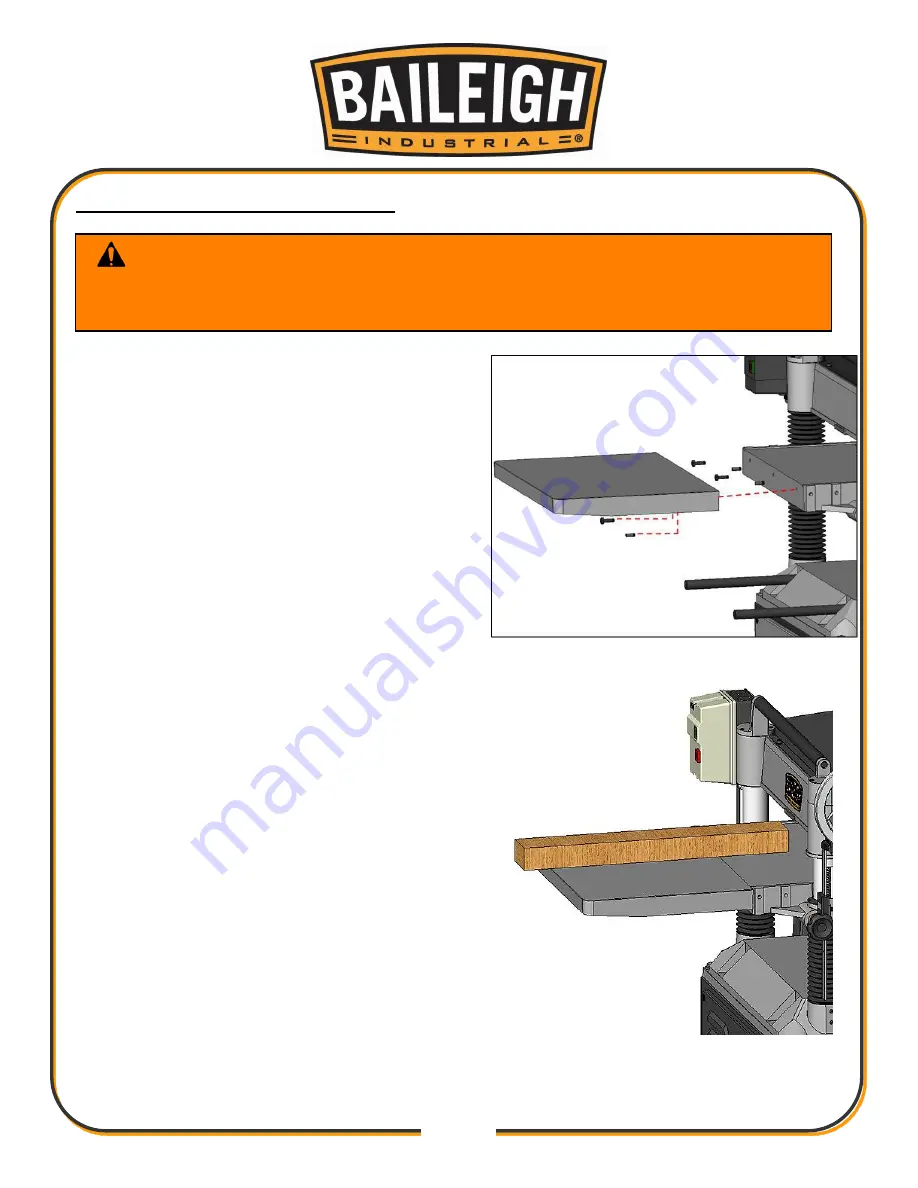
12
12
ASSEMBLY EXTENSION TABLE
1. Use an assistant to help lift and align the holes
on the extension table to the main table.
2. Insert the bolts and loosely secure with
washers and nuts. (Fig. 2).
3. With the fasteners in position and snug, place
straight edge through machine so that it lies
across the main table and extension table.
(Fig. 3).
4. Align the extension table to the main table.
When the tables are aligned, hold in position
and securely tighten the fasteners.
WARNING:
For your own safety, DO NOT connect the machine to the
power source until the machine is completely assembled and you read and
understand the entire instruction manual.
Fig. 2
Fig. 3
Summary of Contents for IP-208
Page 17: ...15 15 ELECTRICAL DIAGRAM...
Page 32: ...30 30 PARTS DIAGRAM SHEET 1 To Parts Sheet 2...
Page 33: ...31 31 PARTS DIAGRAM SHEET 2 To Parts Sheet 1...
Page 34: ...32 32 PARTS DIAGRAM SHEET 3...
Page 35: ...33 33 PARTS DIAGRAM SHEET 4...
Page 43: ...41 41 NOTES...