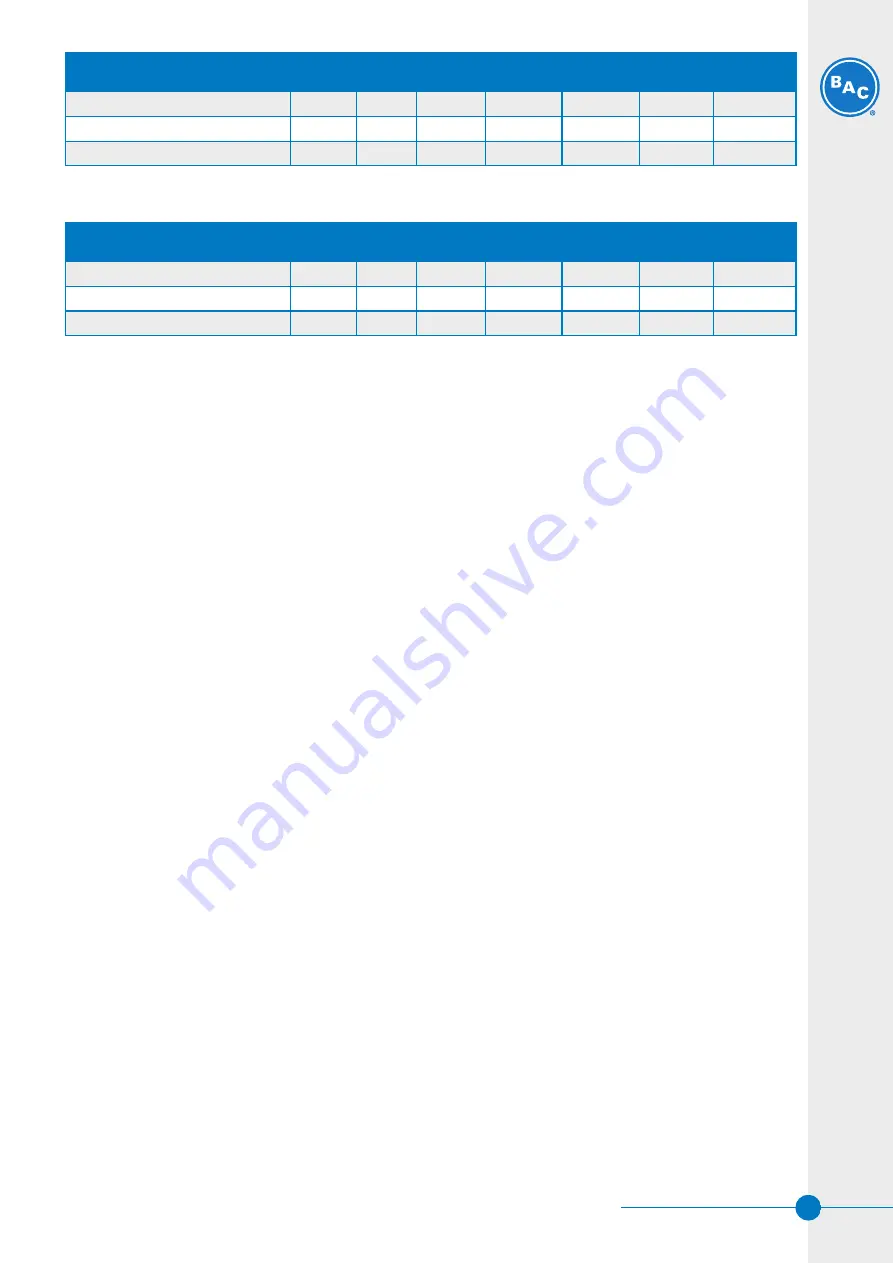
Lubrication
Start-Up
Weekly
Monthly
Quarterly
Every 6
months
Annually
Shutdown
Fan shaft bearings
X
X
X
Motor bearings*
X
X
Adjustable motor base
X
X
X
* only for motors with grease fittings with typical frame size > 200L (>30 KW)
Cleaning procedures
Start-Up
Weekly
Monthly
Quarterly
Every 6
months
Annually
Shutdown
Mechanical cleaning
X
X
X
Disinfection**
(X)
(X)
(X)
Drain basin
X
** depends on applied code of practice
Notes
1. Water treatment and auxiliary equipment integrated in the cooling system may require additions to the table
above. Contact suppliers for recommended actions and their required frequency.
2. Recommended service intervals are for typical installations. Different environmental conditions may dictate
more frequent servicing.
3. When operating in ambient temperatures below freezing, the unit should be inspected more frequently (see
Cold weather operations in the appropriate Operating and Maintenance Instructions).
4. For units with belt drive, tension on new belts must be readjusted after the first 24 hours of operation and
monthly thereafter.
W W W . B A L T I M O R E A I R C O I L . E U
3