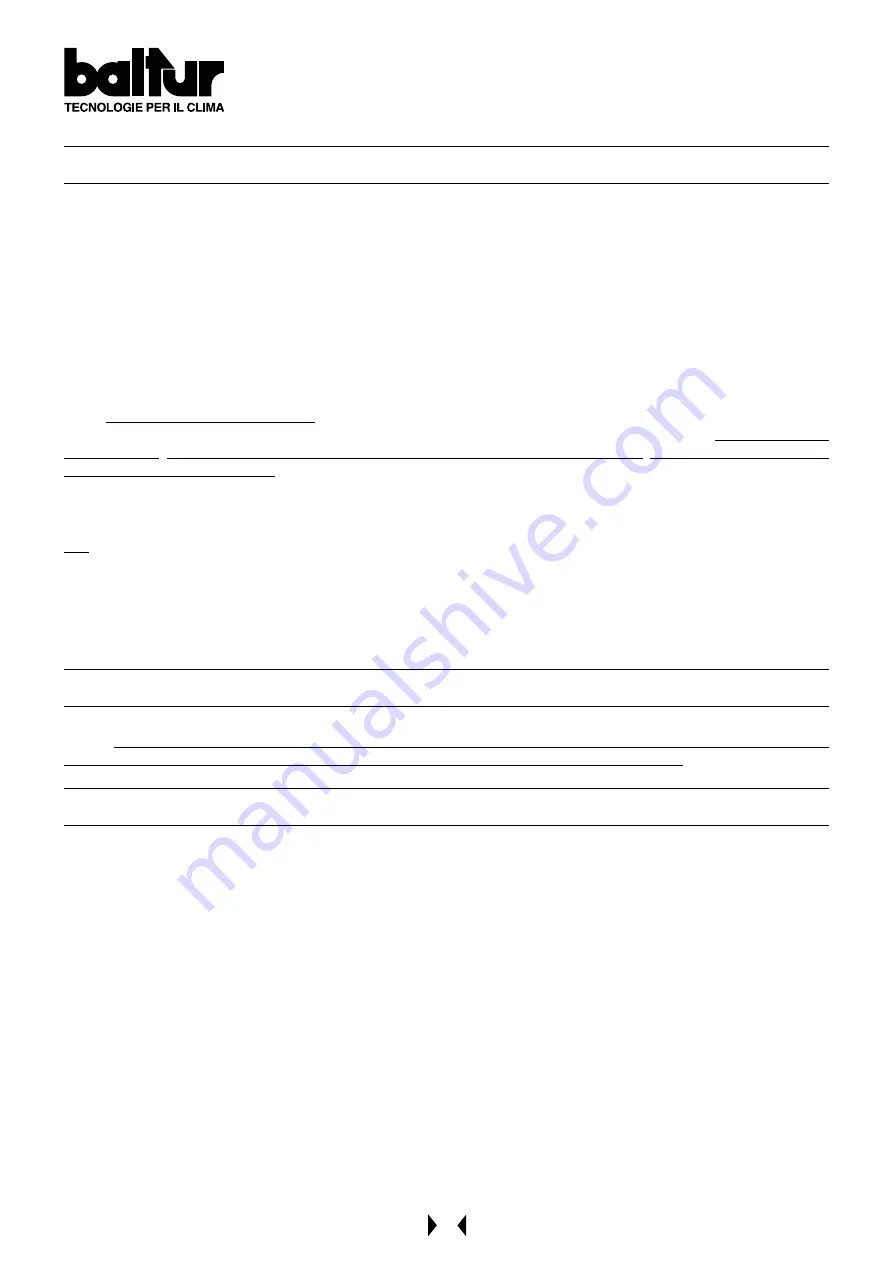
39
ADJUSTING THE AIR ON THE COMBUSTION HEAD
(see BT 8608/1)
The combustion head is equipped with a regulation device that restricts (moves forwards) or opens up (moves
backwards) the air flow between the diffuser disc and the head. Closing the passageway therefore generates high
pressure upstream from the diffuser disc even at low flow-rates Being at high speed and somewhat turbulent, the air
penetrates the fuel better, giving an excellent mix and good flame stability.
High air pressure upstream from the diffuser disc may be necessary to prevent flame pulsation; this condition is
practically essential when the burner is working on a pressurized chamber and/or at high thermal loads.
It is clear from the above description that the device which closes off the air in the combustion head must be brought
into a position which always gives decidedly higher air pressure behind the diffuser disc.
It is recommended that adjustment be carried out to provide on-head air closure that requires considerable opening
of the air gate which adjusts the burner fan intake flow; this condition must, of course, be obtained when the burner is
working at maximum desired fuel flow-rates. In practice adjustment must be begun with the on-head air closure device
in an intermediate position and by igniting the burner for approximate regulation as described previously.
When maximum desired fuel flow rates are reached correct the position of the device which closes off combustion head
air: do this by shifting forwards or backwards so that an air flow compatible with fuel flow is obtained with the air intake
flap wide open. When restricting air flow on the combustion head avoid complete closure. Check for perfect centering
with respect to the diffuser disc.
Please note that imperfect centering with respect to the diffuser disc may lead to poor combustion and excessive heating
of the head with consequent rapid deterioration. Check by looking through the spy-hole on the rear part of the burner
and then tightening (all the way) the screws that hold the combustion head air regulation device in position.
N.B. Check that ignition occurs properly:
if the regulator has shifted forwards the high speed of the outgoing air may make ignition difficult.
Should such a situation occur shift the regulator back a little at a time until it is in a position that gives regular ignition
and take this as the definitive setting.
It should be pointed out, once again, that for the 1st stage it is preferable to limit the air quantity to an indispensable
minimum so as to ensure secure ignition even under the most difficult conditions.
ADJUSTING THE DISTANCE BETWEEN THE DIFFUSER DISC AND THE NOZZLE
The burners are equipped with a device that allows adjustment of the distance between the diffuser disc and the
nozzle. The distance between diffuser disc and nozzle is set by the manufacturer and must only be reduced if it is noted
that the atomized fuel cone exiting the nozzle wets the diffuser disc and consequently stains it.
CHECKS
Once the burner is operating check the safety devices (photoresistance, shutdown, thermostats).
1) The photoresistance is the flame control device. It must therefore cut in if, during operation, the flame goes out
(carry out this check at least 1 minute after flame ignition).
2) The burner must shut itself down and stay off when, during ignition and within the control set time, the flame fails to
appear. Shutdown immediately cuts fuel flow, stops the motor and therefore the burner and causes the shutdown
warning light to come on. To check photoresistance efficiency proceed as follows:
a) start the burner.
b) at least 1 minute after ignition extract the photoresistance by removing it from its housing and simulate a
“no flame” situation by covering the photoresistance (obscure the photoresistance support window with a rag).
The flame should go out (with control box LAL 1.25 the burner shuts down).
c) If, with control box OR 3/B, the photoresistance is kept in the dark the burner re-ignites but the photoresistance
does not “see” the light and the burner shuts down in a time determined by program settings. The burner can only
be reset by pressing the appropriate push-button.
3) To check thermostat efficiency run the burner until the water in the boiler reaches a temperature of at least 50° C and
then act on the thermostat control knob, lowering the temperature setting until the “click” of the opening switch is
heard and simultaneous burner shutdown is observed. The thermostat must trip within a maximum “lag” of 5 - 10°
C with respect to the control thermostat (boiler thermometer). If this is not so modify the thermostat scale calibration
so that it corresponds with thermometer settings.