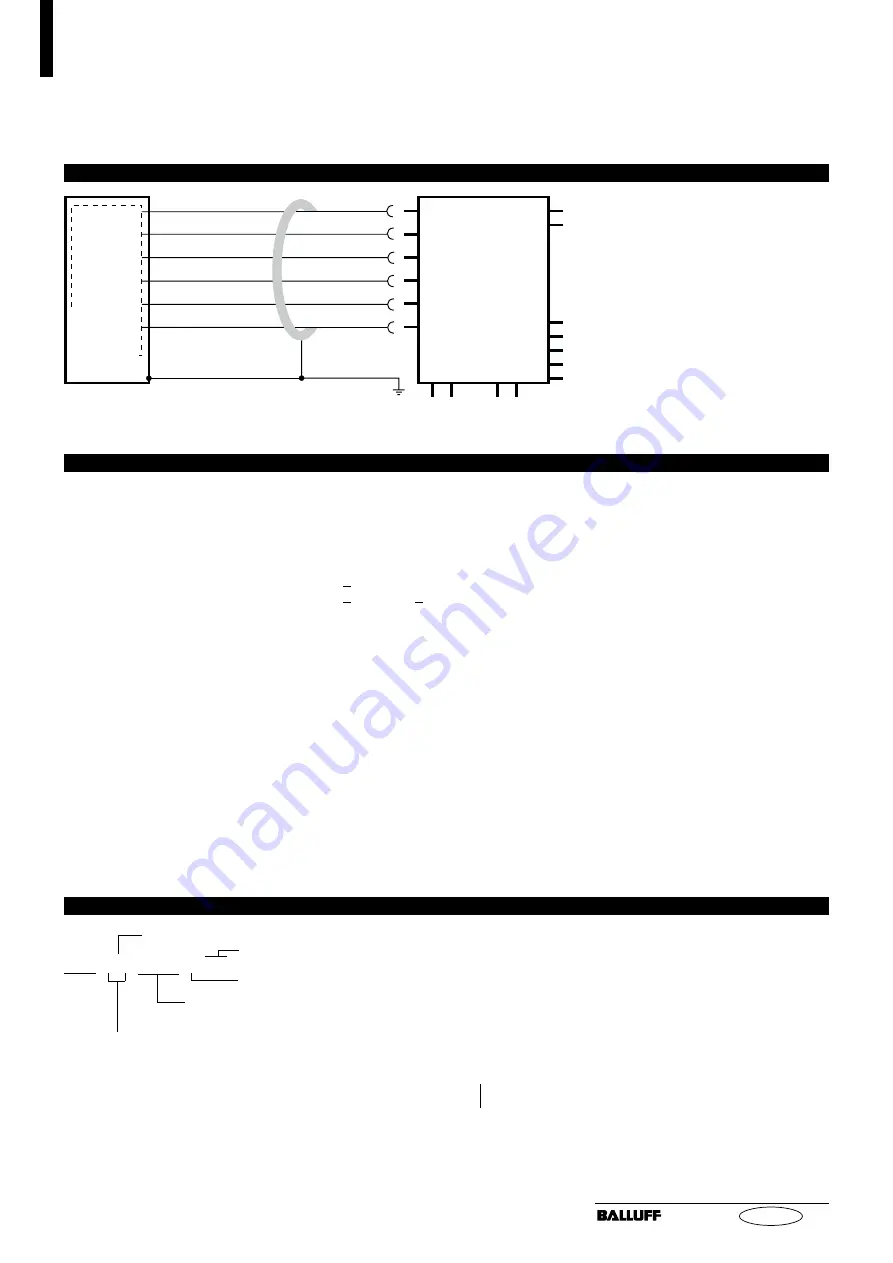
BTL5-A/C/E/G_ _-M/U_ _ _ _-P-S 32/KA_ _
Micropulse Linear Transducer in Profile Housing
7
english
5
Startup
5.1
Check connections
Although the connections are polar-
ity reversal protected, components
can be damaged by improper con-
nections and overvoltage. Before
you apply power, check the connec-
tions carefully.
5.2
Turning on the system
Note that the system may execute
uncontrolled movements when first
turned on or when the transducer is
part of a closed-loop system whose
parameters have not yet been set.
Therefore make sure that no haz-
ards could result from these situa-
tions.
If there is no magnet in the stroke
range, the integrated function moni-
tor provides the following defined
output signals:
6
Versions (indicated on part label)
Supply voltage 1 = DC 24 V, 2 = DC ±15 V
Electr. connection S32: with connector,
BTL5-A11-M0450-P-S32
KA05: with 5 m cable
Profile form factor
Nom. length (4 digits), M = metric in mm
U
= inches in 1/10 inch
Analog interface:
Voltage output
A_1 = 10 ... 0 V and 0 ... 10 V
G_1 = 10 ... –10 V and –10 ... 10 V
Current output
C_0 = 0 ... 20 mA
E_0 = 4 ... 20 mA
C_7 = 20 ... 0 mA
E_7 = 20 ... 4 mA
Micropulse
Linear T
ransducer
Voltage output 10 V
increasing
decreasing
U
A
> 10 V
< 0 V
Current output 20 mA
increasing
decreasing
I
A
> 20 mA
0 mA for BTL5-C...
I
A
> 20 mA
< 4 mA for BTL5-E...
5.3
Check output values
After replacing or repairing a trans-
ducer, it is advisable to verify the
values for the start and end position
of the magnet in manual mode. If
values other* than those present
before the replacement or repair are
found, a correction should be made.
* Transducers are subject to modifi-
cation or manufacturing tolerances.
5.4
Check functionality
The functionality of the transducer
system and all its associated com-
ponents should be regularly
checked and recorded.
5.5
Fault conditions
When there is evidence that the
transducer system is not operating
properly, it should be taken out of
service and guarded against unau-
thorized use.
5.6
Noise elimination
Any difference in potential - current
flow - through the cable shield
should be avoided. Therefore:
–
Use the isolation bushings, and
–
Make sure the control cabinet
and the system in which the
BTL5 is contained are at the
same ground potential.
4
Wiring (cont.)
YE
GY
PK
GN
BU
BN
4...20 mA
0 V
10...0 V
0...10 V
GND
+24 V
Fig. 4-3: BTL5-E10...KA _ _ with processor card/controller, wiring example
p
rocessor/
contr
oller with
analog input
BTL5-E10...KA_ _