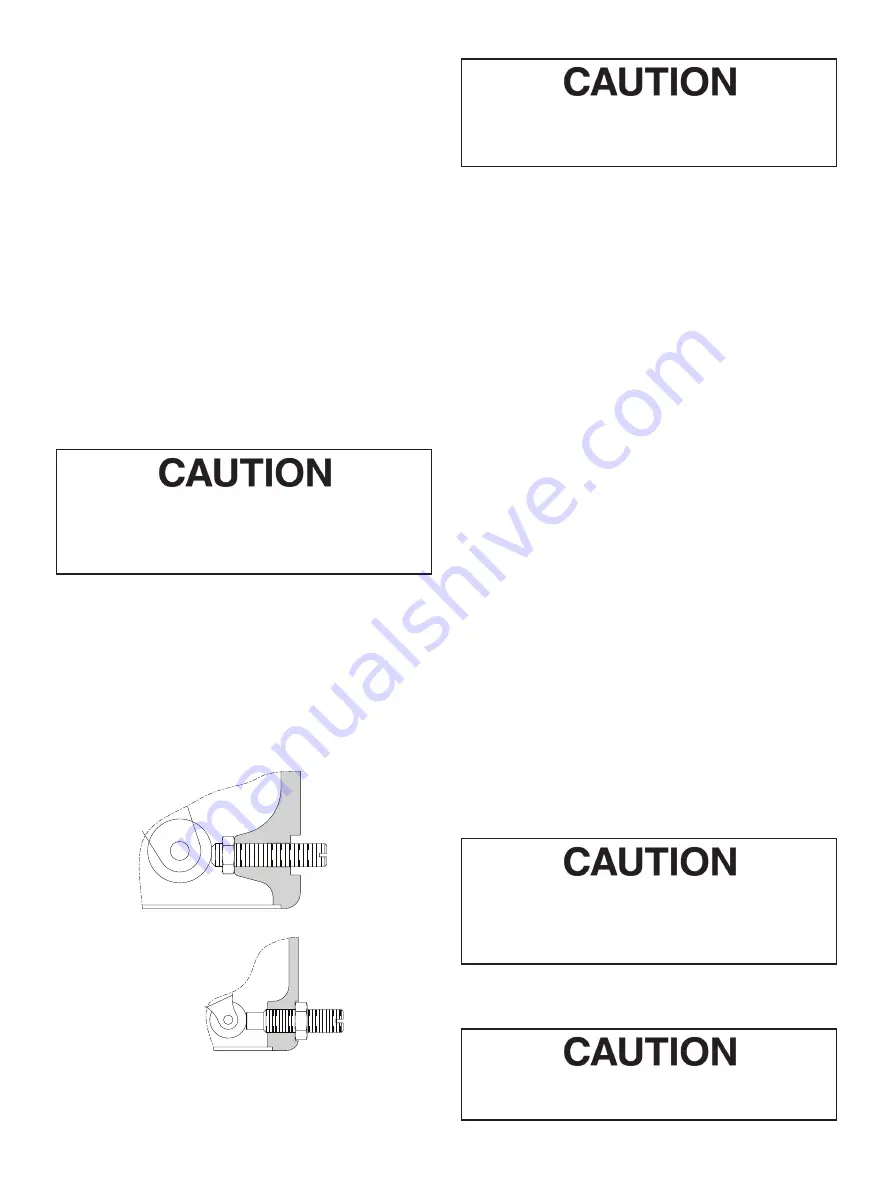
Masoneilan 35002 Series Camflex II Instruction Manual | 10
Copyright 2020 Baker Hughes Company. All rights reserved.
D.
Slide the valve shaft partly into the lower yoke opening,
allowing enough room to place packing flange (14) over the
shaft (19).
Note: Packing flange (14) is placed on the shaft (19)
with the concave side toward the valve packing (17).
E.
Ensure slots in packing flange (14) line up with packing
flange studs (13).
F.
With packing flange on the shaft, continue sliding the valve
shaft toward the yoke (33) and through the grommet (12) in
the yoke (33).
G.
Place the lever (34) in the yoke and in line with the shaft so
the boss on one side of the lever shaft hole is toward the
shaft bearing (8) and engage the shaft to the lever splines.
Note: Shaft must engage lever so the indicator dot on
the clevis pin, when placed in the lever hole, shows the
valve closed. Temporarily place clevis pin into lever
(34) and check indicator dot alignment. Dot should just
start touching the closed indicator line on the front
cover (32) (Refer to Figure 18). If the orientation is not
changed, align lever and mark on yoke then check
alignment. (Refer to Figure 17).
Do not use air pressure to check alignment, since
during normal operation and with full air pressure,
the Indicator may overshoot the closed Indicator
mark on the cover. This is acceptable.
H.
Slide shaft completely through lever to engage shaft bearing
(8). Yoke should now be fully seated on the valve bonnet
flange.
I.
Replace and tighten body stud nuts (27).
J.
Replace packing flange stud nuts (94) and finger tighten
only.
K.
Slide the lever (34) on the shaft (19) toward the valve and
tighten lever capscrew (49).
L.
Pull the lever and shaft toward the bearing (8) in the yoke.
LIMIT STOP STD CAMFLEX 6" and 7"
LIMIT STOP STD CAMFLEX 4.5"
.
Figure 9
This is required to ensure the shaft (19) is shouldered
on the shaft bearing (8) and to ensure free operation
of the valve.
M.
Loosen lever capscrew (49) and slide lever (34) so it will
shoulder against the shaft bearing (8) and tighten capscrew
(49).
Note: if the actuator cylinder (38) has been removed
proceed to step N. If it has not, proceed to Section 11,
Actuator Stem Adjustment.
N.
Determine the desired actuator action and replace actuator
cylinder (38) on the yoke (33) and secure in place with four
capscrews (36) and lockwashers (37).
O.
Proceed to Section 11, Actuator Stem Adjustment.
10.3 Handwheel Reassembly
A.
Place the valve so the position cover (11) is up.
B.
Remove Truac ring (50) and handwheel washer (51) from
the handwheel powerscrew.
C.
Insert handwheel powerscrew with lock (52) in place into the
appropriate hole in the yoke and screw in clockwise.
D.
Replace the washer (51) and Truac ring (50)
E.
Back off handwheel lightly against washer and lock in the off
position with lock (52).
F.
Replace bottom cover (11) by snapping in place.
Note: To use the handwheel, loosen the lock (52) and
turn. The handwheel can be used as a limit stop on the
valve by locking it in any position.
10.4 Limit Stop Reassembly
Two different types of assembly for the limit stop in function of
the actuator size: see Figure 9.
10.5 Valve Body Reassembly
(Refer to Figure 16)
Prior to reassembly, the valve body should be thoroughly cleaned
and the seat ring and plug may be lapped as indicated in Section
9.2. Upon completion of the above, proceed as follows:
Lubricants and sealers are required during reassem-
bly. Figure 15 identifies recommended products for
certain service conditions. Ensure that any lubricant
used is compatible with service conditions.
A.
Apply a small amount of thread lubricant to the seat ring
retainer threads and install seat ring retainer (3) and hand
tighten only.
Do not tighten the seat ring retainer to torque specifi-
cation at this time.