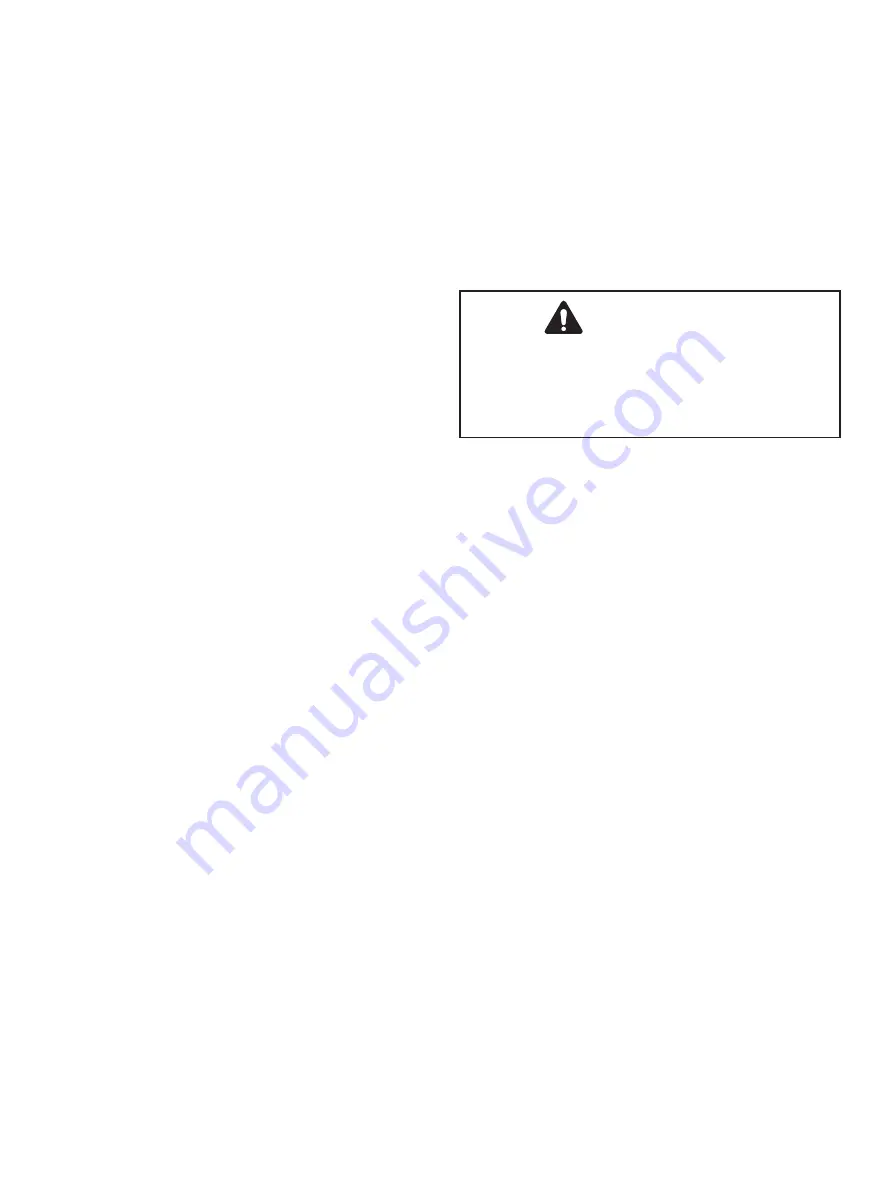
Masoneilan 33000 Series Butterfly Valves Instruction Manual | 11
Copyright 2020 Baker Hughes Company. All rights reserved.
11. Maintenance and Repair
The purpose of this section is to provide recommended
maintenance and repair procedures. These procedures assume
the availability of standard shop tools and equipment.
Preventative Maintenance
The functioning and life of a Butterfly valve largely depends on
proper maintenance. For this reason, guidance, should be taken
from the following:
A. Always read the Technical Instruction specific to the valve
type being installed.
B. Prior to any work being undertaken on valves, reference
should always be made to site safety procedures.
C. Periodic inspections should be undertaken to check that no
damage has occurred that could affect valve performance.
D. Check all valve joints if practicable, including the valve
packing or gland seals for signs of leakage.
E. Check for any signs of corrosion on the valve if lagging does
not restrict this operation.
F. Check that all clamp nuts, screws, bolts etc. are tight.
G. Check that all shaft packing is tight. Adjustment may be
required to prevent stem leakage.
Where practical, establish that the valve is free to operate. Baker
Hughes recommends regular cycling of its product to ensure free
movement of the drive-chain (minimum weekly). Shafts, gearing
and other moving components outside of the valve internals
should be lubricated frequently. If the valve is not free to operate
this could indicate internal problems.
Any remedial action that requires valve removal and
refurbishment should be noted and undertaken at the earliest
convenience. Problems that could affect operational safety
should be addressed immediately.
12. Valve Body Reassembly
After completion of the required maintenance, the valve should
be reassembled using the following procedures:
Note: If any of the following steps were completed during
maintenance, then proceed to the next step.
Disc Seat 2-Piece Design - Standard
(Figure 7)
After removing the actuator, disassemble the body using the
following procedure:
WARNING
During assembly or maintenance, and under
operation in some conditions the operators or
technicians must be alert and aware of all possible
pinch points or areas where there are moving or
sliding components.
A.
Attach the Thrust Pad (B139) to the end of the Shaft with
Cap-head Bolts (B915).
B. Apply MOLYKOTE(R) 321 DRY FILM LUBRICANT or
equivalent to the Bearings (B011) and Shaft (B123) bearing
surfaces. Allow 5-minute drying period.
Note: Air can be used to assist drying of the applied
coating as shown below.
C. Remove excess film coating from Bearing and shaft surface
using cloth or scrubber.
D. Insert Bearing Protectors (B208) into Valve Body (B001)
bore. Apply MOLYBDENUM GREASE or equivalent to the
outer diameter of the Bearings and/or inner diameter of the
body bore. Insert required number of Bearings into either
end of the valve body. Apply MOLYBDENUM GREASE or
equivalent to inside surface of the Bearing.
Note: Chamfered Edge of the Bearing should enter first
while inserting the Bearing. Ensure Bearing is properly
seated on the Bearing Protector.
E. Coat the bearing surfaces of the Shaft (B123) with the
MOLYBDENUM GREASE or equivalent and carefully pass
the Shaft through the Bearings, avoiding damage to the
Bearing Protectors (B208). Rotate the Shaft 360° to allow
the Thrust Pad(B139) to self-center in the Body Bore and
lock the Cap-head Bolts(B915) in position to the required
torque.
F. With the Shaft in position attach the End Plate (B010) (without
End Plate Gasket (B015)) and lock down to compress the
Bearing Protector in the Body bore. Wait for one minute to
allow the end plate(B010) to compress the shaft.