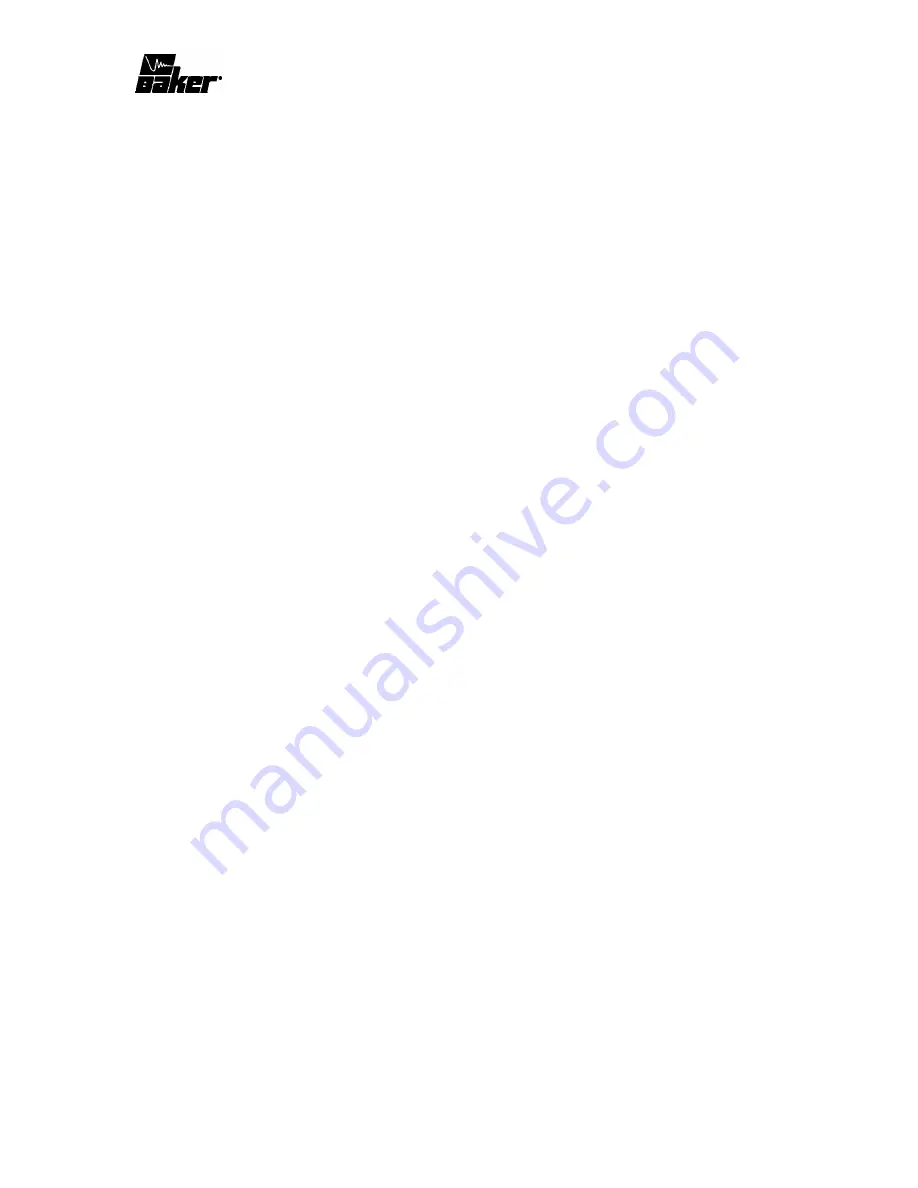
17
Baker Instrument Company
The Measure of Quality
12.
Access the Discharge board by removing the Stack board and check resistance
measurements of the following components and replace if necessary. Ensure that
power is disconnected when making these measurements and disassembling the unit.
Check R1 through R14.
13.
If the signal in step 11 was noted proceed to check that relay K1 on the I/O board has
no contact resistance between pins 2 and 3. If pin 7 of the relay is at a low state and
contact resistance is detected, replace relay K1. If pin 7 is at approxi12 volts
DC, then check U6 pin for +5 volts DC, then replace Q1 on the I/O board. If U6 pin
6 is at a low state, replace U6.
14.
Replace U19, U20 and U14 on the A/D board.
V
OLTAGE DROPS WHEN
PTT
BUTTON
RELEASED
In all digital models previous to serial number 210, an intermittent problem was detected
in that when an operator of the test was to attain the desired test voltage and release the
PTT button, the displayed voltage would drop approximately 10%. To correct this
problem the addition of K1 and K2 chassis relays were added. In older revisions the AC
line voltage was switched directly from the PTT button or the footswitch to the T2 variac.
The Zero Start Interlock board would switch the voltage from T2 pin 3 to the primary of
the high voltage transformer. To engage the Zero Interlock, the following needs to occur
at the Zero Start Interlock board.
1.
AC line voltage is connected through the footswitch or PTT button to J1 pin 1.
2.
+13 volts DC is supplied to J2 pin 5 supplied from the I/O board J1 pin 2B.
3.
/PTT signal at J2 pin 2 needs to switch from +5.6 volts DC to .4 volts DC when the
PTT button is depressed.
4.
The output control variac needs to be adjusted completely counter-clockwise.
After Serial number 210 Baker has changed from revision D to a revision F chassis
wiring diagram. Major changes incorporate using a +12 volt DC supply wired through
the footswitch and the PTT button. Also K1 and K2 were added. These relays hold the
displayed test voltage slightly longer so that the A/D memory has enough time to capture
the displayed test voltage. Relay K2 can be fitted to mount o the side of the card cage
above the Zero Start Interlock board and K1 can be mounted on the chassis next to the
Zero Start Interlock board. Mount by drilling two mounting holes and securing with
mounting hardware. Wiring additions or changes involve the following. To perform this
modification removal from the case is required. Remove mounting hardware on the