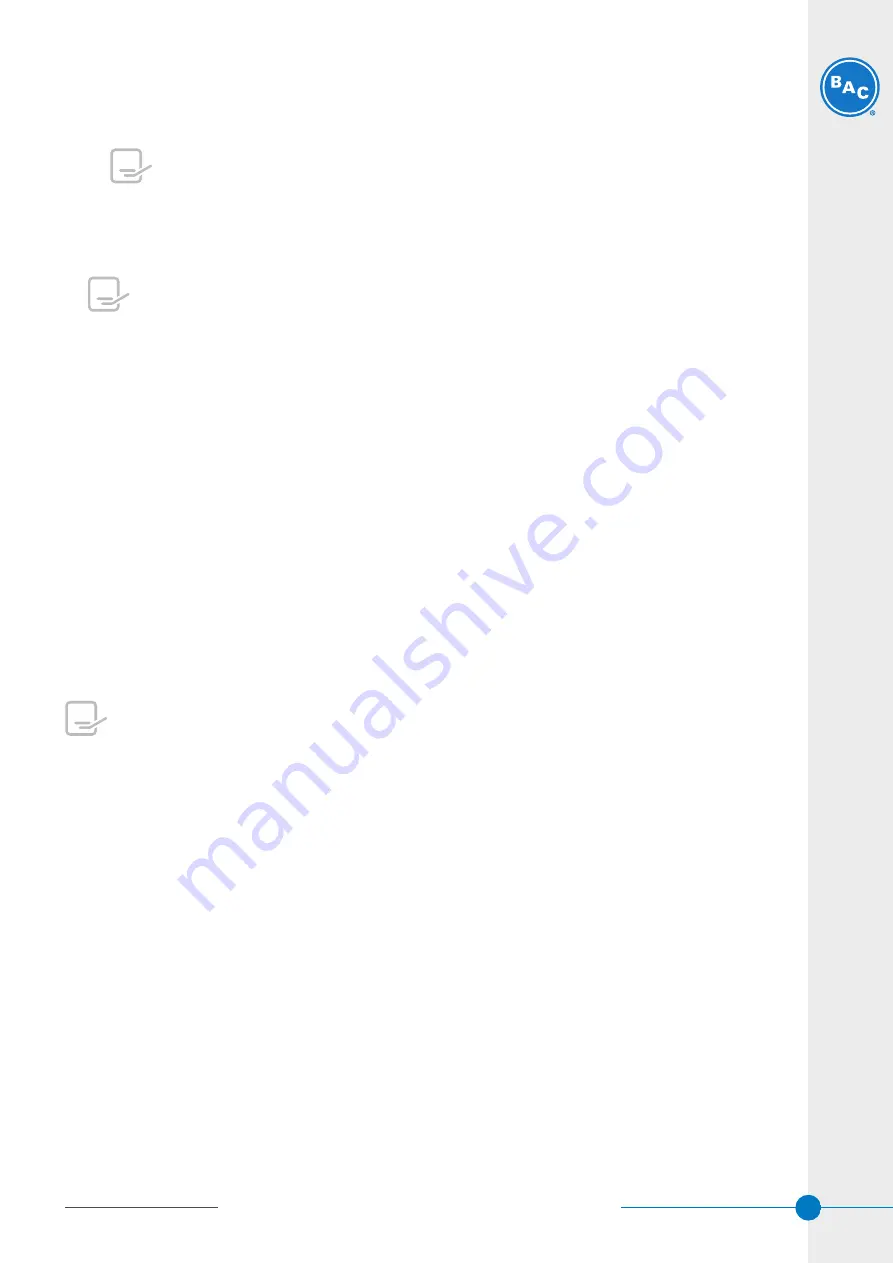
6. After the first three hours of ice build, it is suitable to turn off the air agitation blower(s).
7. In response to a signal from the plant control system, stop the ice build cycle. The signal to end the ice build
cycle can come from a number of sources. Typical examples follow:
-
The ice thickness control
The ice thickness control is a safety control and must override all other controls to prevent damage
to the coils.
-
A control system time clock.
-
A kW counter that indicates a stored input equal to the preceding day's melted output.
8. Turn off the glycol chiller(s) and glycol pump(s) and close the inlet valves to the Ice Chiller
®
Coils.
If both inlet and outlet glycol valves are used on the Ice Chiller
®
Coils, the design must allow for a
bypass relief around the valves. This will prevent an excess build-up of pressure in the coils as a result
of the expansion as glycol in the coils warms up.
9. The Ice Chiller
®
Coils are now charged and available to provide cooling.
ICE MELT
1. Begin the ice melt cycle upon receiving a signal from the plant control system. Usually, this signal is triggered
by a cooling load to be handled by the stored ice.
2. Open any chilled water inlet and outlet valves installed at the ice storage tank.
3. Turn on the air agitation blower(s) feeding the ice storage tank.
4. Turn on the circulating chilled water pump(s) to establish flow between the ice storage tank and the cooling
load.
5. Upon receiving a signal from the plant control system to stop the ice melt cycle, turn off the chilled water pump
(s) and the air agitation blower(s), and close the chilled water inlet and outlet valves to ice storage tank.
6. The signal to end the melt cycle can come from a number of sources. Typical examples follow:
-
A time clock.
-
A signal that the cooling load has been satisfied.
-
A kW counter that indicates the maximum cooling for the day has been drawn from the storage tank.
7. The Ice Chiller
®
Coils are now ready to be recharged following the ice build procedures above.
Full melt-out after every cycle results in minimum energy consumption.
When the required melt performance cannot be obtained due to significant horizontal ice bridging, melt the ice
completely during the next cycle. Full melt-out can be detected by 0% ice display on the Ice Logic™ Ice Thickness
Controller combined with a rapidly increasing water leaving temperature.
To minimize the possibility for ice bridging, operating according to the following guidelines:
•
Limit the cooling load through the TSU-C/D during ice build to less than 15% of the installed compressor
capacity.
•
Maintain a constant high water flow on the TSU-C/D during melt-out. The corresponding temperature difference
between entering and leaving water should be kept as low as possible to minimize conical met-out pattern
(10°C maximum).
•
Try to melt out the TSU-C/D completely at the end of each cooling cycle by limiting the amount of ice build to
the expected cooling load. For multiplier TSU-C/D installations, a melt-out in sequence assures at least one full
melt-out at regular intervals. Full melt can be detected by 0% ice display on the Ice Logic™ Ice Thickness
Controller combined with a rapidly increasing leaving water temperature.
•
To increase control flexibility, use 1 additional Ice Logic™ Ice Quantity Controller on a 4 coil unit (available as
an option).
W W W . B A L T I M O R E A I R C O I L . E U
11
3 Operating instructions
3 Operating instructions
Summary of Contents for ICE CHILLER TSC-C-D
Page 24: ...W W W B A L T I M O R E A I R C O I L E U 24...
Page 25: ...W W W B A L T I M O R E A I R C O I L E U...
Page 26: ...W W W B A L T I M O R E A I R C O I L E U...
Page 27: ...W W W B A L T I M O R E A I R C O I L E U...
Page 28: ...W W W B A L T I M O R E A I R C O I L E U...