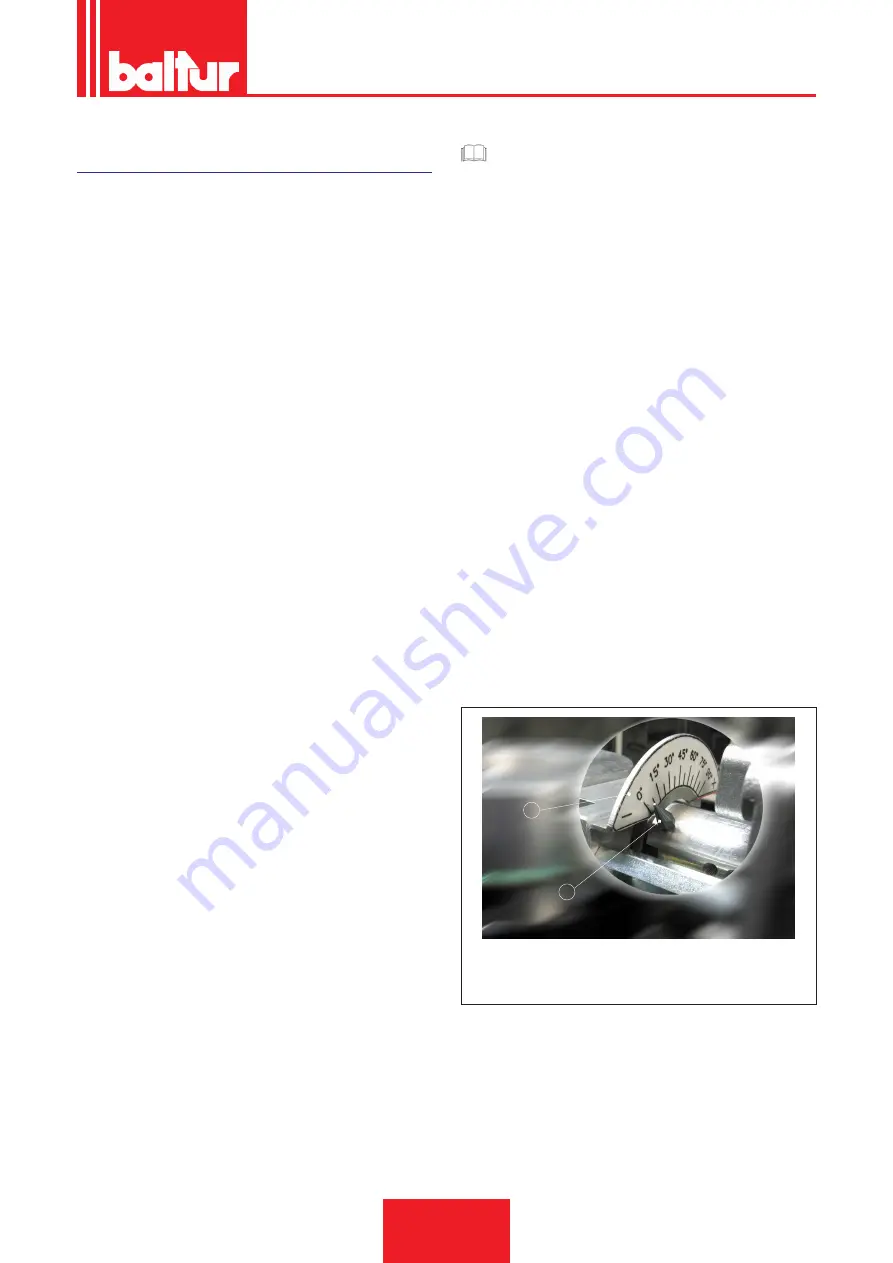
ENGLISH
19 / 38
0006160050_201708
DESCRIPTION OF PROGRESSIVE TWO-
STAGE OPERATION
Blown air burners with electronic modulation may be used on
hearths under strong pressure or in a vacuum, according to the
corresponding operating curves.
They combine a very stable flame with total safety and high
performance.
The burner is fitted with an electronic cam controlled by a
microprocessor for intermittent operation, and for the control and
monitoring of the blown air gas burners. Electronic modulation
achieved by means of two step air gas regulation motors.
The burner is fitted with a valve tightness control device. To better
understand the operation of the electronic cam, read the specific
instructions in the manual provided carefully.
The term two-stage progressive operation indicates that transition
from the first to the second state (from minimum to maximum
operation) is progressive in terms of both amount of combustion
air let in and the amount of output fuel. This results in a greater
pressure stability in the gas supply network.
Ignition is preceded by the combustion chamber pre-ventilation
as set forth by the Standards, with air open and with a duration of
approx. 30 seconds.
If the air pressure switch has detected a sufficient pressure, the
ignition transformer activates at the end of the ventilation phase
and after 3 seconds the safety and main valves open in sequence.
Gas reaches the combustion head, mixes with air supplied by the
fan and is ignited. The gas supply is regulated by the butterfly gas
valve.
Three seconds after the valves (main and safety) come on, the
ignition transformer goes off. Thus the burner is ignited at the
ignition point.
The presence of the flame is detected by the control device
(ionization probe immersed in the flame) .
The programmer relay moves past the locking position and sends
voltage to the (air / gas) supply regulation servo motors, which go
to the minimum point (200).
If the second stage boiler thermostat (or pressure switch) allows
it (set to a temperature or pressure value higher than the existing
value in the boiler), the (air / gas) supply servo motors will start to
turn, gradually increasing gas and combustion air supplies up to
the maximum supply to which the burner has been set (999).
CAUTION / WARNING
The electronic cam controls the burner, activating the
combustion air, gas servomotor and the fan motor, if the
inverter is fitted, according to a curve that has ten points set
(see curve regulation table).
The burner remains in the maximum output position as long as
the temperature or pressure reaches a value sufficient enough
to cause the intervention of the probe that rotates the gas/air flow
rate regulation servomotors. This progressively reduces the gas,
combustion air and motor's RPM (if the inverter is fitted) to the
minimum.
If the threshold value (temperature or pressure), to which the
complete shut-down device (thermostat or pressure switch) is set,
is reached even with minimum gas and air output, the burner will
be shut down when the device is triggered.
As the temperature or pressure drops below the shut-down
device's (thermostat or pressure switch) set point, the burner will
be turned on again as described above.
During normal operation, the modulation probe installed on the
boiler measures any variation demands and automatically adjusts
the fuel and combustion air flow rate by starting the air/gas flow
rate modulation servomotors, modulating the output.
This causes the air/gas output control system to balance the
amount of heat supplied to the boiler with the amount it gives off
during use.
If the flame does not appear within 3 seconds after the gas valves
have opened, the control box goes into the lock-out condition (the
burner shuts down completely and the warning light turns on).
To “reset” the control box operation, press the reset button.
DETAIL OF BUTTERFLY VALVE FOR GAS FLOW
REGULATION BY MEANS OF SERVO MOTOR
A
B
A) Butterfly gas valve position reference index
B) Gas modulation servomotor
Summary of Contents for BGN 300 LX
Page 2: ......
Page 29: ...ITALIANO 27 38 0006160050_201708 SCHEMI ELETTRICI...
Page 30: ...ITALIANO 28 38 0006160050_201708...
Page 31: ...ITALIANO 29 38 0006160050_201708 BT1 BA BP I1 I2 I3 I4...
Page 33: ...ITALIANO 31 38 0006160050_201708 SCHEMI ELETTRICI...
Page 34: ...ITALIANO 32 38 0006160050_201708...
Page 35: ...ITALIANO 33 38 0006160050_201708 D...
Page 36: ...ITALIANO 34 38 0006160050_201708 BT1 BA BP I1 I2 I3 I4...
Page 37: ...ITALIANO 35 38 0006160050_201708...
Page 38: ...ITALIANO 36 38 0006160050_201708 E E...
Page 40: ...ITALIANO 38 38 0006160050_201708...
Page 67: ...ENGLISH 27 38 0006160050_201708 WIRING DIAGRAMS...
Page 68: ...ENGLISH 28 38 0006160050_201708...
Page 69: ...ENGLISH 29 38 0006160050_201708 BT1 BA BP I1 I2 I3 I4...
Page 71: ...ENGLISH 31 38 0006160050_201708 WIRING DIAGRAMS...
Page 72: ...ENGLISH 32 38 0006160050_201708...
Page 73: ...ENGLISH 33 38 0006160050_201708 D...
Page 74: ...ENGLISH 34 38 0006160050_201708 BT1 BA BP I1 I2 I3 I4...
Page 75: ...ENGLISH 35 38 0006160050_201708...
Page 76: ...ENGLISH 36 38 0006160050_201708 E E...
Page 78: ...ENGLISH 38 38 0006160050_201708...
Page 79: ......