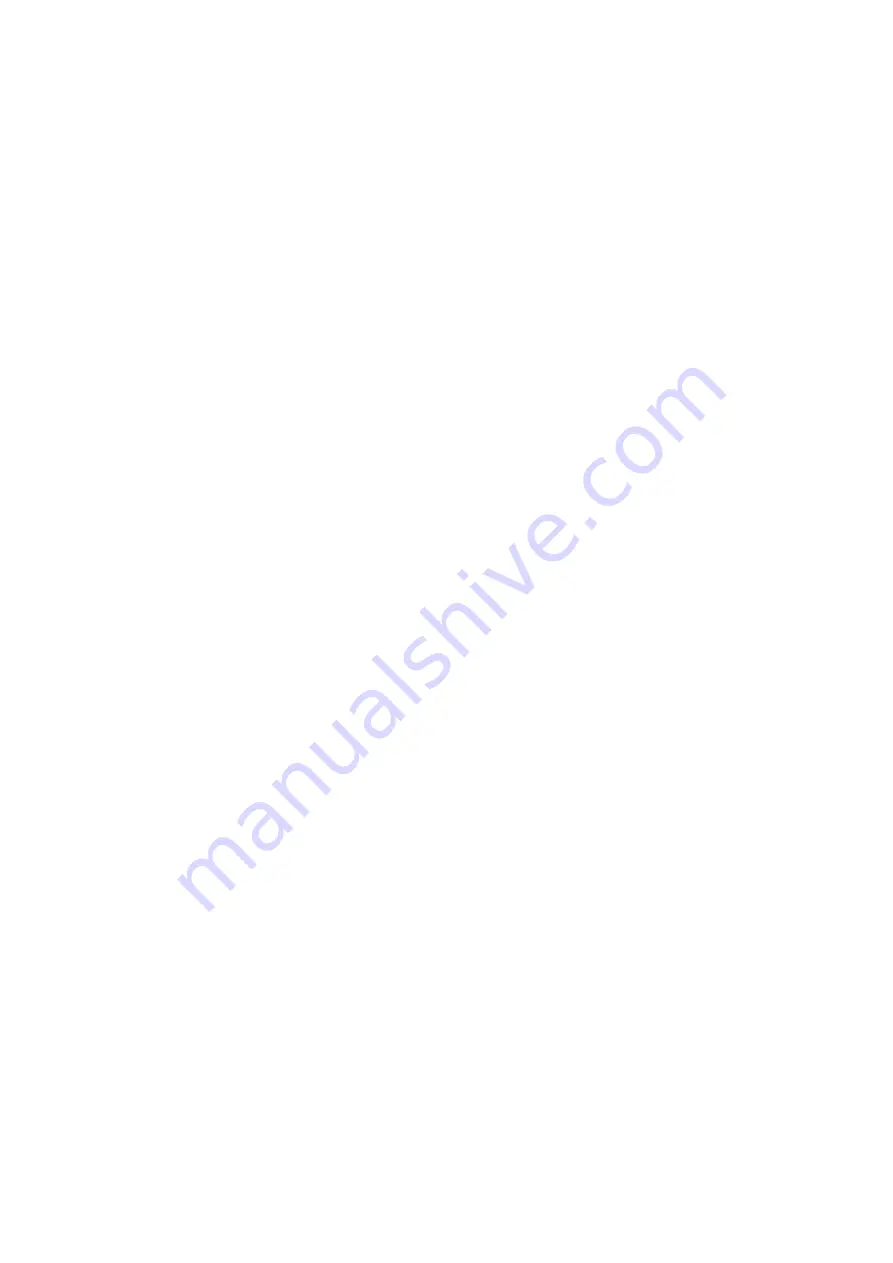
21
4-3-3. Data transfer
We distinguish between two types of data transfer:
Scheduled data transfer (cyclic): all time-critical process data (i.e. continuous measurement
or actuating signals) are transferred and processed in accordance with a fixed schedule.
Unscheduled data transfer (acyclic): device parameters that are not time-critical for the
process and diagnosis information are only transferred to the fieldbus when needed. This
data transfer is always carried out in the intervals between timed communication.
4-3-4. Device ID, addressing
Within the FF network, each fieldbus device is identified by a unique device ID (DEVICE_
ID). The fieldbus host system (LAS) automatically gives the network address for this to the
field device. The network address is the address that the fieldbus currently uses.
The Foundation Fieldbus™ uses addresses between 0 and 255:
Groups/DLL: 0 to 15
Devices in operation: 20 to 35
Reserve devices: 232 to 247
Offline/substitute devices: 248 to 251
The field device tag name (PD_TAG) is given to the device in question during commissioning
(see
→
page 27). It remains stored in the device even during a supply voltage failure.
4-3-5. Function blocks
The Foundation Fieldbus™ uses predefined function blocks to describe the functions of a
device and to specify uniform data access. The function blocks implemented in each fieldbus
device provide information on the tasks which a device can accept in the whole of the
automation strategy.
In the case of sensors these are typically the following blocks:
’Analog Input’ or
’Discrete Input’ (digital input)
Actuating valves normally have the function blocks:
’Analog Output’ or
’Discrete Output’ (digital output)
For control tasks there are the blocks:
PD controller or
PID controller
More information on this can be found from Chapter Chapter 9 onwards.
4-3-6. Fieldbus based process control
With the Foundation Fieldbus™ field devices can carry out simple process control functions
themselves, thereby relieving pressure on the superior process control system. Here the
Link Active Scheduler (LAS) coordinates data exchange between the sensor and controller
and makes sure that two field devices cannot access the bus at the same time. To do this,
configuration software such as the NI-FBUS Configurator from National Instruments is used
to connect the various function blocks to the desired control strategy . generally graphically
(
→