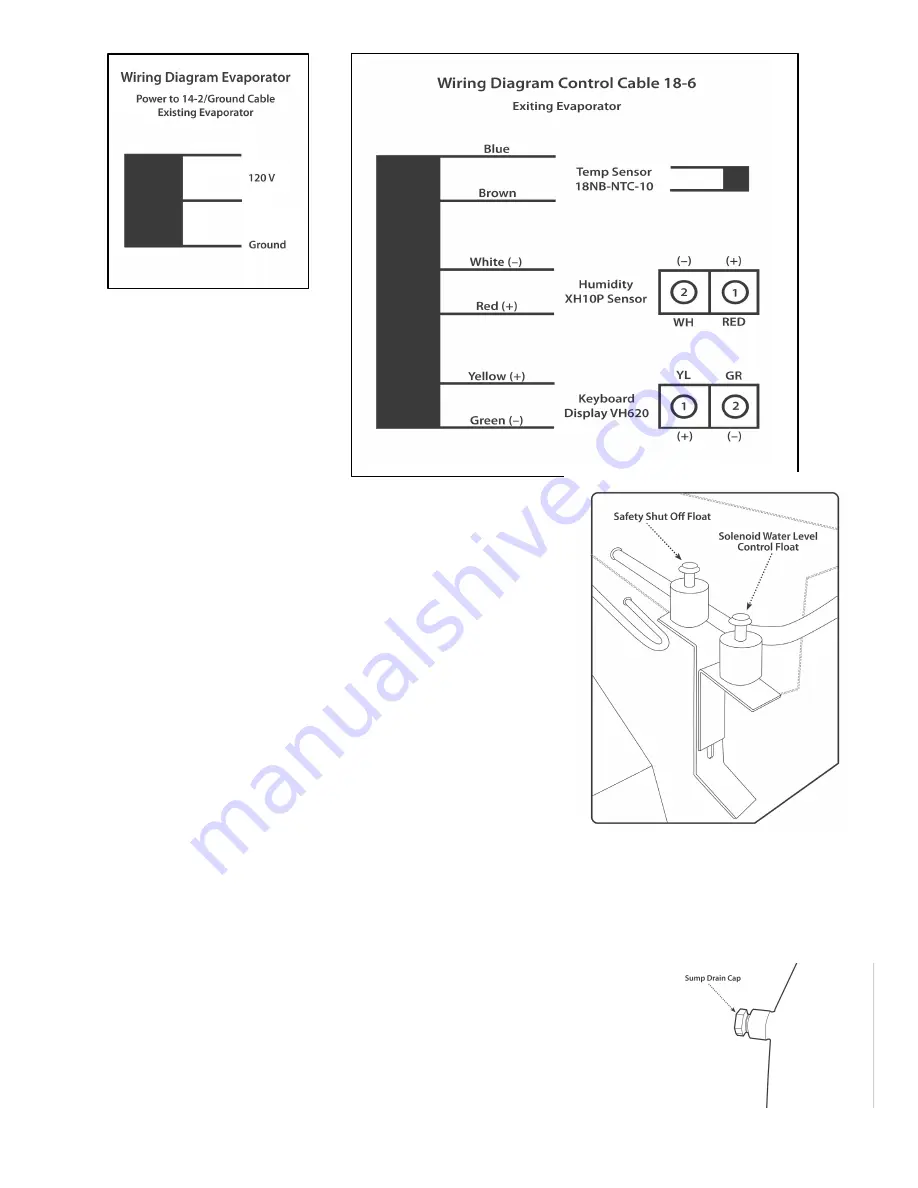
Charging the System
1. Evacuate and pressure test the system. This can be
accomplished by charging with nitrogen to 75 lbs
and checking your gauges for any sign of a leak.
Evacuate the system to 500 microns.
2. Charge the system with R134A until the sight
glass goes clear. Initial charge will be 6.3 pounds
of 134A; the pumpdown capacity of the receiver.
It is very important not to over charge this system.
As soon as the bubbles in the sight glass disappear,
discontinue charging. Over-charge will result in an
ice block in the evaporator.
3. Adjust the TXV to 12-14 degree’s of superheat.
Take your suction pressure and temperature reading at the condenser,
and add two pounds to it for the pressure drop.
Take the difference between actual temperature and
your reading from a PT chart to calculate.
4. System Start up. Before replacing stainless steel
enclosure cover, power up the system to make sure
water solenoid is opening correctly. The misting
nozzle will be open. Remove power and replace the
cover. Power up the evaporator, and let the system
pull down. At temp set point the refrigerant solenoid
will close and the system will pump down and shut
off the condensing unit.
5. Check level of safety float.
Breakers. We recommend a 30a fused disconnect.
Maintenance and Troubleshooting
Have your system checked each year by a certified refrigeration technician.
He should:
1. Clean the indoor and outdoor coils
2. Change the water filter on the Humidification models, and change out
the humidification mister head
3. Drain the Stainless steel sump (diagram #3), and clean it if necessary.
6