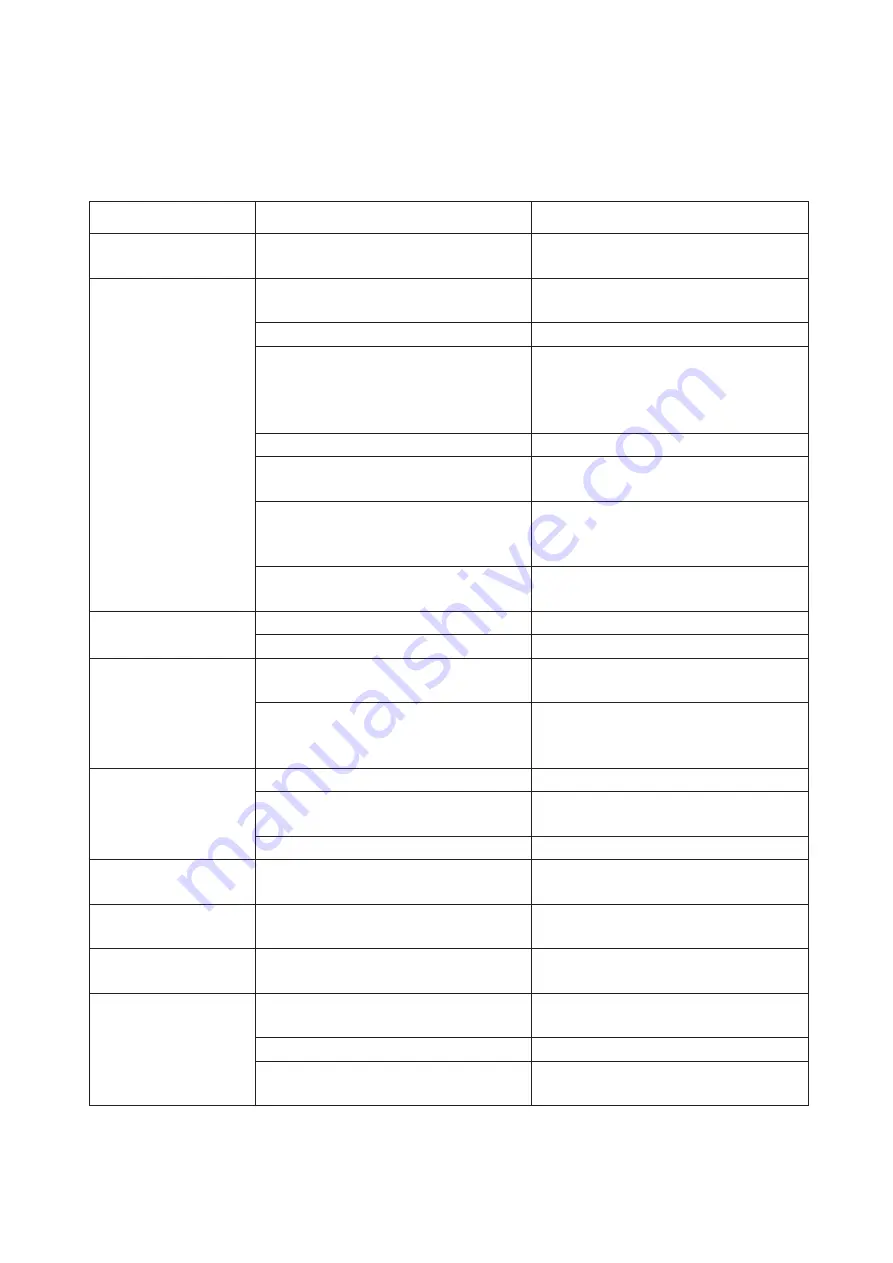
35
7-6. Troubleshooting
Symptoms of troubles, probable causes, and remedies are shown in the following table. For
adjustments, refer to the preceding section.
Symptom
Probable cause
Remedy
Pilot relay whines.
Stained valve stem (section hitting the port) Take out pilot relay and clean the valve stem
(section hitting the port)
No or only very low
controller output pressure
is delivered.
No air supply is provided or air supply
pressure is lower than 140 kPa {1.4 kgf/cm
2
).
Provide an air supply of correct pressure.
Restriction is clogged.
Take out and clean the restriction.
Restriction is not correctly installed.
Parts (restriction, blind plug, etc.) differ by
whether instrument is incorporated with
transmitter or not. Install correct parts at
correct positions.
Filter is stained.
Replace filter.
Air leak in nozzle circuit of controller unit. Check that O-rings are properly installed.
Securely tighten the controller unit.
Leak or clogging of A/M transfer circuit (for
instrument with A/M transfer provision)
Take out manual loader unit, inspect its
circuit, check that O-rings are properly
installed, and securely install the unit.
Leak in pilot relay diaphragm section
Take out pilot relay and inspect diaphragm.
If leak is found, replace diaphragm.
Controller output
pressure is too high.
Nozzle of controller unit is clogged.
Clean the nozzle.
Stained valve seat of pilot relay
Take out pilot relay and clean the valve seat.
Indication is with large
input offset.
SP or PV pointer is shifted.
Re-adjust deviation generating mechanism
and indicating mechanism.
Controller mechanism is not properly
adjusted. (Balancing of proportional band is
improper.)
Adjust balancing of controller mechanism.
Integral rate is shifted,
or integral action is
ineffective.
Damaged needle or seat
Replace needle assembly with new one.
Clamping screw of dial is loose.
Set the dial in the correct position and fix it
securely with screw.
Air leak of gasket
Securely fix to base.
Manual loading pressure
is low.
No air supply is provided or air supply
pressure is lower than 140 kPa {1.4 kgf/cm
2
}.
Provide proper air supply.
Manual loading pressure
is high.
Valve stem of pressure regulator valve is
stained or dusty.
Overhaul the pressure regulator.
Zero point shifts largely
when ranges are changed.
Transmitter section is not properly adjusted. Adjust and calibrate transmitter section.
Output is unstable or
pulsates.
Air leak
Check and correct air connections and
gaskets.
Stained nozzle/flapper
Clean the nozzle/flapper.
Stained pilot relay
Take out and clean the pilot relay. Replace it
as required.
Summary of Contents for KFDB
Page 1: ...OM2 6220 0000 Field Mounted Indicating Controller Model KFDB KFKB KFLB User s Manual...
Page 4: ......
Page 7: ...3 Fig 1 2 Layout of Internal Components...
Page 18: ...14...
Page 27: ...23...
Page 28: ...24...
Page 38: ...32 Fig 7 2 Maintenance of Controller Unit...
Page 42: ...36 Pneumatic Circuit Diagram...
Page 43: ......
Page 46: ......
Page 48: ......