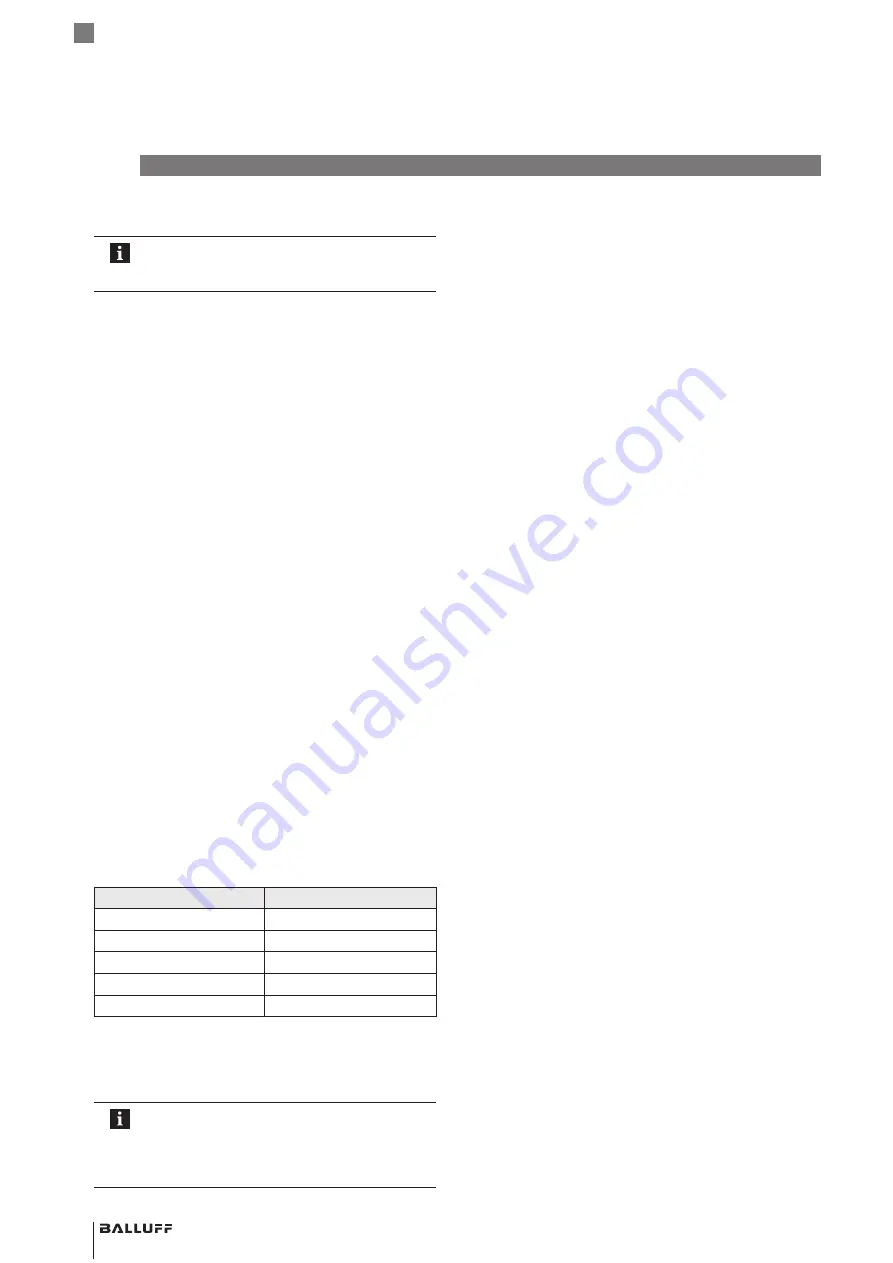
10
english
4
Installation and connection (continued)
4.4
Shielding and cable routing
Defined ground!
The BTL and the control cabinet must be at the
same ground potential.
Shielding
To ensure electromagnetic compatibility (EMC), observe
the following:
– Connect BTL and controller using a shielded cable.
Shielding: Braided copper shield with minimum 85%
coverage.
– Shield is internally connected to connector housing.
Magnetic fields
The position measuring system is a magnetostrictive
system. Ensure that there is sufficient distance between
the BTL and the strong, external magnetic fields.
Cable routing
The Profibus bus line must be routed according to
Techni-
cal Guideline 2.111, Installation Guidelines for Profibus-DP/
FMS
.
Do not route the cable between the BTL, controller, and
power supply near high voltage cables (inductive stray
noise is possible).
The cable must be routed tension-free.
Inductive stray noise from AC harmonics (e.g. from phase
angle controls) are especially critical and the cable shield
offers very little protection against this.
The signal is transmitted to the controller via the Profibus
DP interface.
Cable twisted in pairs, shielded.
Maximum length of the entire field bus cable: 1200 m
The transfer rate depends on the length of the cable. In
accordance with EN 50170, the values named in Tab. 4-3
apply.
Cable length
Baud rate [kbit/s]
< 100 m
12000
< 200 m
1500
< 400 m
500
< 1000 m
187.5
< 1200 m
93.7/19.2/9.6
Tab. 4-3: Baud rate depending on cable length
The bus must be terminated at both ends in accordance
with EN 50170 (see Fig. 4-10).
The BTL can be assigned a station address via
DIP switches. In addition, the BTL can internally
terminate the bus via DIP switches. For further
information see chapter Presettings on
page 12.
Noise elimination
To avoid equipotential bonding (current flow) through the
cable shield, please note the following:
– Use insulating bushes.
– Put the control cabinet and the system in which the
BTL is located to the same ground potential.
BTL5-T1 _ _ -M _ _ _ _ -P-S103
Magnetostrictive Linear Position Sensor – Profile Style