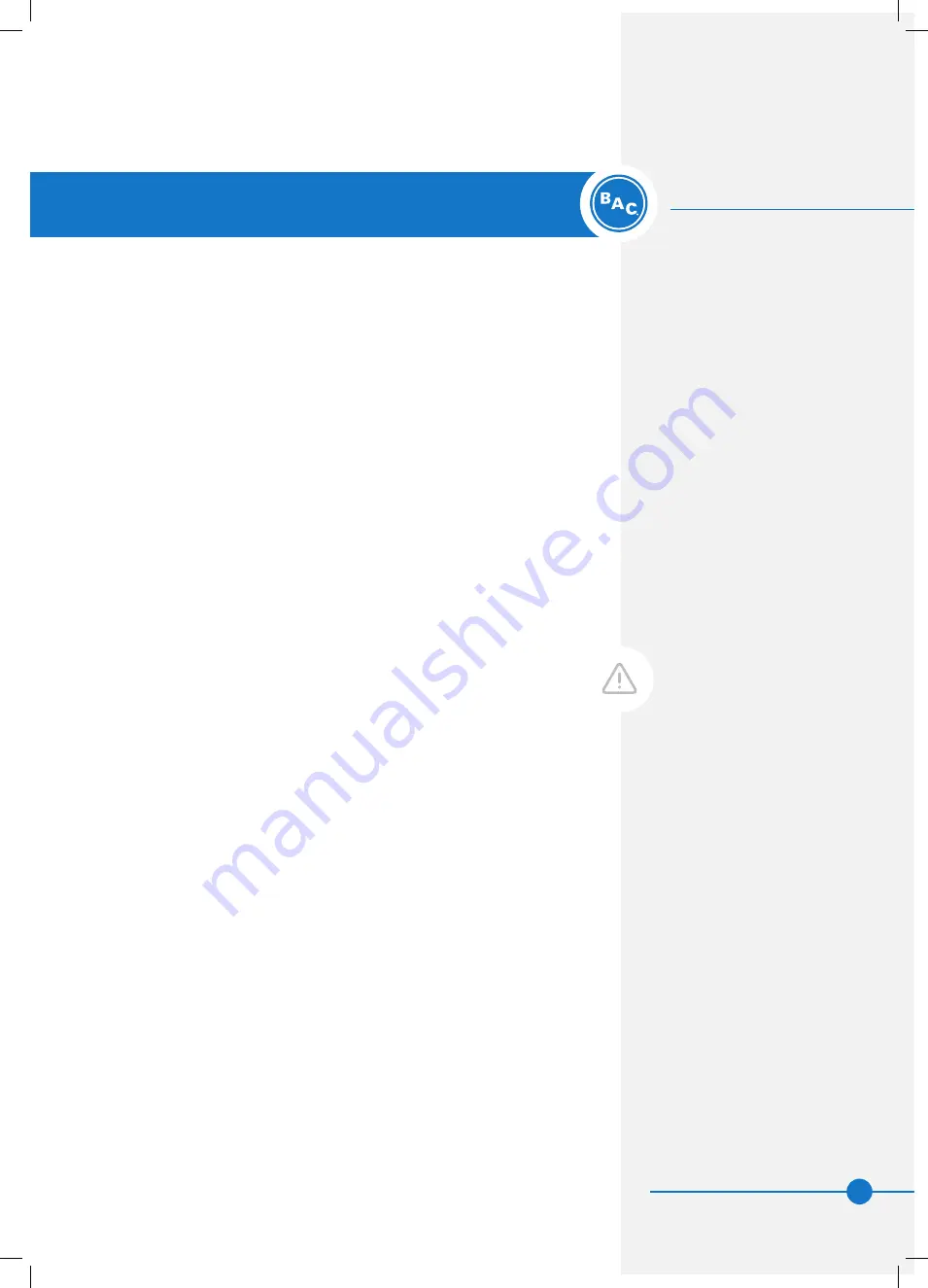
5
W W W . B A L T I M O R E A I R C O I L . C O M . A U
M A R 1 0 8 - 2
Extended Shutdown
Perform the following services whenever the unit is shutdown in excess
of three days:
• If the unit is mounted on vibration isolators or isolation rails (by
others), refer to the manufacturer’s guidelines before loading/
unloading weight from the unit.
• Disconnect, lock-out, and tag-out all fans and pumps.
• Close the shut-off valve in the make-up water line (supplied by
others) and drain all exposed make-up water piping. Heat trace and
insulate all exposed piping.
• Drain the cold water basin and all the piping that will be exposed to
freezing temperatures. Heat trace and insulate all exposed piping.
• Clean all the debris, such as leaves and dirt, from the interior and
exterior of the unit.
• Leave the cold water basin drain open so rain and melting snow will
drain from the tower.
• Clean the basin strainer and re-install.
• Cover the fan discharge to keep out dirt and debris.
• For PCT belt driven units, lubricate the fan shaft bearings, motor
base, and motor base adjusting screw.
• Apply RUST VETO
®
to steel shafts.
• Inspect the protective finish on the unit. Clean and refinish as required.
• Maintain the fan motor starting device in the “OFF” position to
ensure personal safety in the case of future inspection or service.
Operation and Maintenance
Initial & Seasonal Start-Up
Start-up
Extended Shutdown
WARNING:
Do not perform any
service on or near the fans,
motors, and drives, or inside
the unit without first ensuring
that the fans and pumps are
disconnected, locked out, and
tagged out.
Summary of Contents for PCT Series
Page 1: ...OPERATION MAINTENANCE MANUAL PCT Cooling Towers ...
Page 2: ......
Page 8: ...PCT COOLING TOWER Operation and Maintenance INITIAL AND SEASONAL START UP EXTENDED SHUTDOWN 1 ...
Page 26: ...PCT COOLING TOWER Water Treatment BLEED RATE BLEED LINE CALCULATIONS 3 ...
Page 36: ...PCT COOLING TOWER Factory Authorised Parts THE PERFECT FIT 5 ...