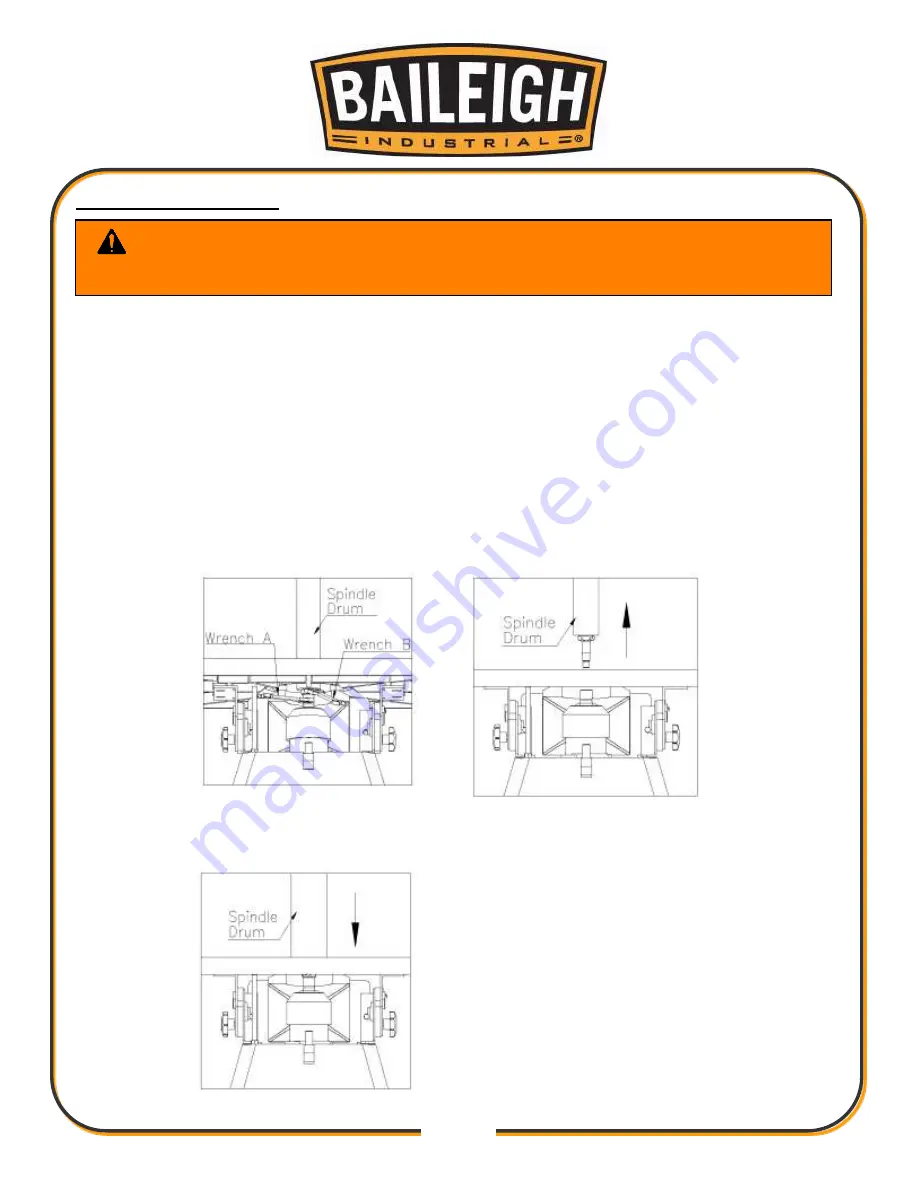
21
21
Mounting Spindle Drum
1. Disconnect the sander from the power source.
1. Select the proper diameter of spindle drum.
2. Clean the taper part of the spindle drum before mounting it into the spindle.
3. Use an open-end wrench to lock the spindle by holding its flat surface. At the same time,
use another open-end wrench to tighten the spindle drum.
4. Lift straight upward on the spindle drum to remove it.
5. Install the spindle squarely into the chuck.
6. Tighten using two wrenches. Do not over tighten the spindle drum or it will be causing
removable problem.
WARNING:
ALWAYS disconnect power to the machine before changing
spindles or working on it for any reason.
Use a wrench to lock the
spindle. Use another wrench
to loosen the spindle drum.
Fitting a new spindle drum.
Removing an old spindle drum
Summary of Contents for OS-2424
Page 16: ...14 14 OVERALL DIMENSIONS 24 610 24 610 39 990...
Page 17: ...15 15 GETTING TO KNOW YOUR MACHINE...
Page 27: ...25 25 PARTS DIAGRAM 1...
Page 31: ...29 29 NOTES...