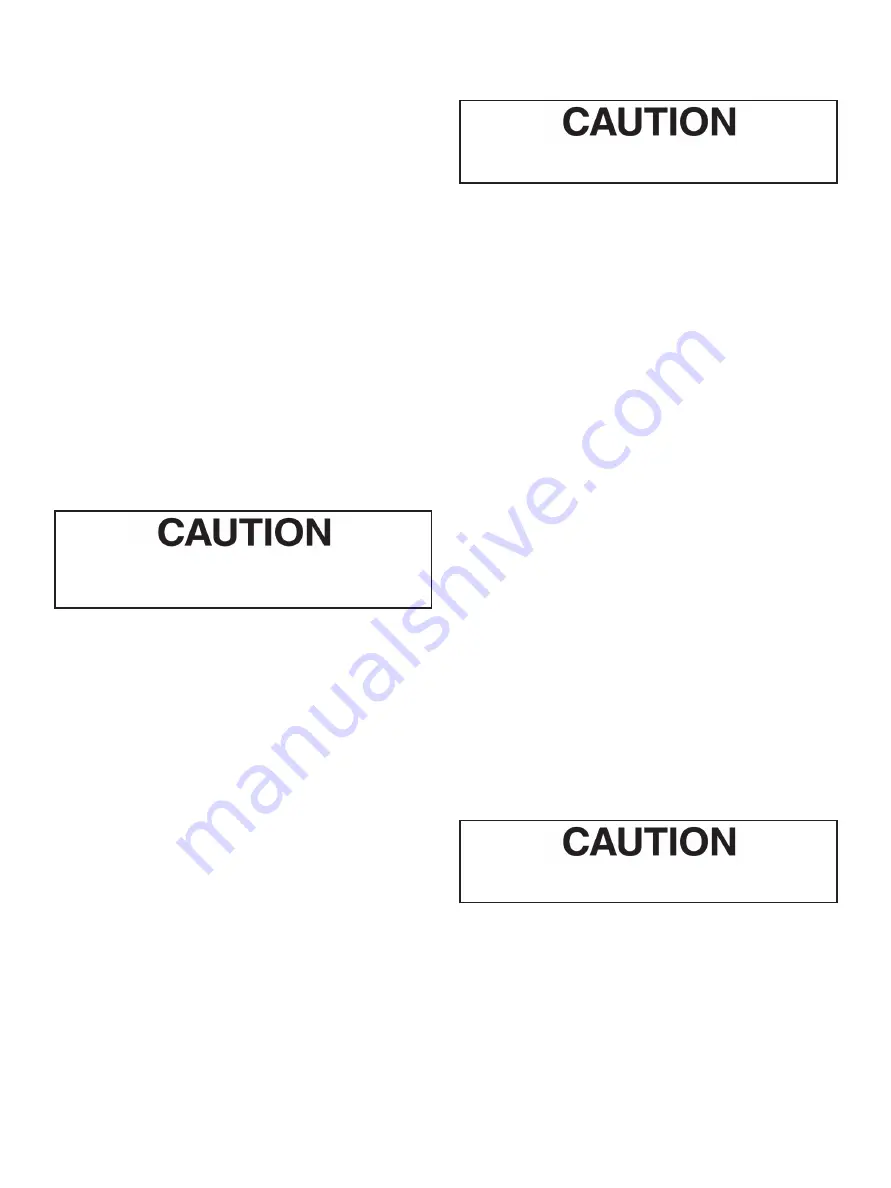
5 | Baker Hughes
Copyright 2021 Baker Hughes Company. All rights reserved.
B. Screwing Stem to Plug
Refer to step B of the previous section on “REPLACING PLUG
AND STEM”.
C. Drilling the new Stem
PIace the plug guide on a V-block and use a suitable size drill bit to
drill the stem (use the hole in the plug as a guide).
Note: If the hole in the plug guide has been slightly damaged
while removing the old pin, choose a drill bit and a pin with
a slightly larger diameter than the normal pin.
D. Pinning
Select the correct size pin based on the plug guide diameter and
pin hole diameter. Proceed as described in part D of the previous
section, taking care not to damage the plug guide area.
Ensure plug stem alignment following the pinning operation.
7.3 Packing Box
Packing box maintenance is one of the principle action items
of routine servicing. Tightness of the packing is maintained
by packing compression. Compression is achieved by evenly
tightening the packing flange nuts (3) against the packing flange
(4). Care must be taken not to over tighten as this could prevent
smooth operation of the valve. If all compression is used up and
the valve leaks, then new packing is required.
Valve must be isolated and the pressure vented before
performing packing box maintenance.
Proceed as follows:
7.3.1 Braided PTFE with Carbon or aramid Core (Standard)
Note: The Braided PTFE/Carbon or Aramid packing rings
have a skive cut allowing packing replacement without
discon-necting the plug stem from the actuator connector
or actuator stem.
A.
Loosen and remove packing flange nuts (3).
B.
Lift the packing flange (4) and packing follower (5) up the
valve stem.
Note: They may be taped in place to keep them out of the
way before proceeding.
C.
By means of a hooked instrument , remove packing (6)
ensuring not to damage the sealing surfaces of the packing
box or plug stem.
Note: On valves equipped with an optional lubricator
connection, the lantern ring (7) must also be removed to
gain access to lower packing rings.
D.
Replace packing rings (6).
Note: Assemble and compress rings one at a time into
packing box. The skive cut of each packing ring must be
placed about 120 degrees apart.
Note: On valves equipped with an optional lubricator
connection, refer to Figure 7 for correct amount of rings to
place under the lantern ring (7).
E.
Replace packing follower (5) and packing flange (4).
F.
Replace and tighten packing stud nuts (3).
Do not overtighten.
G.
Place valve back in service and only tighten packing as
necessary to stop external leakage.
Note: In an emergency, string packing may be used as a
temporary repair only. It must be replaced with the correct
packing as soon as possible.
7.3.2 Flexible graphite rings (optional-See Figure 5)
Note: Flexible graphite packing rings replacement may
require disconnecting the plug stem from the actuator stem
and removal of the actuator if rings are not skive cut.
A.
Remove actuator from the body S/A. Refer to actuator
instruction Ref. GEA19530 for a type 87/88 actuator.
B.
Loosen and remove packing flange nuts (3).
C.
Remove packing flange (4) and packing follower (5) from the
plug stem.
D.
By means of a hooked instrument , remove packing (6)
ensuring not to damage the sealing surfaces of the packing
box or plug stem.
Note: On valves equipped with an optional lubricator
connection, the lantern ring (7) must also be removed to
gain access to lower packing rings.
E.
Replace new packing set (6); first assemble a back- up
ring (Graphite Filament Yarn braided ring), then the flexible
graphite rings (smooth rings), and finally another braided
back-up ring (refer to Figure 5).
Note: Assemble and compress rings one at a time into
packing box.
Note: On valves equipped with an optional lubricator
connection, refer to Figure 7 for correct arrangement
according to valve size.
F.
Assemble packing follower (5) and packing flange (4).
G.
Assemble and tighten packing stud nuts (3).
Do not overtighten.
H.
Proceed to appropriate instructions for actuator and valve
assembly adjustment.
I.
Place valve back in service and only tighten packing as
necessary to stop external leakage.