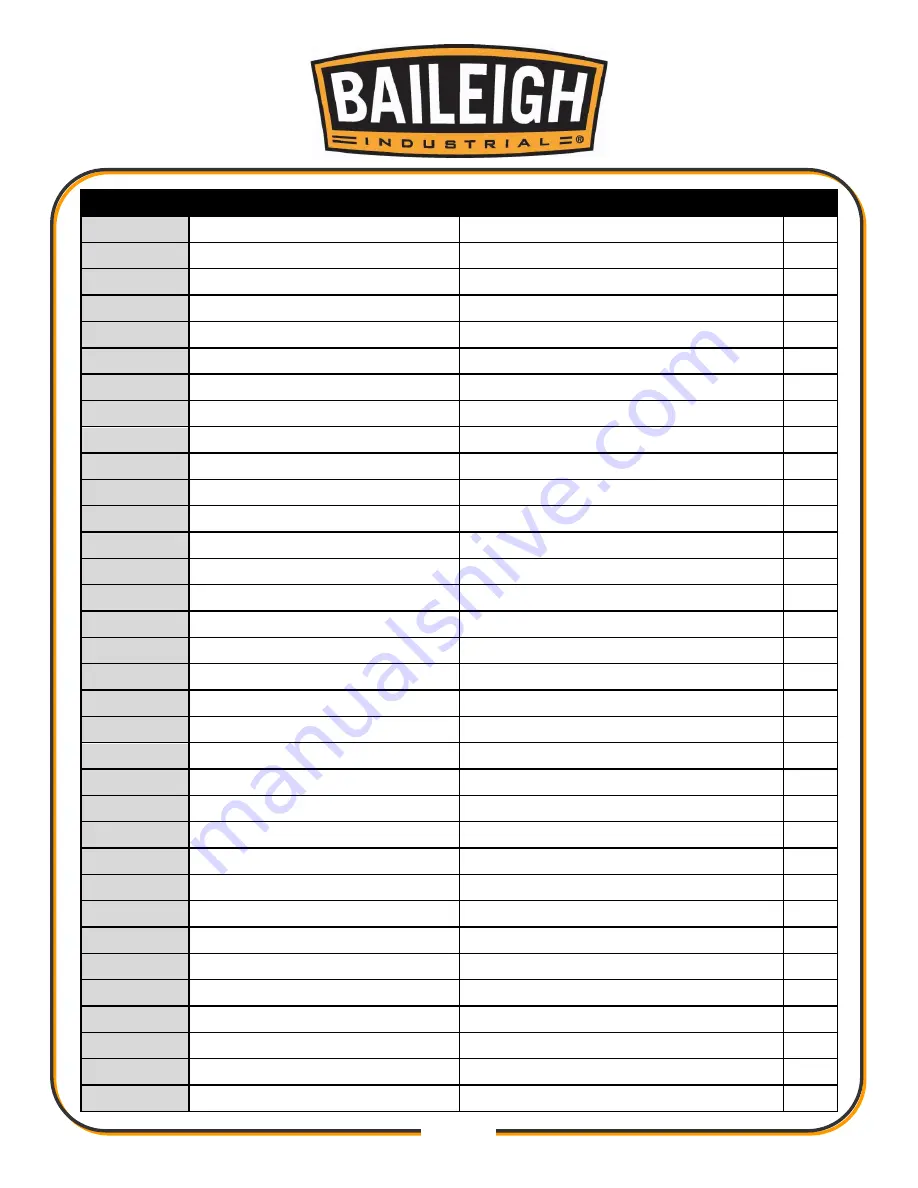
42
42
Item
Description
Size No.
Qty.
26-1
Slide Bracket
1
26-2
Set Screw
M6x8
1
27-1
Rack
1
28-1
Rack Block
1
29-1
Pin
1
30
Closed Bearing
HK25 15
2
30-1
Bushing
1
31
Torsion Spring
1
32
Pivot Shaft
1
32-1
Spacer
M12
2
32-2
Hex. Cap Bolt
M12x20
2
33
Pivot Bracket
1
33-1
Set Screw
M10x12
1
34
Nut
M12
1
35
Washer
M12
1
36
Hex. Cap Bolt
M12x40
1
37
Torsion Spring Shaft
1
38
C-Ring
S-22
1
39
Hex. Cap Bolt
M8x30
1
39-1
Washer
M8
1
39-2
Nut
M8
1
40
Motor Tilt Plate
1
41
Limit Switch Plate
1
42
Washer
M8
2
43
Hex. Cap Bolt
M8x20
2
43-1
Lock Washer
M8
2
44
Hex. Cap Bolt
M6x12
4
44-1
Washer
M6
4
45
Limit Switch
1
46
Drain Plug
3/8PT
1
47
Cylinder Pin
1
48
C-Ring
S-20
1
49
C-Ring
S-25
2
50
Hex. Cap Bolt
M10x30
1
Summary of Contents for BS-300M
Page 16: ...13 13 GETTING TO KNOW YOUR MACHINE S T U V W X R A G E D C F B H I J K L N P Q O M...
Page 29: ...26 26...
Page 42: ...39 39 PARTS DIAGRAM...
Page 43: ...40 40...
Page 52: ...49 49 ELECTRICAL COMPONENTS...
Page 54: ...51 51 ELECTRICAL SCHEMATIC...
Page 55: ...52 52 NOTES...