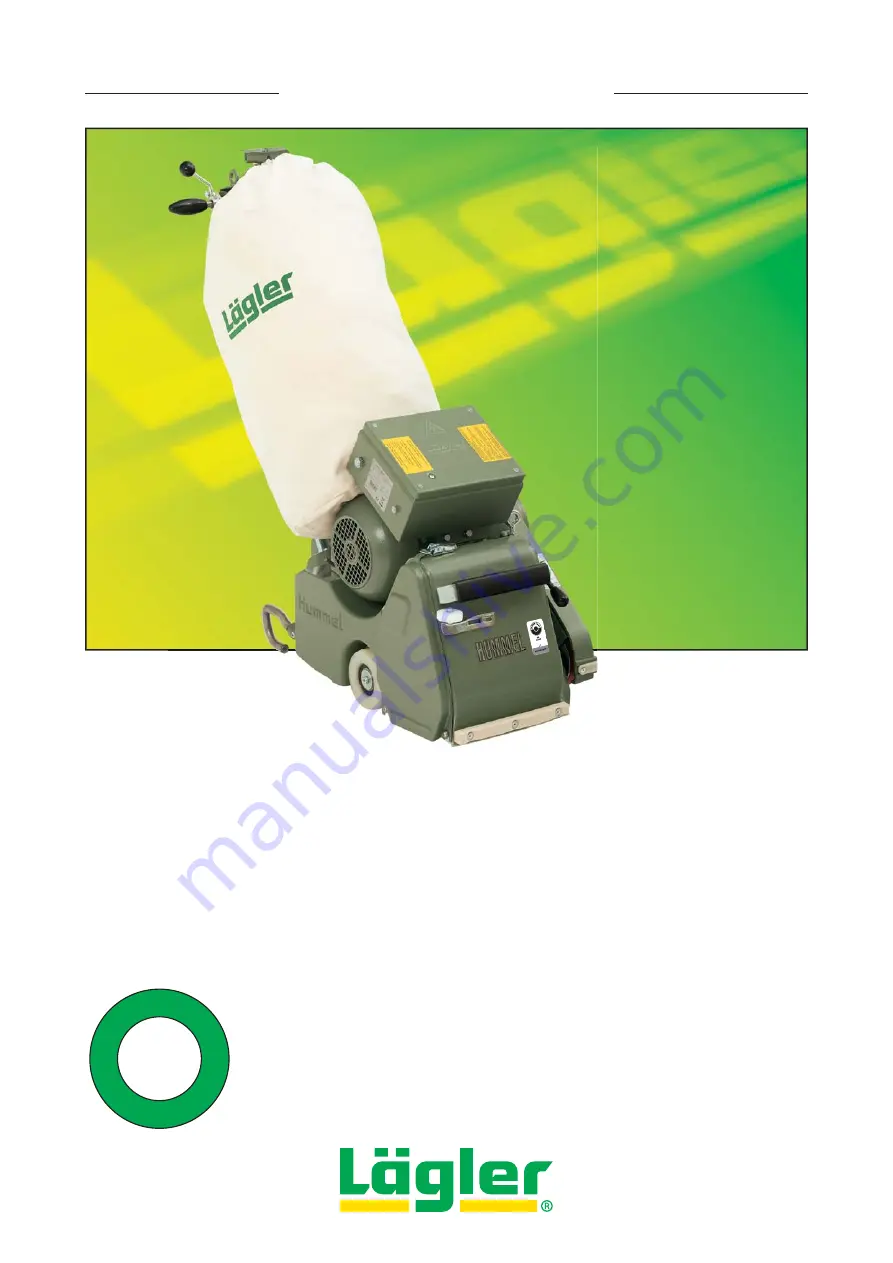
BELT SANDING MACHINE HUMMEL
®
HUMMEL
®
English / Englisch
S
ta
u
b
-
d
us
t
-
p
ou
ss
iè
re
- p
o
lv
o
S
ta
u
b
-
d
us
t
-
p
ou
ss
iè
re
- p
o
lv
o
- -
<
1
mg/m³
Operation,
Maintenance, Safety
Translation of original operating instructions
for the belt sanding machine
00.100.20.002 01.12.2012
*00.100.20.002*
Summary of Contents for HUMMEL
Page 56: ...HUMMEL 01 12 2012 English Englisch SPARE PARTS 56 11...
Page 58: ...HUMMEL 01 12 2012 English Englisch SPARE PARTS 58 11...
Page 60: ...HUMMEL 01 12 2012 English Englisch SPARE PARTS 60 11...
Page 64: ...HUMMEL 01 12 2012 English Englisch SPARE PARTS 64 11...
Page 66: ...HUMMEL 01 12 2012 English Englisch SPARE PARTS 66 11...
Page 68: ...HUMMEL 01 12 2012 English Englisch NOTES 68...
Page 69: ...HUMMEL 01 12 2012 English Englisch NOTES 69...