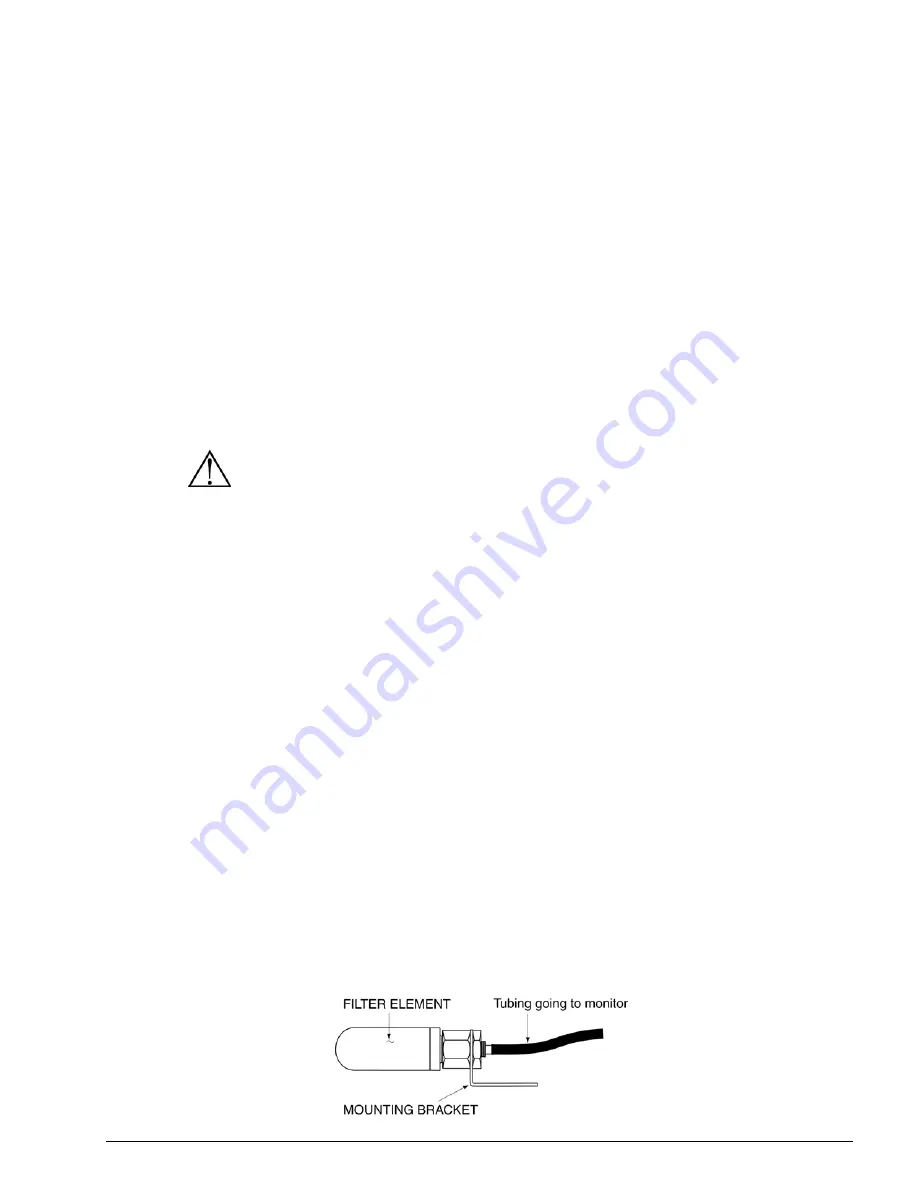
Instruction 3015-4286
7
Tubing Considerations
Use ¼ in. outside diameter (0.040 in. wall) flex tubing for all air lines (P/N 304-2742 or equivalent). The tubing
should be clean and free of moisture or other contaminants. The tubing should be cut cleanly with a sharp knife
and care should be taken not to distort the tubing end.
IMPORTANT!
Due to the reactive nature of ammonia gas, it is important to use materials that will not absorb
the gas as it passes through the sampling system. The use of unauthorized tubing or any other materials in the
gas-sampling stream may lead to erroneously low readings.
All tubing bends should have a radius of no less than 5" to insure proper airflow. If kinks or obstructions occur in
the line the monitor may not function properly.
Connecting the Gas-Sample Line
Please refer to Section
Suggested Location of Sampling Point
(Page 4) to learn more about where to take a gas
sample.
The gas-sample line can be up to 500 ft (152.4 m) in length. The end of this line should be placed near the
potential leak source and positioned to reduce the possibility of mists, aerosols, oil, water, dust, or other
contaminates from being drawn into the monitor. For added protection, a termination filter (P/N 3015-3420)
supplied with the monitor must be attached to the end of this line.
CAUTION:
The introduction of contaminants through the gas-sample line can
result in serious and permanent damage to the monitor.
Connecting the Purge Line
The purge line functions to bring fresh (zero) air into the monitor for the purpose of purging the detector and
setting its baseline zero reading. This purge line is required if the monitor is located in an area that contains
ammonia gas or other types of refrigerant.
The purge line can be up to
100 ft (30.5 m)
in length. This line should terminate in an area known to contain
fresh air. To connect the purge line to the monitor, simply push the tubing into the Purge Air Inlet Port. If the
purge line terminates outside the building, position the tubing so that no water or moisture can enter the line.
For added protection from contaminates entering the monitor, a termination filter (P/N 3015-3420) must be
attached to the end of this line.
Connecting the Exhaust Line
The exhaust line functions to carry the exhausted gas sample away from the monitor, and is required if the
monitor is located in a confined, poorly ventilated area. If no purge line is used, it is a good idea to vent the
exhausted gas sample away from the monitor to prevent erroneous readings due to improper zeroing of
the detector.
The exhaust line can be up to
100 ft (30.5 m)
in length. Ideally this line should terminate outdoors in a location
that is not exposed to the elements. Connect the exhaust line to the monitor by firmly pushing the tubing onto
the Gas Sample Exhaust Port’s barbed fitting. Ensure that no loops or dips are present that could trap
condensate. This is likely as outside air can be cooler than instrument. Note that the exhaust line does not
require a termination filter.
Termination Filter (P/N 3015-3420)
Summary of Contents for 3015-4286
Page 16: ...12 Instruction 3015 4286 Notes ...