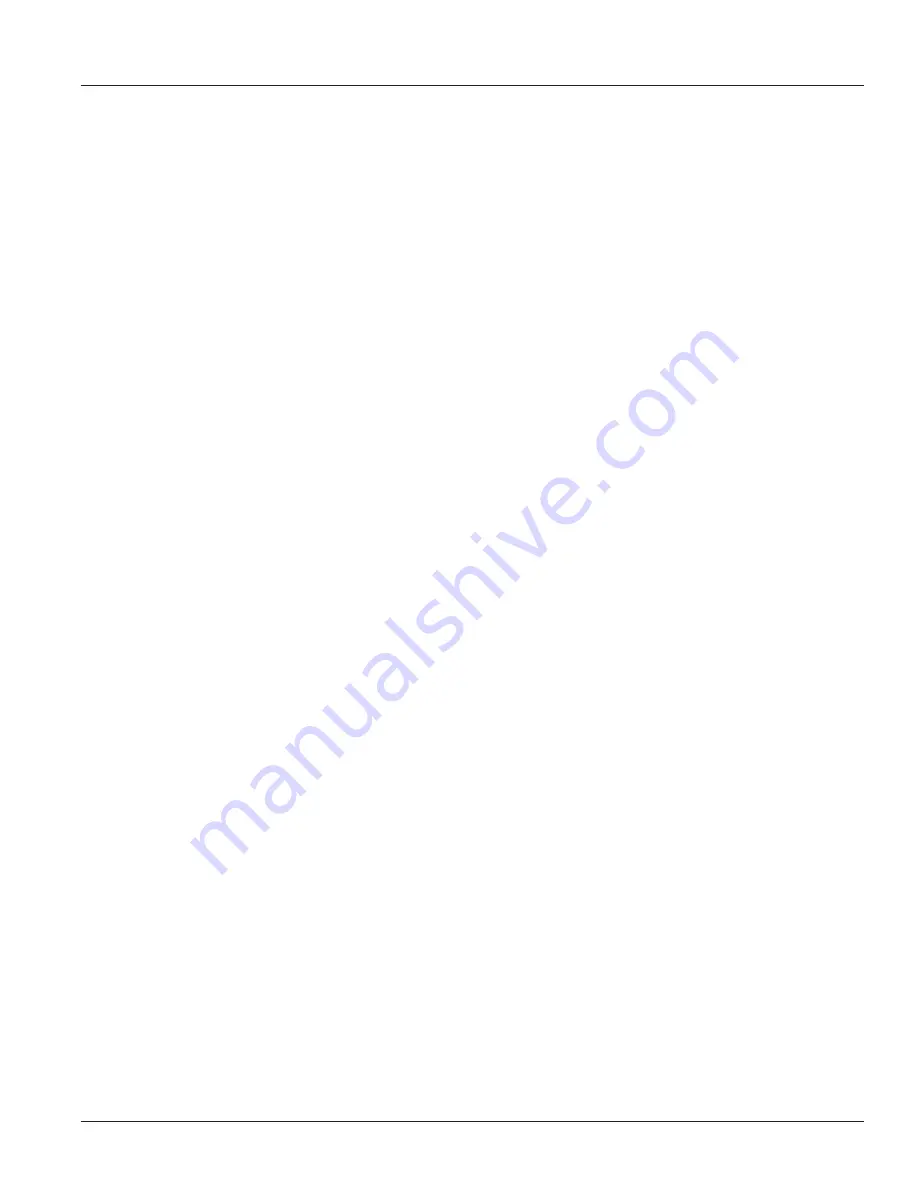
Page 6
7-11
Series 380 Impeller Btu System
MECHANICAL INSTALLATION
General
The accuracy of flow measurement for all flow measuring devices is highly dependent on proper location of the sensor in the
piping system. Irregular flow velocity profiles caused by valves, fittings, pipe bends, etc. can lead to inaccurate overall flow
rate indications, even though local flow velocity measurement may be accurate. A sensor located in the pipe can be affected
by air bubbles, floating debris, or sediment may not achieve full accuracy and could be damaged. Badger Meter flow sensors
are designed to operate reliably under adverse conditions, but the following recommendations should be followed to ensure
maximum system accuracy.
1.
Choose a location along the pipe where 10 pipe diameters upstream and 5 pipe diameters downstream of the
sensor provide no flow disturbances. Pipe bends, valves, other fittings, pipe enlargements and reductions should not
be present in this length of pipe.
2.
The recommended location for the sensor around the circumference of a horizontal pipe is on top of the pipe. The
sensor should never be located at the bottom of the pipe, as sediment may collect there. Locations away from the
top-center on a pipe cause the impeller friction to increase, which may affect performance at low flow rates. Any
circumferential location is correct for installation in vertical pipes. Rising flow is preferred to reduce effects of any
trapped air.
Installing the Sensor Tee
1.
Position the tee for unrestricted pipe flow for at least 10 pipe diameters upstream and 5 pipe diameters downstream
of the tee.
2.
Apply pipe compound over the first 3 or 4 threads of the mating pipe.
3.
Thread the pipe into the sensor tee until hand tight.
4.
Tighten the pipe an additional 1-1/2 turns, using a wrench.
ELECTRICAL INSTALLATION
1.
The Series 380 requires an isolated 12-24 V AC/DC power supply. To avoid ground fault conditions, the 380 power
should not be shared with other devices. This is especially true when the RS-485 network connections are being
utilized, where damage to the product or system could result.
The power connections are labeled 1 and 2 and are not polarity sensitive.
2.
The RS-485 requires three connections: RS-485+, RS-485- and REF.
The connections are labeled 1 (+), 2 (-) and 3 (GND). RS-485 is a high-speed connection and should be wired to meet
TIA-EIA-485-A standards.
This is especially true if a long cable run is involved or multiple devices are to be networked.
3.
The pulse output is a simple solid state switch.
The connections are labeled "PULSE OUTPUT 1" and "PULSE OUTPUT 2". The switch is not polarity sensitive, however,
be careful that the maximum voltage and current ratings are not exceeded. See "SPECIFICATIONS" on page 11 for
details.
Note:
The pulse and RS-485 may be used simultaneously.