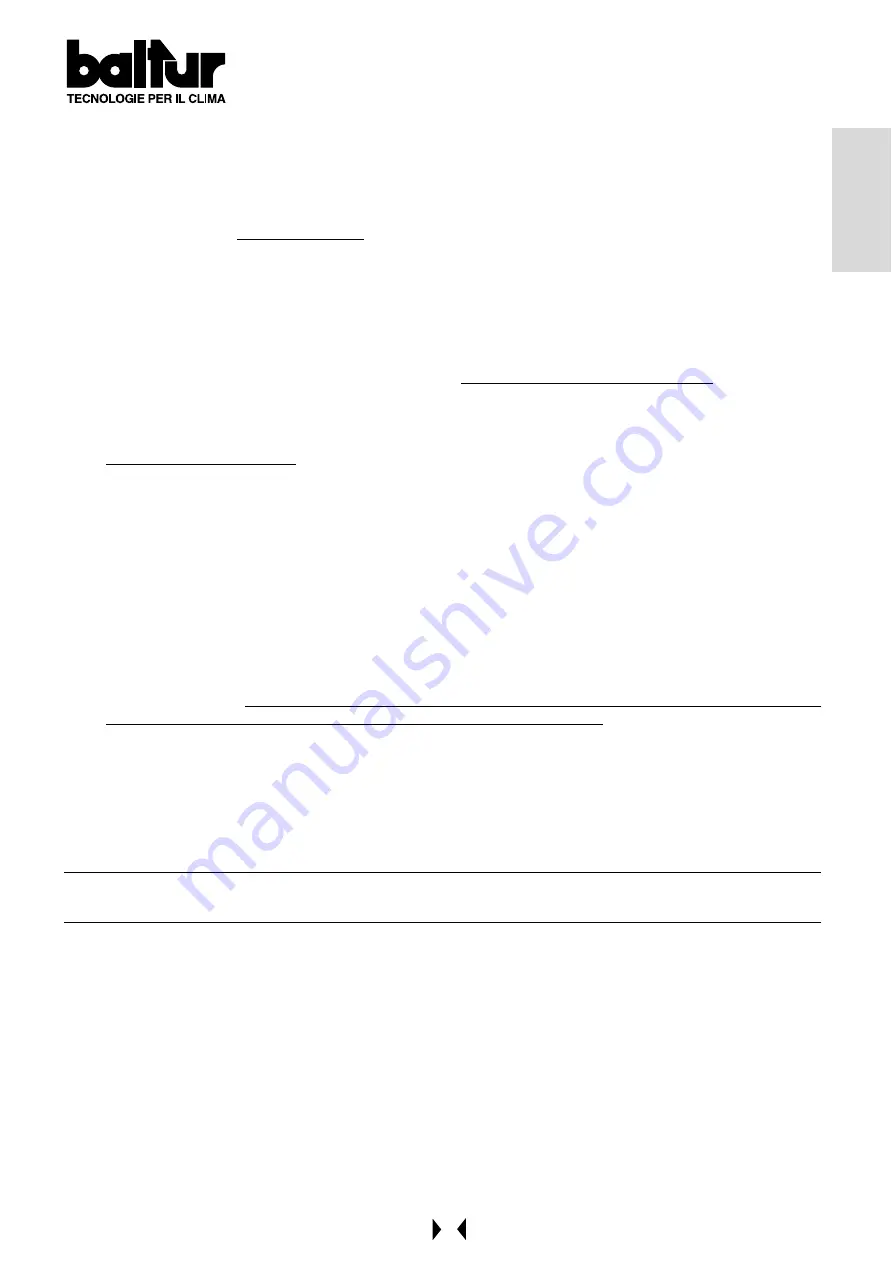
49
ENGLISH
less and the average efficiency of the latter is normally higher even if CO2 levels are slightly lower. Remember
that to achieve proper adjustment system water must be up to normal working temperature and that the burner
must have been working for at least fifteen minutes. In the absence of proper instrumentation use fume colour
as a guide. We recommend that adjustment be effected so as to obtain a light orange flame; avoid red flames
with smoke and white flames with an exaggerated excess of air.
20)
The purpose of the air pressure switch is to place the control box in lock-out (safety mode) if air pressure is
incorrect. The pressure switch must be adjusted so that it trips by closing the N.O. (Normally Open) contact
when air pressure in the burner reaches a sufficient value. The pressure switch connection circuit features
self-control so it is necessary that the N.C. (Normally Closed) contact (with fan at standstill and therefore no
air pressure in burner) actually brings about this condition. If it does not the control box is not switched on (the
burner stays off). More precisely, note that if the contact designed to be closed when working fails to close (air
pressure too low) then the control box goes through its cycle but the ignition transformer does not come on,
the pilot flame gas valves stay closed and the burner thus shuts down in “lock-out”. To check that the air
pressure switch is working properly it is necessary, with the burner at minimum flow rate to increase the
adjustment value until it trips: immediate burner “lock-out” must follow. Reset the burner by pressing the
appropriate button and adjust the pressure switch to a value sufficient to detect the air pressure during pre-
ventilation.
21)
The gas pressure switches (minimum and maximum) are designed to stop the burner working when gas
pressure is outside the set range.Given the specific function of the pressure switches it is evident that the
minimum pressure control switch must utilise the closed contact when the pressure switch detects a pressure
higher than that to which it is set. It is also evident that the maximum pressure switch must utilise the closed
contact when it detects a pressure lower than that to which it is set. Adjustment of minimum and maximum
gas pressure switches must therefore be effected during burner testing as a function of actual pressure at
each individual installation. The pressure switches are electrically connected in series; consequently, if any
one of the pressure switches trips (i.e. opening of the circuit) when the burner is working (flame lit) the burner
shuts down immediately. When testing the burner it is extremely important to check that pressure switches
are working properly. Proper pressure switch operation (opening of the circuit) must cause burner shutdown:
this can be checked for by acting on the relevant adjustment devices.
22)
Now check that modulation works properly in automatic mode. Turn the AUT - O - MAN switch to “AUT” and
the MIN - O - MAX switch to “O”. The modulation system is now on and under the exclusive automatic control
of the boiler probe. It is not normally necessary to act on the internal adjusters of the “RWF 40” power
regulator; however, the relevant instructions are contained in the pamphlet.
23)
Check that preheater thermostats are not adjusted in such a way as to cause anomalies (poor ignition, smoke,
formation of gas in the preheater etc.). Note that good atomisation can only be obtained when the heavy oil
arrives at the nozzle with viscosity no greater than 2 °E. Therefore adjust the “MS 30” electronic regulator or
regulation thermostat accordingly. For the minimum thermostat we advise a temperature setting approxi-
mately 20°C lower than the “MS 30” electronic regulator setting.
As a guideline consult the viscosity-temperature chart for the type of oil used.
ADJUSTING AIR ON THE COMBUSTION HEAD
(see drawing n° 0002933410)
The combustion head is fitted with an automatic device which regulates the passage of air between the disk and the
head. By throttling the passage it is possible to obtain high pressure upstream from the disk even for a low flow-rate.
Consequently, the high speed and turbulence of the air allows it to penetrate the fuel better, thus giving an optimum
mix and good flame stability. With a gas burner it may be indispensable to have high air pressure upstream from the
disk in order to avoid flame pulse. This condition is virtually a must when the burner has a pressurised combustion
chamber and/or a high heating load. It follows, then, that the device which closes off the air on the combustion head
must be adjusted in such a way as to always maintain decidedly high air pressure behind the disk.
We recommend that the air on the head be throttled to an extent that requires significant opening of the air damper
which regulates burner fan air flow. To do this act on the modulation disk adjuster screws.
When adjustment is over remember to lock the adjuster screws in place with the lock screws.
Summary of Contents for GI 1000 DSPN
Page 23: ...23 ITALIANO SCHEMA DI PRINCIPIO REGOLAZIONE ARIA PER MODELLO GI 1000 DSPN D N 0002933410 ...
Page 50: ...50 ENGLISH BURNER GI 1000 DSPN D AIR FEEDING ADJUSTMENT PRINCIPLA DIAGRAM N 0002933410 ...
Page 51: ...51 ENGLISH N 0002933930 BURNER GI 1000 DSPN D GAS PILOT ADJUSTMENT PRINCIPLE DIAGRAM ...
Page 67: ......
Page 68: ......
Page 69: ......
Page 70: ......
Page 71: ......
Page 72: ......
Page 73: ......
Page 74: ......
Page 75: ......