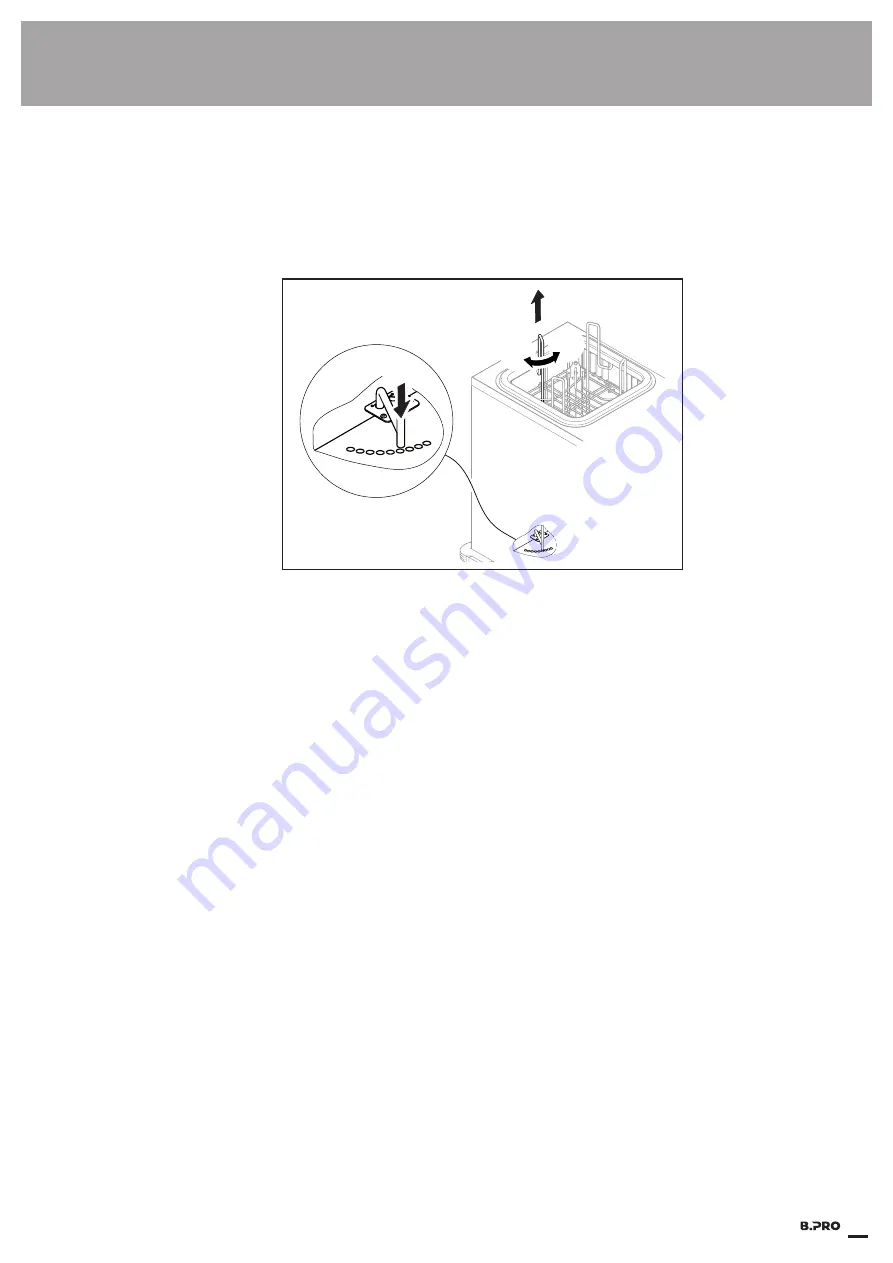
19
Mobile Plate Dispenser
OPERATING INSTRUCTIONS
Pull the guide rod upward (1.).
4.
1.
2.
3.
Turn the guide rod toward the centre of the tube (2.) if the diameter is to be reduced
– or –
Turn the guide rod toward the housing cover (3.) if the diameter is to be increased.
Lower the guide rod (4.) and insert it in the corresponding guide hole in the unit bottom.
Lock the guide rod's transport securing device
L
The distribution height of stacked items is adjusted using springs, which are used to mount
the stacking platform at the top of the unit housing.
L
Individual springs can be hooked/unhooked to adjust the distribution height of stacked items
if necessary.
L
The unit is supplied from the factory with fully hooked springs. We recommend testing the
distribution height of stacked items using this spring setting and making adjustments if ne-
cessary.
)
If a different type of stacked item is to be stacked at a later time and it is necessary to change
the distribution height of stacked items, either unhooked springs must be hooked in or additi-
onal springs unhooked.
)
The distribution height of stacked items is correctly adjusted when the top plate is positioned
above the unit cover.
Place 11 plates on the stacking platform.
If the top plate does not extend above the upper side of the unit or several plates extend abo-
ve the upper side of the unit, remove all plates and change the spring setting.
ª
Section "Setting the distribution height of stacked items"
Retest the distribution height of stacked items after changing the spring setting.
If necessary, repeat the spring setting change and testing of the distribution height of stacked
items until the correct setting is achieved.
Testing distribution height
of stacked items
Summary of Contents for TS-H1
Page 1: ...Translation of the original operating instructions PLATE DISPENSER TS H1 H2 UH2...
Page 6: ...6 Mobile Plate Dispenser OPERATING INSTRUCTIONS...
Page 49: ...49 Mobile Plate Dispenser OPERATING INSTRUCTIONS...
Page 50: ...50 Mobile Plate Dispenser OPERATING INSTRUCTIONS...
Page 51: ...51 Mobile Plate Dispenser OPERATING INSTRUCTIONS...