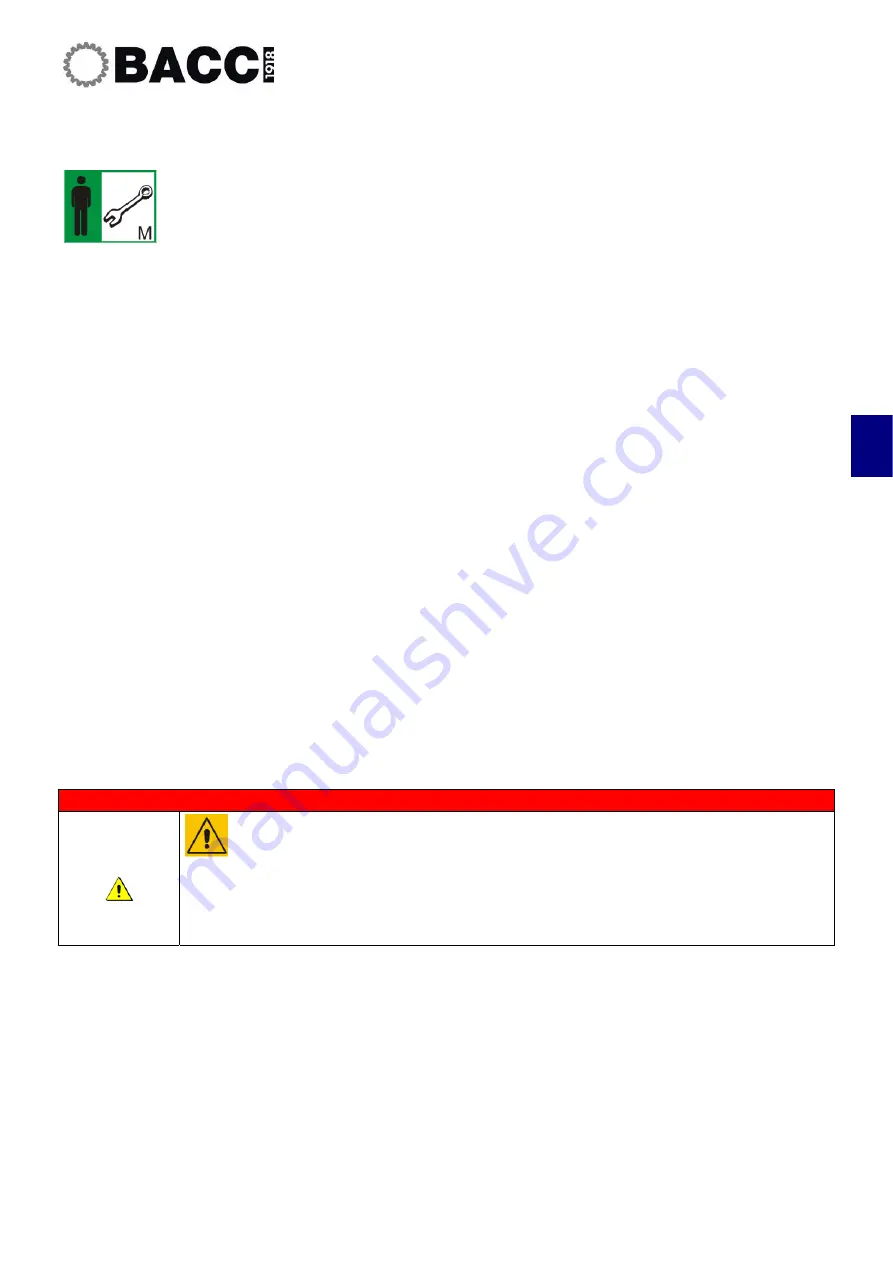
CHAPTER 5 –
Controls and use
Chap. 5
-
39
/48 -
5.8
Setup of piece support devices and presser clamps
5.8.1
Adjusting the pressers
The presser clamps may be adjusted in two ways:
•
In the first case, for example for a 50 mm piece, the clamps may be adjusted so that when they
are closed the minimum space is 45 mm. This prevents the risk of being crushed, as zero stroke
is never reached when there is no piece in the clamps. However, there is a large risk of being
crushed between two pieces, if the machined piece is not removed before another rough piece is
inserted. Moreover, crushing when there is no piece in the machine is against all machine use
logic and is to be considered an extraordinary event.
•
In the second case, again using a 50 mm piece as example, the clamps may be adjusted so that
the opening to insert the piece is 55 mm, and the 5 mm of space avoid the risk of inserting fingers.
This method is closer to actual machining requirements but is effective only if the rough pieces
are uniform and if they are positioned with the greatest care possible.
The importance and need to adjust the presses is a well-known fact, it is standard practice in machine
equipping and must be carried out only by the machine maintenance technician.
The risk of being crushed by the pressers is reduced by the measures adopted to attempt to contrast
possible lack of diligence with redundancy:
•
Presser adjustment by the maintenance technician during machine equipping.
•
The application of two pressure stages during loading/unloading and machining.
NOTE
Safety warning
DANGER!
Danger of the piece or tool parts flying off the machine.
An erroneous piece program or a piece program applied to a piece that is not blocked
properly may cause the tool to break and tool fragments to fly off the machine. Check the
piece program before starting machining.
Once the machine has been equipped, the operator in charge of running the machine must check that
the work cycle is executed as required. Generally, checks carried out in the original conditions are the
best. The only difference with the final cycle is that the operator holds the portable control and reduces
the machining speed using the potentiometer in order to be able to intervene quickly in the event of
programming or equipping errors, etc.
Summary of Contents for Twin
Page 4: ...TWIN Use and maintenance instruction manual Cap 0 IV 4 Page intentionally left blank ...
Page 5: ...CHAPTER 1 Foreword Chap 1 1 14 CHAPTER 1 Foreword ...
Page 7: ...CHAPTER 1 Foreword Chap 1 3 14 Page intentionally left blank ...
Page 18: ...TWIN Use and maintenance instruction manual Chap 1 14 14 Page intentionally left blank ...
Page 19: ...CHAPTER 2 Safety information Chap 2 1 52 CHAPTER 2 Safety information ...
Page 98: ...TWIN Use and maintenance instruction manual Chap 3 28 28 Page intentionally left blank ...
Page 99: ...CHAPTER 4 Installation Chap 4 1 20 CHAPTER 4 Installation ...
Page 119: ...CHAPTER 5 Controls and use Chap 5 1 48 CHAPTER 5 Controls and use ...
Page 166: ...TWIN Use and maintenance instruction manual Chap 5 48 48 Page intentionally left blank ...
Page 167: ...CHAPTER 6 Maintenance Chap 6 1 32 CHAPTER 6 Maintenance ...
Page 198: ...TWIN Use and maintenance instruction manual Chap 6 32 32 Page intentionally left blank ...
Page 202: ...TWIN Use and Maintenance Instruction Manual Chap 7 4 4 Page intentionally left blank ...