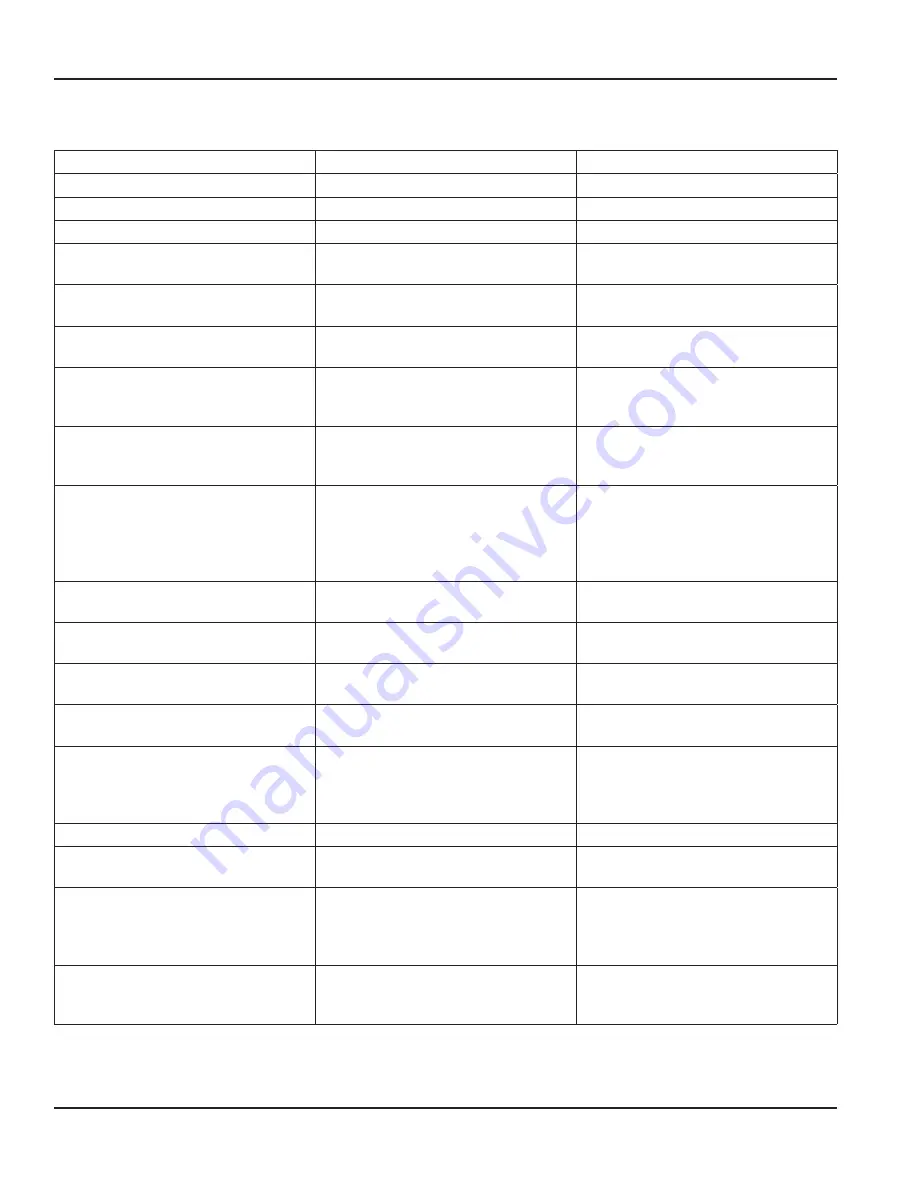
TROUBLESHOOTING
Issue
Possible Cause
Remedy
Meter indicates higher flow than actual . Cavitation .
Increase back pressure .
Meter indicates high flow .
Dirt blocking flow area rotor .
Clean meter; add filter .
Meter indicates low flow .
Dirt dragging rotor .
Clean meter; add filter .
Meter indicates low flow .
Worn bearing .
Replace bearing; recalibrate when
required .
Meter indicates low flow .
Viscosity higher than calibrated .
Change temperature; change fluid;
recalibrate meter .
Erratic system indication; meter alone
works well .
Ground loop is shielding .
Ground shield one place only . Watch for
internal electronic instrument grounds .
Indicator shows flow when shut off .
Mechanical vibration causes rotor to
oscillate without turning .
Mechanical vibration .
Isolate meter; use potted pickoff .
No flow indication . Full flow of fluid
opened into dry meter . Impact of fluid
on rotor causes bearing separation .
Fluid shock . New bearing failed .
Move meter to position where it is full
of fluid at start-up .
Erratic indication at low flow; good
indication at high flow .
Low instrument sensitivity . 10
mV rms turbine signal is being
lowered by loading of electronics or
instrumentation cannot sense low level
signals .
Amplify signal .
No flow indication .
Faulty pickoff .
Replace pickoff; recalibrate as
necessary .
System works perfectly, except
indicates lower flow over entire range .
Bypass flow, leak .
Eliminate bypass valves, leak . Faulty
solenoid valves .
Meter indicating high flow . Upstream
piping at meter smaller than meter .
Fluid jet impingement on rotor . Critical
in gas .
Change piping .
Opposite effects as above .
Viscosity lower than calibrated .
Change temperature; change fluid;
recalibrate meter .
Mass flow indication wrong . Turbine
meter is volumetric; density correction
is electronic; must change with
temperature .
Wrong fluid density . Critical in gas .
Check fluid, electronics .
Erratic or wrong indication of flow .
Loose pickoff .
Tighten pickoff .
Indicates high flow two hours after
installing new bearing .
Bearing wear-in; small meters critical .
Recalibrate . 20…30 min . run-in is
required to stabilize friction .
Cannot reach maximum flow rate;
meter selection was with Delta-P at 0 .75
sp . gr ., now using on 1 .0 sp . gr . Delta-P
is proportional to specific gravity .
High pressure drop .
Install larger meter .
Does not repeat at low flows . Repeats at
high flows .
System resolution readability .
Increase resolution, for example:
1 out of 100 = 1%
1 out of 1000 = 0 .1%
Table 1: Troubleshooting
Precision Meters, Turbine Flow Meters
Page 10
May 2014