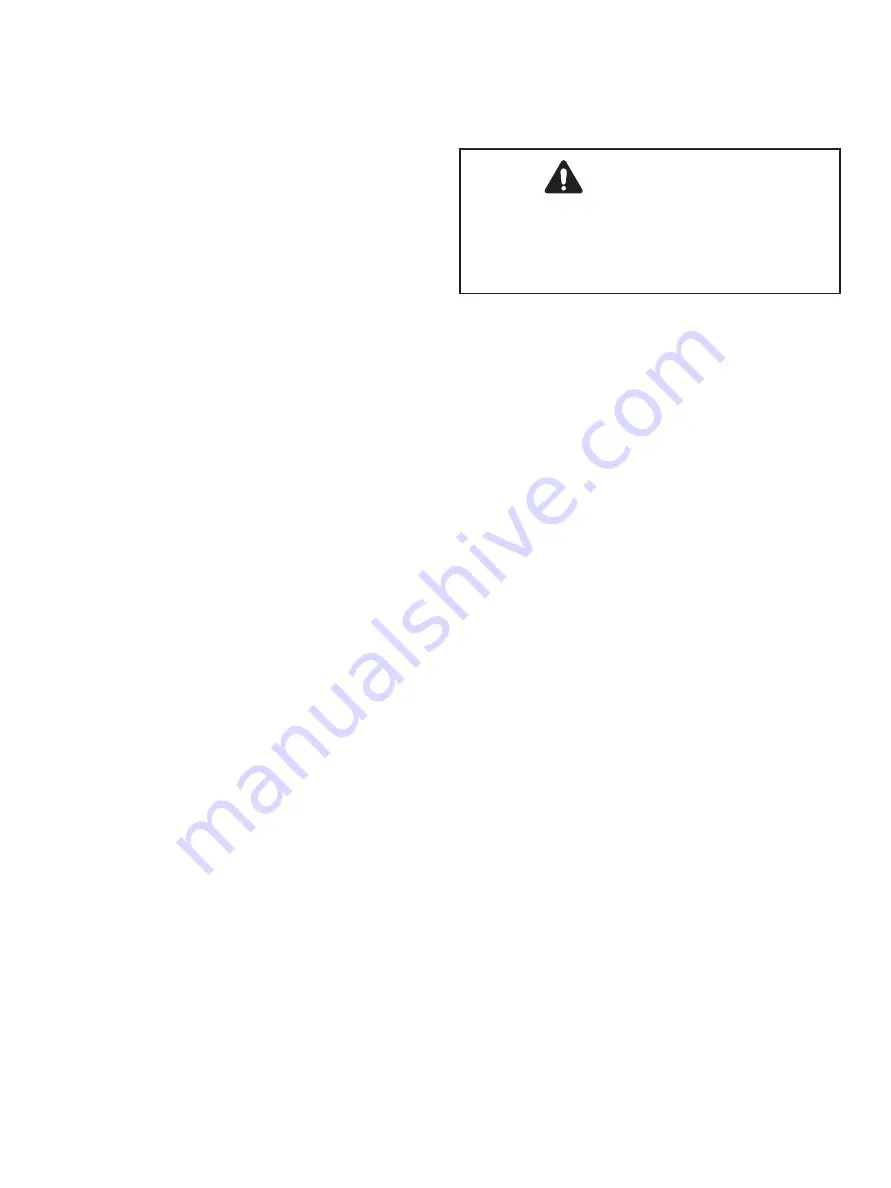
12 | Baker Hughes
Copyright 2020 Baker Hughes Company. All rights reserved.
G. Remove the End Plate. Check free rotation of the shaft.
Tight the thrust pad Bolts (B915) using Allen key by holding
shaft square using spanner.
H. Apply a thin layer of MOLYBDENUM GREASE or equivalent
to the gasket sealing area and Loctite 222 or equivalent on
the required End Plate Bolting (B913a). Re-fit the End Plate
including Gasket (B015) using the torques specified on the
Table-2.
I. Rotate the Shaft 360° - if there is no free rotational movement
the fitter shall repeat step 6. If there is a high- spot or notable
abrasion the fitter shall repeat step E.
J. At the opposite end of the Valve Body, carefully insert the
Gland Packing Ring (B202) and then the first of two Braided
Packing pieces (B206). Insert 3 off Passivated Packing
pieces (B206), lightly greased. Apply the second Braided
Packing piece (B206) (position the split end at 180° to the
first piece) and compact using the Gland (B213) or specific
compression tool.
Note: do not over compress packing; ensure free
rotational movement of Shaft.
K. Apply Loctite 222 or equivalent to the Threaded Studs
(B200). Screw the studs into position and lock. Position the
Gland (B213) over the Shaft and loosely secure with Nuts
(B201) supplied. Do not compress Packing.
L. Fit the Disc (B137) over the Shaft ensuring the machined
line on the end of the Shaft is in parallel.
M. Offer the mating Disc Seat (B138) into position. Secure using
required bolting (B913) (bolting should be lightly greased
with MOLYKOTE
®
1000 PASTE or equivalent on the thread
and shoulder to allow correct input torque). Tighten the bolts
(B913) ‘finger tight’ and release by one half turn - do not
apply torque.
Note: Disc Seat (B138) Angled side bottom and flat side
top.
N. Place the Seat Ring Gasket (B103), Seat Ring (B102) and
Retainer (B105) into the Body Counter bore. Secure with
required bolting (bolting should be lightly greased with
MOLYKOTE
®
1000 PASTE or equivalent on the thread and
shoulder to allow correct input torque). Tighten the bolts
‘finger tight’ and release by one complete turn - do not apply
torque.
Note: Seat Ring Orientation should match with that of
Disc, i.e. Flat side of Seat Ring and that of Disc should
match.
Single Disc 3 and 4 inch sizes class
600 (Keyed Shaft Assembly) (Figure 8)
After removing the actuator, disassemble the body using the
following procedure:
WARNING
During assembly or maintenance, and under
operation in some conditions the operators or
technicians must be alert and aware of all possible
pinch points or areas where there are moving or
sliding components.
Place the valve body (B001) in the still position.
A. Repeat steps A to D from previous section “Disc Seat
2-Piece Design”
B. Insert the Key(B929) into the keyway of the shaft(B123)
and Coat the bearing surfaces of the shaft(B123) with
MOLYBDENUM GREASE or equivalent.
C. Hold the Integrated disc and disc seat(B138) in the bore of
the Valve and carefully pass the shaft(B123) through the
cross bore from the Gland (B213) end, align the key(B929)
with the keyway in the Integrated disc and Disc Set(B138)
and pass the shaft(B123) through the endplate(B010)
end of the cross bore avoiding damage to the bearing
protectors(B208).
Note: Integrated Disc and Disc seat(B138) angled side
bottom and bottom side
D. Tighten the Integrated disc and disc seat(B138) with
shaft(B123) using Grub screw(B914). Ensure that machined
line at the shaft is parallel to the disc.
E. Attach the Thrust Pad(B139) to the end of the Shaft(B123)
with Cap-head Bolts(B915) (threads may be covered with
the specified grease – use of Loctite or equivalent is not
permitted). Rotate the Shaft through 90° to allow the Thrust
Pad(B139) to self-center in the Body Bore and lock the Cap-
head Bolts(B915) in position.
F. Repeat steps A to D from previous section “Disc Seat
2-Piece Design”.