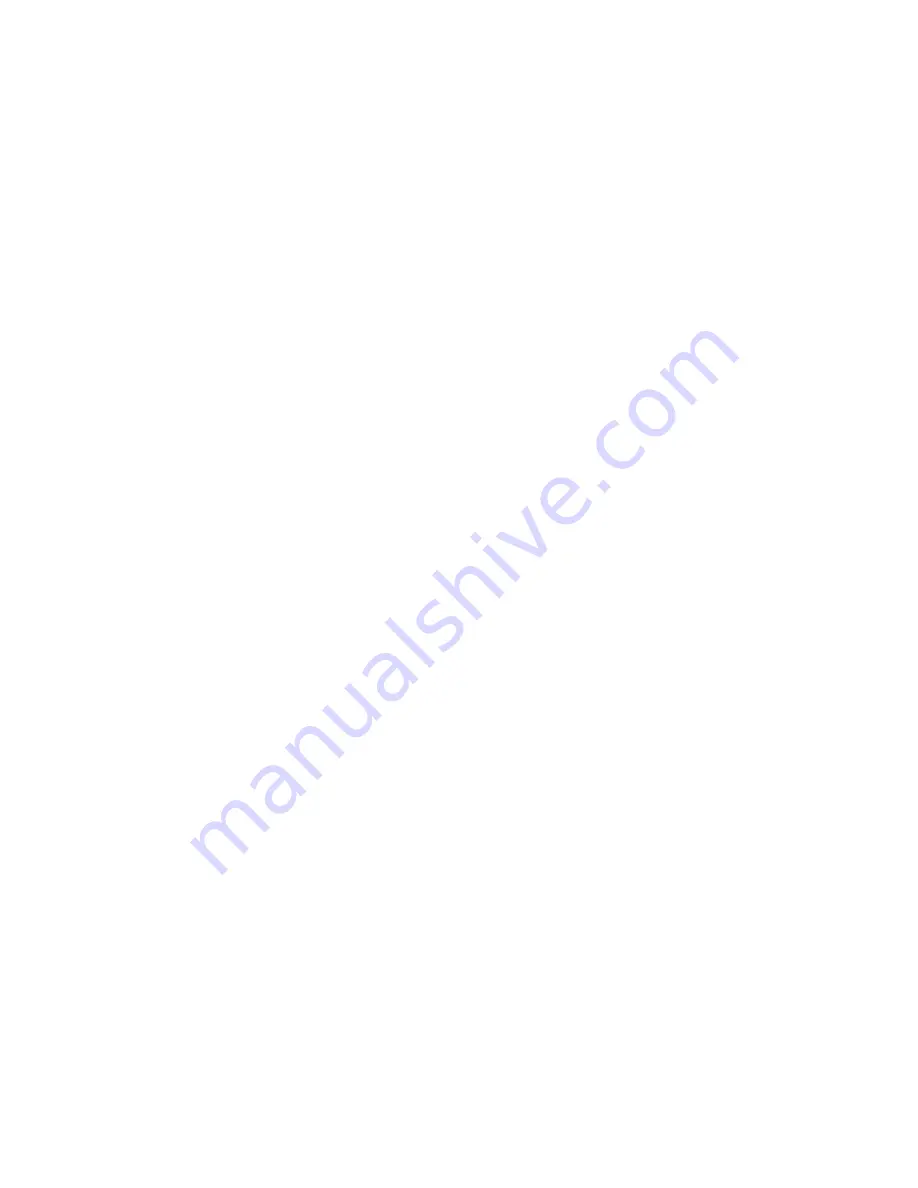
13.7.3 Screw off the nut of the pipe of the flame igniter 13 from the valve block 14.
13.7.4 Unscrew two screws fixing the valve block 14 to the body frame of the gas unit 15 and remove the block.
13.7.5 Install a new valve block and check the joints subject to disassembling on air-tightness, see p. 7.4.6.
13.7.6
Check the appliance’s working capacity with the new valve block.
13.8
Replaceme
nt of the water and gas unit’s water unit
13.8.1 Remove the casing, see p. 13.1.
13.8.2 Unscrew two captive nuts from the water inlet and outlet fittings of the water unit 17.
13.8.3 Unscrew two screws fixing the water unit 17 to the body frame of the gas unit15 and remove it.
13.8.4 Install a new water unit.
13.8.5 Check the joints subject to disassembling on air-tightness, see p. 7.3.7. Water leakage is unacceptable.
13.8.6
Check the appliance’s operation with the new water unit.
13.9
Replacement of the water unit membrane (membrane assembled with the plate)
13.9.1 Effectuate the works listed in pp. 13.8.1-13.8.3.
13.9.2 Unscrew six screws fixing the cover of the water unit 17 with the body frame, replace the membrane that is out of order (the membrane with a plate) for a
new one.
13.9.3 Assemble the water unit.
13.9.4 Effectuate the works listed in pp 13.8.4-13.8.6.
13.10 Replacement of the thermo relay (water overheating sensor)
13.10.1 Remove the casing, see p. 13.1.
13.10.2 Disconnect two cables from the thermo relay 22 on the hot water outlet pipe (Scheme 17)
13.10.3 Unscrew two screws connecting the thermo relay 22 with the loop 8 and remove the thermo relay.
13.10.4 Install a new thermo relay.
13.10.5
Check the appliance’s operation with the new thermo relay.
13.11 Replacement of the pipe of cold water supply to the heat exchanger
13.11.1 Remove the casing, see p. 13.1.
13.11.2 Unscrew a captive nut from the fitting of the water unit 17.
13.11.3 Unscrew a captive nut from the fitting of the pipe of the heat exchanger 2 and remove the pipe 5 together with the gaskets.
13.11.4 Install a new pipe with new gaskets.
Summary of Contents for NEVALUX-5514
Page 18: ......